Glass Fiber Reinforced Concrete Manufacturing Plant Project Report 2024: Setup and Cost
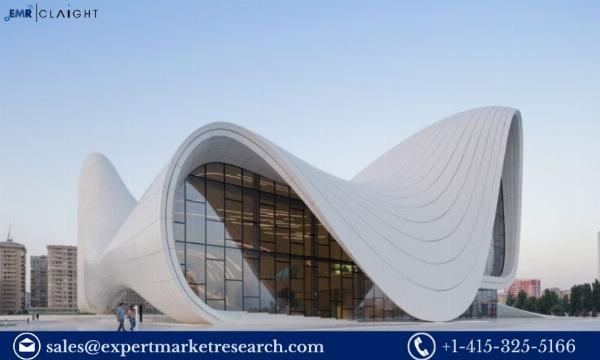
Introduction
Glass Fiber Reinforced Concrete (GFRC) is a high-performance composite material that combines traditional concrete with glass fibers to enhance its durability, flexibility, and aesthetic appeal. GFRC is increasingly used in architectural applications, including facades, cladding, and decorative features, due to its strength, lightweight nature, and ability to mimic various textures and finishes. The Glass Fiber Reinforced Concrete Manufacturing Plant Project Report provides a comprehensive overview of establishing a manufacturing facility for GFRC. This report covers market analysis, plant design, production technology, financial considerations, and regulatory requirements, offering valuable insights for investors, entrepreneurs, and industry professionals.
Market Analysis
Demand and Applications
GFRC is gaining popularity across various sectors due to its unique benefits:
Architectural Applications: GFRC is used for decorative panels, facades, and cladding in both residential and commercial buildings. Its versatility allows it to replicate traditional materials like stone or marble while being lighter and easier to handle.
Infrastructure: GFRC is used in infrastructure projects such as bridges and retaining walls due to its high durability and resistance to environmental factors.
Custom Design: The material's ability to be molded into various shapes and textures makes it ideal for custom designs and artistic features.
Sustainability: GFRC contributes to sustainable construction practices by reducing the need for heavier materials and offering improved longevity.
Get a Free Sample Report with Table of Contents @
https://www.expertmarketresearch.com/prefeasibility-reports/glass-fiber-reinforced-concrete-manufacturing-plant-project-report/requestsample
Competitive Landscape
The GFRC market is competitive, with key players and emerging companies striving to innovate and capture market share. Key factors influencing competition include:
Product Quality: High-quality GFRC that meets industry standards for strength, durability, and finish is essential for market success.
Innovation: Advances in GFRC formulations, such as improved fiber technology and enhanced mix designs, can provide a competitive edge.
Cost Management: Efficient production processes and raw material management are crucial for maintaining competitive pricing.
Distribution and Supply Chain: Strong distribution networks and reliable supply chains are important for meeting market demands and ensuring timely deliveries.
Plant Design and Technology
Plant Capacity and Layout
Designing a GFRC manufacturing plant involves several considerations, including capacity, layout, and workflow. A typical plant layout includes:
Raw Material Storage: Facilities for storing cement, glass fibers, aggregates, and other additives required for GFRC production.
Production Area: The core area where GFRC is manufactured, including mixing, casting, curing, and finishing processes.
Quality Control Laboratory: A dedicated space for testing the GFRC for quality, strength, and other performance characteristics.
Packaging and Storage: Facilities for packaging finished GFRC products and storing them until they are ready for distribution.
Utility and Support Systems: Includes systems for waste management, water treatment, and HVAC to maintain optimal production conditions.
Production Technology
The production of GFRC involves several key processes:
Raw Material Preparation: The primary materials for GFRC include cement, glass fibers, fine aggregates, and additives. These materials are prepared and measured according to the specific GFRC mix design.
Mixing: The raw materials are mixed to form a homogeneous slurry. Glass fibers are added to the mix to enhance the concrete's tensile strength and flexibility.
Casting: The GFRC mix is poured into molds or formwork to create panels, tiles, or other desired shapes. The use of molds allows for a wide range of textures and finishes.
Curing: The cast GFRC is cured under controlled conditions to ensure proper hydration and strength development. Curing may involve wetting the surface or using curing compounds.
Finishing: After curing, the GFRC products are finished to achieve the desired appearance. This may include surface treatments, polishing, or coating.
Quality Control: Comprehensive testing is conducted to ensure the GFRC meets specifications for strength, durability, and surface quality.
Packaging: Finished GFRC products are packaged and prepared for distribution, ensuring they are protected from damage during transport.
Modern manufacturing facilities use advanced technologies and automation to enhance production efficiency, ensure product quality, and reduce operational costs.
Financial and Economic Considerations
Investment and Cost Analysis
Setting up a GFRC manufacturing plant involves significant investment. Key financial considerations include:
Land and Building: Costs for acquiring and developing the facility, including production, storage, and quality control areas.
Machinery and Equipment: Includes mixing machines, molds, curing systems, finishing equipment, and packaging lines.
Raw Materials: Costs for cement, glass fibers, aggregates, additives, and other materials used in GFRC production.
Labor: Expenses for hiring skilled workers, including operators, quality control staff, and maintenance personnel.
Utilities: Costs for electricity, water, and waste management, which are significant due to the energy requirements of concrete production.
A detailed financial plan should account for these initial investments and ongoing operational costs. Effective cost management and efficient production processes are crucial for achieving profitability.
Return on Investment (ROI)
ROI for a GFRC manufacturing plant depends on factors such as production efficiency, market demand, and cost control. By optimizing manufacturing processes, maintaining high product quality, and implementing effective marketing strategies, businesses can enhance ROI and establish a strong market presence.
Regulatory and Environmental Considerations
Compliance
Manufacturing GFRC involves adhering to various regulations:
Industry Standards: Compliance with industry standards and specifications for GFRC to ensure product quality and performance.
Health and Safety Regulations: Ensuring a safe working environment and proper handling of materials, including protective equipment for workers.
Environmental Regulations: Managing emissions and waste to minimize environmental impact. This includes recycling waste materials and optimizing resource use.
Labeling Requirements: Accurate labeling of products, including compliance with industry standards and safety information.
Environmental Impact
The production of GFRC involves material use and generates waste. Implementing waste reduction strategies, recycling materials, and using energy-efficient technologies are essential for minimizing environmental impact. For example, incorporating waste recycling systems can help reduce raw material consumption and waste generation.
FAQs
What is Glass Fiber Reinforced Concrete (GFRC)?
GFRC is a composite material made by combining traditional concrete with glass fibers. It is used in architectural applications for its enhanced durability, flexibility, and aesthetic appeal.
How is GFRC manufactured?
GFRC is manufactured by mixing cement, glass fibers, aggregates, and additives, then casting the mixture into molds. After curing, the GFRC products are finished and tested for quality.
ย What factors should be considered when setting up a GFRC manufacturing plant?
Key factors include understanding market demand, designing an efficient plant layout, selecting appropriate production technology, managing investment and operational costs, and ensuring regulatory compliance.
What are the environmental impacts of GFRC production?
The production process involves material use and generates waste. Implementing waste reduction strategies, recycling materials, and using energy-efficient technologies are important for reducing environmental impact.
ย How profitable is a GFRC manufacturing plant?
Profitability depends on factors such as production efficiency, market demand, and cost management. With effective operations, high-quality products, and strategic marketing, a GFRC manufacturing plant can achieve favorable returns on investment.
Media Contact:
Company Name: Claight Corporation
Contact Person: Lewis Fernandas, Corporate Sales Specialist โ U.S.A.
Email: [email protected]
Toll Free Number: +1โ415โ325โ5166 | +44โ702โ402โ5790
Address: 30 North Gould Street, Sheridan, WY 82801, USA
Website: www.expertmarketresearch.com
Aus Site: https://www.expertmarketresearch.com.au
Note: IndiBlogHub features both user-submitted and editorial content. We do not verify third-party contributions. Read our Disclaimer and Privacy Policyfor details.