Common Real World Application of Physical Vapor Deposition
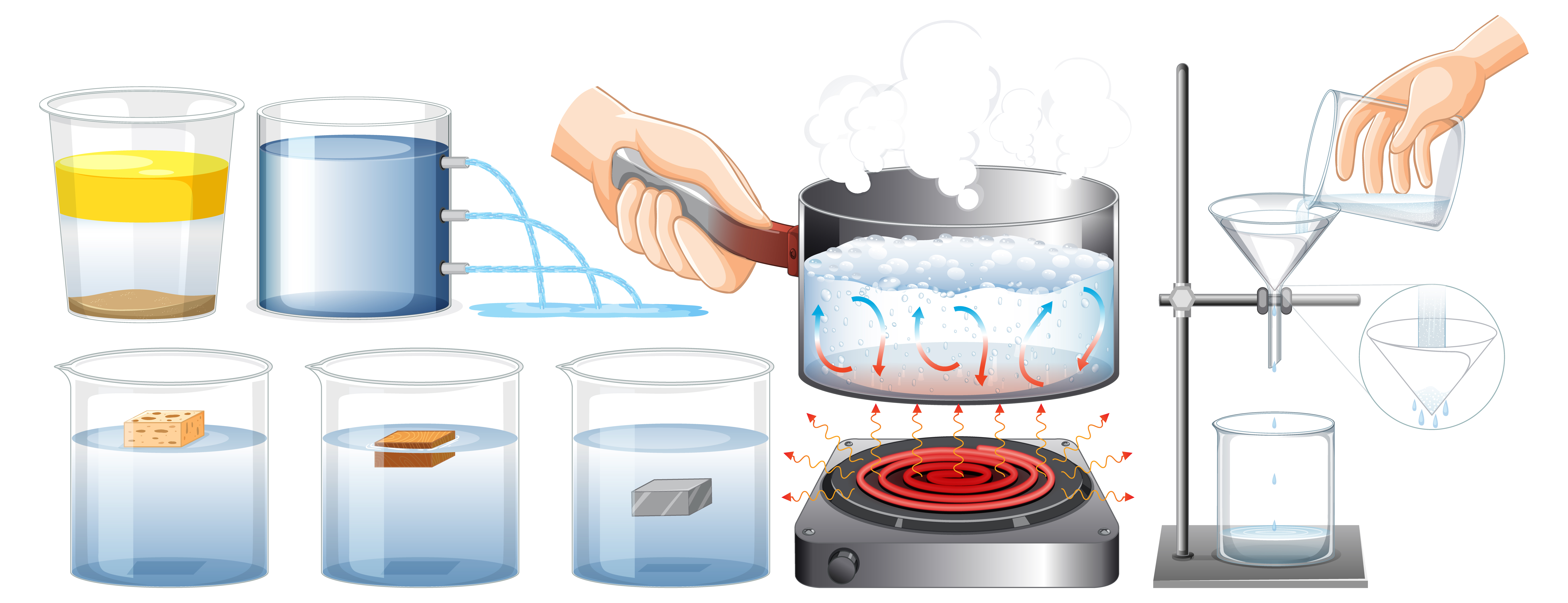
Thin-film deposition technologies, like physical vapor deposition (PVD) or chemical vapor deposition (CVD), have long been associated with manufacturing microelectronics and sensors.However, their application extends beyond these specialized areas to everyday products, a fact less known to many. Manufacturers have been utilizing these techniques since the 1930s, embedding them into various commonplace items.
From improving the durability of cutting tools to adding anti-reflective properties to eyeglass lenses, thin-film deposition technologies have quietly transformed numerous consumer goods. In this article, we shall discuss some of the common uses of PVD in the real world, so continue reading.
How Does PVD Coating Work?
Physical vapor deposition (PVD) coating is a method for applying thin layers of material to a surface. The process occurs within a vacuum chamber, where solid material evaporates through heating, forming a plasma.
This vapor then settles onto the surface, creating a thin film. Techniques like sputtering or evaporation control the deposition process. PVD coatings offer excellent adhesion, hardness, and corrosion resistance, making them valuable for enhancing surface properties in various automotive, aerospace, and electronics industries.
Common Uses of PVD Coating Across Various Industries
Cutting Tools
One of the primary applications of PVD static dissipation is cutting tools used in machining operations. Tools coated with PVD exhibit exceptional wear resistance and prolonged tool life, thereby reducing downtime and enhancing productivity. Industries such as automotive, aerospace, and general manufacturing rely on PVD-coated cutting tools for precision machining, higher cutting speeds, and cost-effective operations.
Decorative Finishes
PVD coatings have found widespread acceptance in the realm of decorative finishes, where aesthetics and durability are paramount. From architectural elements to consumer goods, PVD-coated surfaces offer vibrant colors, superior corrosion resistance, and ease of maintenance. Door handles, bathroom fixtures, and jewelry are just a few examples where PVD coatings elevate the visual appeal while ensuring long-lasting performance indoors and outdoors.
Medical Devices
In the healthcare sector, PVD coatings play a critical role in enhancing the functionality and safety of medical devices. Surgical instruments and orthopedic implants benefit from the superior surface hardness, wear resistance, and antibacterial properties of PVD static dissipation. These coatings extend the lifespan of medical devices and contribute to improved patient outcomes by minimizing the risk of contamination and wear-related failures.
Automotive Components
The automotive industry extensively utilizes PVD coatings to enhance the performance and aesthetics of various components. Engine parts, wheels, and trim elements coated with PVD exhibit superior corrosion resistance, scratch resistance, and UV stability. Apart from extending the lifespan of automotive parts, PVD coatings contribute to fuel efficiency, reduced maintenance, and enhanced visual appeal, thereby meeting the evolving demands of consumers and regulatory standards.
Tooling and Molding
PVD coatings have wide-ranging applications in tooling and molding processes across plastics and glass manufacturing industries. PVD coatings optimize production efficiency and product quality by imparting superior release properties, abrasion resistance, and thermal stability to molds and dies. Reduced downtime, improved productivity, and higher-quality finished products are among the key benefits derived from the use of PVD-coated tooling and molding equipment.
Electronics
The electronics industry relies on PVD coatings to enhance the performance and reliability of various components, including semiconductor devices, circuit boards, and connectors. PVD coatings offer electrical insulation, thermal management, and corrosion protection, extending electronic devices' lifespan and functionality in demanding environments. PVD-coated components enhance product performance, reliability, and longevity from consumer electronics to industrial equipment.
Optical Coatings
PVD technology is pivotal in producing optical coatings used in lenses, mirrors, and filters across diverse optical systems. By enhancing light transmission, reducing glare, and improving scratch resistance, PVD coatings contribute to sharper imaging and extend equipment lifespan in applications ranging from cameras to laser devices. The optical clarity and durability provided by PVD coatings are indispensable in industries where precision and reliability are paramount.
Note: IndiBlogHub features both user-submitted and editorial content. We do not verify third-party contributions. Read our Disclaimer and Privacy Policyfor details.