Biodiesel Manufacturing Plant Project Report 2024: Machinery and Technology Requirements
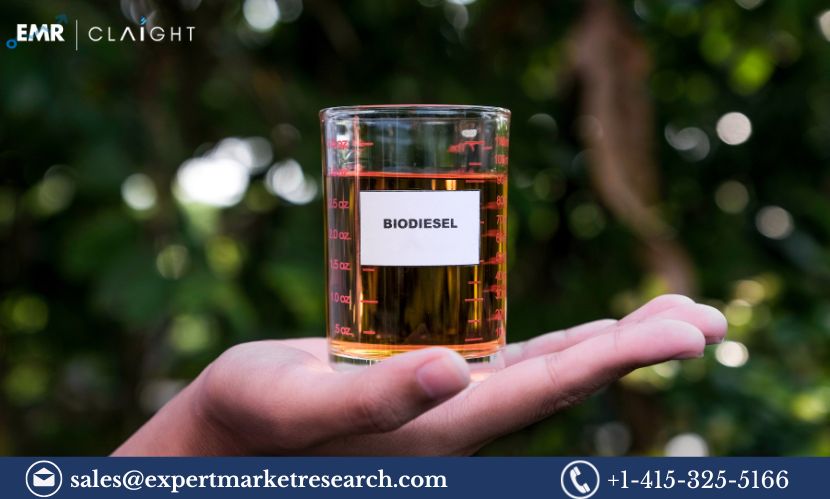
Introduction
Biodiesel is an eco-friendly alternative to conventional petroleum-based diesel, produced from renewable resources such as vegetable oils, animal fats, and recycled cooking oil. With the global push towards sustainability and reduced carbon emissions, biodiesel has emerged as a crucial component in the transition to greener energy solutions. Establishing a biodiesel manufacturing plant offers a promising business opportunity, driven by increased demand from both governmental and industrial sectors. This Biodiesel Manufacturing Plant Project Report outlines the essential elements of setting up a biodiesel production facility, including production methods, equipment requirements, market analysis, regulatory compliance, and financial planning.
Overview of Biodiesel
Biodiesel is a clean-burning, biodegradable fuel that can be used in standard diesel engines without modifications. It is produced through a chemical process called transesterification, where triglycerides in the feedstock react with an alcohol (usually methanol or ethanol) in the presence of a catalyst to produce fatty acid methyl esters (FAME) and glycerol. The FAME is the biodiesel, while glycerol is a byproduct that can be used in other industries.
Production Process of Biodiesel
The production of biodiesel involves several steps to ensure a high-quality end product:
Feedstock Selection: The choice of feedstock significantly impacts the cost and quality of the biodiesel. Common feedstocks include soybean oil, palm oil, rapeseed oil, animal fats, and recycled cooking oils.
Pre-treatment and Purification: The feedstock is filtered and purified to remove impurities and free fatty acids that could interfere with the transesterification process.
Transesterification Reaction: The purified feedstock is mixed with alcohol (methanol or ethanol) and a catalyst (typically sodium hydroxide or potassium hydroxide). This chemical reaction breaks down the triglycerides into biodiesel (FAME) and glycerol.
Separation and Washing: The mixture is separated into biodiesel and glycerol phases. The biodiesel is then washed to remove residual impurities, such as excess catalyst and soap, to achieve high purity.
Drying and Refining: The washed biodiesel is dried to remove any water content and refined to meet the required specifications.
Packaging and Storage: The final biodiesel is stored in tanks and packaged for distribution. Proper labeling and documentation are essential for compliance with industry standards.
Equipment and Infrastructure Requirements
Establishing a biodiesel manufacturing plant requires specialized equipment and infrastructure to ensure efficient and safe production:
Pre-treatment Units: Equipment for filtering and purifying feedstock.
Transesterification Reactors: Reactors capable of mixing feedstock, alcohol, and catalysts at controlled temperatures.
Separation Units: Centrifuges or decanters for separating biodiesel from glycerol.
Washing Systems: Systems for washing the biodiesel to remove impurities.
Drying Equipment: Equipment such as rotary dryers to remove moisture from the biodiesel.
Storage Tanks: For storing both raw materials and the finished product.
Quality Control Laboratory: For testing the biodiesel’s properties, including purity, viscosity, and combustion characteristics.
Packaging Equipment: Automated machines for filling, sealing, and labeling containers.
The facility must be designed for safety and compliance with environmental standards, including proper ventilation and containment systems to handle chemicals and waste.
Market Demand and Applications
The demand for biodiesel is growing, driven by the global shift towards sustainable energy and cleaner fuels:
Transportation Industry: Biodiesel is used in vehicles, including trucks, buses, and cars, as a renewable fuel source
Industrial Applications: Biodiesel is used in machinery and equipment to reduce carbon emissions.
Agriculture: Used as fuel for farm equipment and machinery.
Marine and Aviation: Biodiesel blends can be used in ships and aircraft engines, contributing to greener operations.
Several countries have implemented policies to promote biodiesel usage, which has increased demand for biodiesel production facilities. As governments aim to meet carbon reduction targets, incentives and subsidies for biodiesel production may also support the growth of this market.
Financial Planning and Investment
Starting a biodiesel manufacturing plant requires substantial initial investment. Key financial considerations include:
Capital Expenditure (CapEx): Costs for purchasing land, building the facility, and buying specialized equipment.
Operational Costs: Ongoing expenses such as raw material procurement, energy, labor, and maintenance.
Marketing and Distribution: Investment in creating brand recognition and establishing partnerships for distribution.
Regulatory Compliance: Costs related to meeting environmental regulations and obtaining necessary certifications.
A thorough financial analysis should include break-even analysis, cash flow projections, and ROI estimates to determine the feasibility and potential profitability of the project.
Regulatory and Safety Considerations
Compliance with local and international regulations is critical for operating a biodiesel plant:
Environmental Standards: Adherence to environmental protection laws to minimize emissions and waste.
Safety Regulations: Implementing safety protocols to handle flammable chemicals and prevent accidents.
Certification Requirements: Meeting standards set by organizations like ASTM International to ensure product quality.
Documentation and Reporting: Maintaining records of production and waste management for regulatory audits.
Employee safety training is essential to ensure workers are familiar with the handling of chemicals, equipment operation, and emergency procedures.
Challenges and Risk Management
Manufacturers may face challenges such as:
Raw Material Fluctuations: Price volatility of feedstocks can affect production costs.
Regulatory Hurdles: Navigating complex regulations can be time-consuming and costly.
Market Competition: Competing with larger, established biodiesel producers.
Product Quality Control: Maintaining consistent product quality in each batch.
Effective risk management strategies include securing long-term contracts with suppliers, investing in technology for quality control, and diversifying product offerings to include higher-value byproducts like glycerol.
Sustainability Practices
Incorporating sustainability practices can improve the plant’s environmental footprint and appeal to eco-conscious consumers:
Sustainable Feedstocks: Sourcing feedstocks from sustainable agricultural practices.
Energy Efficiency: Using renewable energy sources for the plant’s operations.
Waste Management: Recycling byproducts such as glycerol and reusing waste products.
Eco-friendly Packaging: Using biodegradable and recyclable packaging materials.
FAQsÂ
1. What are common feedstocks used for biodiesel production?
Vegetable oils (soybean, rapeseed, palm oil), animal fats, and recycled cooking oils.
2. What is transesterification?
A chemical reaction that converts triglycerides into biodiesel (FAME) and glycerol using an alcohol and catalyst.
3. How is biodiesel quality tested?
Through properties such as viscosity, purity, and combustion characteristics.
4. What challenges do manufacturers face?
Raw material costs, regulatory compliance, and competition.
5. How can sustainability be incorporated?
By using renewable energy, sustainable feedstocks, and eco-friendly practices.
6. What safety measures should be followed?
Adhering to safety protocols for chemical handling and equipment operation.
7. How is biodiesel stored and packaged?
In moisture-proof, airtight containers with proper labeling.
8. What regulations must be met?
Environmental standards, safety regulations, and certification requirements.
9. What byproducts are produced during biodiesel manufacturing?
Glycerol, which can be used in other industries.
10. What are key financial considerations for starting a plant?
Initial capital, operational costs, and potential revenue from biodiesel and byproducts.
Media Contact:
Company Name: Claight Corporation
Contact Person: Lewis Fernandas, Corporate Sales Specialist — U.S.A.
Email: [email protected]
Toll Free Number: +1–415–325–5166 | +44–702–402–5790
Address: 30 North Gould Street, Sheridan, WY 82801, USA
Note: IndiBlogHub features both user-submitted and editorial content. We do not verify third-party contributions. Read our Disclaimer and Privacy Policyfor details.