Eco-Friendly 3D Printer Materials Worth Trying
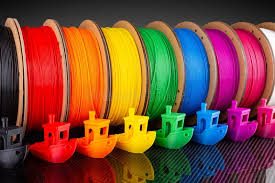
1. Why “Greener” Printing Matters
Nobody gets into 3D printing because they want to fill up landfills. But with every print comes a little scrap—failed pieces, support structures, leftover filament, empty spools. It adds up. Traditional plastics can stick around for centuries, and many are made from fossil fuels. Combine that with the power it takes to melt and move the stuff, and it’s easy to see how even small-scale printing can leave a bigger mark than we think.
That’s why eco-friendly 3D printing materials are gaining attention. These aren’t just about good feelings or trendy labels. Many come from renewable sources, take less energy to produce, and in some cases, even compost at the end of their life. Better yet, a lot of them are actually pleasant to work with—less smell, less cleanup, often less mess. If you care about the planet (or just want a less toxic printroom), greener materials are a smart step forward.
2. What Makes a Material Eco-Friendly?
The term “eco-friendly” gets thrown around a lot, but what does it really mean for 3D printing? Generally, a material is more sustainable if it checks one or more of these boxes:
• Made from renewable sources like plants, algae, or food waste instead of petroleum.
• Uses recycled content, meaning it’s made from plastic that already existed.
• Takes less energy or water to produce.
• Safer to use, giving off fewer harmful fumes or chemicals.
• Can break down naturally—either through composting or recycling.
Just because something is plant-based doesn’t mean it’s guilt-free, and just because it’s recycled doesn’t mean it prints well. But when these materials are used thoughtfully, they really can lighten your environmental footprint.
3. Waste Happens: Print Efficiently
Before switching materials, it helps to look at how you print. The most sustainable spool is the one you don’t waste. Failed prints, over-supporting, stringy layers, poor adhesion—all of it adds up. Even the greenest filament gets less green if you need three attempts to get it right.
So: calibrate your machine, design with minimal supports, use proper retraction settings, and dry your materials. These habits save plastic, time, and frustration—no matter what material you’re using.
4. Plant-Based Filaments
PLA, Reinvented
Polylactic acid (PLA) is probably the best-known eco filament. It’s made from plants—usually corn or sugarcane—and gives off a slightly sweet smell when printed. It’s easy to use, prints at low temperatures, and doesn’t need a heated bed. Newer blends are tougher than the brittle stuff you may have tried a few years back, and many now resist warping and cracking under sunlight.
PLA is compostable—but only in industrial facilities. Don’t expect it to break down in your garden or backyard. Still, compared to petrochemical plastics, it’s a big improvement.
PHA and PHB Blends
PHA (polyhydroxyalkanoate) and PHB (polyhydroxybutyrate) are lesser-known but promising players. Made by bacteria that digest sugars or oils, these are natural bioplastics. Mixed with PLA, they make prints tougher, more flexible, and slightly more heat-resistant. These blends often break down more readily than plain PLA when composted properly.
5. Recycled Plastic Filaments
rPETG – From Bottles to Brackets
Recycled PETG (rPETG) is made from old water bottles, packaging scraps, or post-consumer waste. It prints like standard PETG—tough, slightly flexible, and pretty forgiving—but it’s sourced from stuff that would otherwise become trash. It’s ideal for brackets, enclosures, or household tools.
Dry it well and print a bit slower if needed. It may be a bit more prone to stringing, but the tradeoff is worth it.
Recycled ABS
ABS has a reputation for strength and warp-prone frustration. Recycled ABS tones down the guilt by using recovered materials from appliances or electronics. It’s still not a perfect “green” option—it gives off fumes and needs ventilation—but using recycled stock is a meaningful step. Expect slightly darker colors and good mechanical properties.
Grinding and Re-Extruding at Home
If you generate lots of waste plastic, consider a small shredder and extruder. With some patience and trial runs, you can reprocess prints into new filament. It takes effort and tinkering, but the reward is a near-zero-waste workflow.
6. Bio-Based Nylons
Nylon 11 (PA11) from Castor Beans
Nylon 11 is one of the few high-performance filaments made from plants—in this case, castor oil. It’s strong, flexible, and more UV-stable than traditional nylon. It prints at high temperatures but doesn’t require extreme drying, and it has better layer adhesion than PA12 in many cases.
Use it for parts that need to bend without breaking—hinges, clips, or sports gear.
Partially Bio-Based PA12
Some PA12 filaments now include a percentage of castor-derived content. The rest is still fossil-based, but even partial shifts can reduce the environmental load. These blends are usually just as tough and consistent as standard PA12.
7. Natural Fiber-Filled Filaments
Wood-Filled PLA
PLA mixed with fine wood dust prints easily and smells fantastic. It has a matte finish that looks almost like stained wood, and it can be sanded or painted. Best of all, it’s lightweight and prints on most machines without upgrades.
Perfect for display pieces, toy parts, or anything decorative.
Other Fibers: Bamboo, Hemp, Coffee, and More
Many companies are getting creative with fillers. Bamboo fibers add a soft beige tint and grainy look. Hemp provides extra strength and a natural rough texture. Coffee grounds give a dark, rich tone (and sometimes a faint aroma). Cork, flax, algae, and even coconut shell have been used.
These all behave a lot like wood-filled PLA—use a larger nozzle, print a bit slower, and enjoy the aesthetic.
8. Support Materials with a Softer Impact
PVOH and BVOH
These water-soluble support materials dissolve in warm water, making clean-up a breeze. While they’re not biodegradable in the garden, they do reduce the waste left behind in complex prints. Just don’t pour large amounts down the drain—moderation is key.
Starch-Based Snap-Off Supports
Some materials blend plant starch with PLA to make support sticks that break away easily. These are simpler to manage than dual-material dissolvables and can often compost with PLA scraps.
9. Eco-Forward Resins for SLA Printing
Soy-Based Resins
Some resins now use soy derivatives instead of styrene or petroleum-based acrylates. These tend to have lower fumes and are slightly less harsh to handle. They cure similarly to standard resins and work well for models or figurines.
While not fully biodegradable, they’re a step toward lower-impact resin printing.
Lignin-Infused Resins
Lignin, the tough stuff that holds wood together, can replace a portion of resin base chemicals. It adds a natural color and boosts UV resistance while reducing the amount of synthetic compounds needed. Ideal for display prints or structural parts with a natural look.
Plant Oil and Terpene-Based Options
Emerging formulations are using oils from citrus peels and other waste plants. These create less odor and often cure faster. Some are also safer to rinse or wash without harsh solvents.
10. Recycled and Natural Powders (SLS & Binder Jetting)
For powder-based systems, some vendors now offer recycled metal powders or ceramic blends using waste material. These don’t directly affect most desktop users, but as the technology trickles down, it's encouraging to see industrial suppliers focus on sustainable sourcing.
In binder jetting, reclaimed steel or bronze powders are gaining traction—often from post-manufacturing scrap.
11. Sustainable Packaging
A surprising amount of plastic waste comes from filament packaging. Thankfully, more brands are now using:
• Cardboard spools that can be composted or recycled.
• Refillable systems, where filament comes in coils instead of on a full spool.
• Paper or compostable bags instead of plastic sleeves.
Keep your eyes open and support packaging that’s part of the solution.
12. Tips for Working with Eco Materials
• Dry it well – Bio-based and recycled materials can absorb moisture faster. Use a dry box or dehumidifier.
• Use larger nozzles – Fiber-filled materials can clog 0.4mm nozzles. Go 0.6mm or 0.8mm when you can.
• Print slow and cool – Some blends (like wood PLA) burn if too hot. Start at 200°C or lower.
• Vent when needed – Just because a material is plant-based doesn’t mean it’s 100% safe. Always err on the side of airflow.
• Experiment – Don’t be afraid to tweak retraction or speed settings. Some eco-filaments are trickier but worth it.
13. End of Life: What to Do with Failed Prints
Even the best-laid prints sometimes fail. Here’s what you can do:
• Compost PLA and blends – If you have access to industrial composting, collect scraps in a bin and drop them off.
• Recycle – Some local recycling centers now accept clean 3D prints made from specific materials. Call ahead.
• Grind and reuse – Invest in a shredder and make new filament. It’s hands-on but rewarding.
• Art and crafts – Reuse scraps in jewelry, mosaic, or model building.
And if all else fails: minimize supports, optimize orientation, and print only what you need.
14. Designing with the Planet in Mind
You can be eco-minded even before you hit “print.” Here’s how:
• Use minimal infill for strength without bulk.
• Design for no supports by orienting or reshaping models.
• Make hollow parts to save material and time.
• Print in parts that snap together instead of huge solids.
• Test with mini versions before scaling up.
Sustainable printing isn’t just about material—it’s about mindful design.
15. What’s Next for Eco Printing?
The future is bright—and greener.
• Algae-based plastics are being explored as carbon-negative materials.
• Mushroom mycelium composites might replace foams or filler cores.
• Printable enzymes could let certain plastics break down on demand.
• Aqueous resins may soon cure with just water rinses—no more alcohol baths.
• Cold spray metals and repairable prints might reduce replacements.
As the tech matures, expect to see more smart materials that balance performance, safety, and environmental care.
16. Final Thoughts
Eco-friendly 3D printing isn’t about perfection—it’s about direction. You don’t have to overhaul everything overnight. Just try one new spool: maybe a recycled PETG, a coffee-infused PLA, or a soy-based resin. See how it performs, dial in your settings, and go from there.
Each small change adds up. A better spool here, smarter design there, fewer failed prints over time—it all reduces waste. And along the way, you might just find some materials you like better than the old standbys.
Note: IndiBlogHub features both user-submitted and editorial content. We do not verify third-party contributions. Read our Disclaimer and Privacy Policyfor details.