Detailed Material Takeoff in civil works
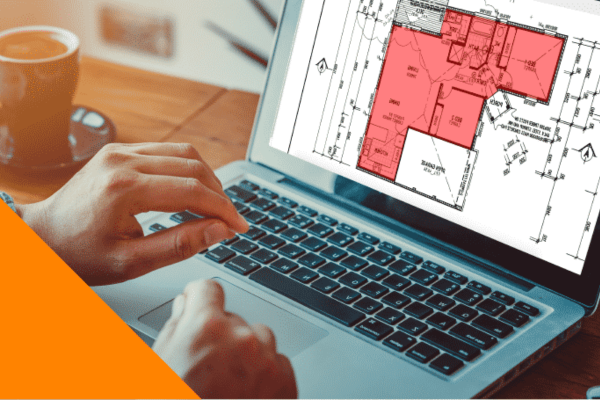
In the realm of civil construction, the success of any project hinges on meticulous planning and resource management. One vital aspect that often determines whether a project stays within budget and timeline is the Detailed Material Takeoff (MTO). This process involves systematically identifying and quantifying every material required, ensuring that construction progresses smoothly without unexpected shortages or costly overruns. Whether you’re building roads, bridges, or buildings, mastering a detailed material takeoff is essential for efficient project execution and cost control.
What is Detailed Material Takeoff?
Detailed Material Takeoff is the process of quantifying the exact amount of materials required for a construction project. It involves extracting data from project drawings, blueprints, and specifications to list every item and material necessary to complete the work. Unlike rough estimates, a detailed MTO provides a precise inventory of materials down to the smallest units, such as the number of bricks, cubic meters of concrete, kilograms of steel, and so forth.
This detailed inventory acts as a bridge between design and procurement, enabling contractors, engineers, and project managers to plan purchases, avoid wastage, and ensure smooth progress without material shortages.
Importance of Detailed Material Takeoff in Civil Works
1. Accurate Budgeting and Cost Estimation
An accurate MTO is the cornerstone of reliable project budgeting. When you know the exact quantity of materials needed, it’s easier to obtain competitive quotations from suppliers, minimize contingency costs, and reduce the risk of budget overruns.
2. Efficient Resource Management
Material wastage is a common challenge in civil works. By performing a detailed takeoff, contractors can order materials in precise quantities, reducing excess inventory and minimizing storage issues. This efficiency also improves cash flow by preventing unnecessary bulk purchases.
3. Streamlined Project Scheduling
Knowing the quantity and timing of material deliveries helps in scheduling various phases of construction. Detailed MTO aids in planning site activities, manpower deployment, and machinery usage, leading to better project coordination and timely completion.
4. Improved Communication and Transparency
A detailed material list fosters clear communication among architects, engineers, contractors, and suppliers. Everyone involved can understand material requirements, reducing disputes and ensuring accountability.
5. Compliance and Quality Control
Certain civil works require adherence to strict standards and specifications. A detailed takeoff ensures that the correct types and grades of materials are procured, supporting compliance with industry regulations and quality benchmarks.
Steps to Prepare a Detailed Material Takeoff
Step 1: Review Project Documents
The first step involves thoroughly reviewing the architectural, structural, mechanical, and civil drawings, along with technical specifications and project schedules. Understanding these documents is vital to identify every material required for the scope of work.
Step 2: Break Down the Project Into Components
Divide the project into smaller, manageable sections such as foundations, slabs, walls, columns, beams, roofing, and finishes. This segmentation helps in organizing the takeoff process and reduces the risk of missing any components.
Step 3: Quantify Each Material Item
Carefully measure and calculate the quantities of each material required in every section. For example, calculate the volume of concrete in foundations and slabs, the number of bricks in walls, the length and diameter of reinforcement steel, and the area of plastering or flooring.
Step 4: Cross-Verify Measurements
Verification is crucial to ensure accuracy. Cross-check your quantities with project specifications, consult structural engineers for reinforcement details, and use digital tools or software to minimize human error.
Step 5: Compile the Material List
Create a comprehensive list or spreadsheet that details every material with units, quantities, specifications, and sometimes unit costs. This list should be clear and easy to interpret by procurement teams and suppliers.
Step 6: Update and Revise as Necessary
Projects evolve, and designs may change during execution. Keep the material takeoff updated with any revisions to maintain accuracy and relevance throughout the project lifecycle.
Tools and Software for Material Takeoff
Modern civil engineering has greatly benefited from digital tools designed to streamline the MTO process. Some popular software solutions include:
• AutoCAD and Revit: For extracting quantities directly from 2D and 3D models.
• PlanSwift and Bluebeam Revu: Specialized takeoff software that allows digital measurement and quantity extraction from drawings.
• Microsoft Excel: Widely used for organizing and calculating quantities and costs.
• Building Information Modeling (BIM): Advanced BIM tools automate takeoff by integrating design, material, and cost data.
Using these tools reduces manual errors, speeds up the takeoff process, and enhances collaboration among project stakeholders.
Challenges in Material Takeoff and How to Overcome Them
1. Incomplete or Inaccurate Drawings
Incomplete drawings can lead to missed materials or incorrect quantities. Collaborate closely with the design team to ensure all drawings and specifications are final and comprehensive.
2. Human Errors in Measurement
Manual takeoffs are prone to errors. Implement peer reviews and use digital tools to verify quantities.
3. Changes During Construction
Design modifications during execution can disrupt the material plan. Maintain flexibility by updating the MTO regularly and communicating changes promptly to procurement and site teams.
4. Complexity of Large Projects
Large civil projects may involve thousands of material items. Breaking down the project into smaller units and using specialized software can make the process more manageable.
Conclusion
Detailed Material Takeoff is an indispensable part of civil works, impacting cost control, scheduling, and quality assurance. By meticulously quantifying all materials required for a project, stakeholders can avoid costly delays, minimize wastage, and ensure smooth project delivery.
Investing time and effort into a comprehensive MTO early in the project lifecycle leads to better decision-making and contributes significantly to the overall success of any civil construction endeavor.
For construction professionals and enthusiasts visiting IndiBlogHub, mastering the art of detailed material takeoff can be a game-changer—enhancing accuracy, efficiency, and profitability in civil works projects.
Note: IndiBlogHub features both user-submitted and editorial content. We do not verify third-party contributions. Read our Disclaimer and Privacy Policyfor details.