Exploring Closed Cell Crosslinked Foams: Advancements in Aerospace Applications
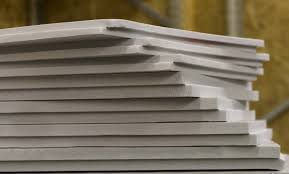
Introduction:
Closed cell crosslinked foams have become a crucial material in modern aerospace applications, providing several performance benefits that make them ideal for use in aircraft components. The aerospace industry, which is constantly seeking ways to reduce weight, enhance durability, and improve efficiency, has embraced these innovative materials. This article explores how closed cell crosslinked foams have advanced in aerospace, particularly focusing on their role in lightweight aircraft components, their properties, and the future of their use in aviation.
Understanding Closed Cell Crosslinked Foams
Closed cell crosslinked foams are a type of foam material characterized by small, sealed cells that are uniformly distributed throughout the foam structure. These cells are typically filled with gas, which makes the foam lightweight yet durable. The “closed cell” nature of the foam means that each cell is isolated, preventing air and moisture from entering, making it an excellent barrier against thermal and acoustic energy. The "crosslinked" aspect refers to the chemical bonds formed between the polymer chains in the foam structure, which significantly enhance the foam's mechanical properties, such as strength, stability, and resistance to environmental stress.
The foam’s ability to be tailored for different performance characteristics is key to its applications. Closed cell crosslinked foams can be designed to meet specific weight, insulation, and strength requirements, making them ideal for use in the aerospace industry, where precision and performance are essential.
Advancements in Closed Cell Crosslinked Foams for Lightweight Aircraft Components
Reducing the weight of aircraft components has been one of the aerospace industry's top priorities. Lighter aircraft are more fuel-efficient, which reduces operational costs and lowers environmental impact. Closed cell crosslinked foams have made significant contributions to this objective by replacing heavier, traditional materials with lightweight foam solutions. These foams are used in a variety of aircraft components, from structural parts to insulation materials, thanks to their unique combination of lightweight and strong properties.
High Strength-to-Weight Ratio
One of the most important properties of closed cell crosslinked foams is their excellent strength-to-weight ratio. This means that the foam can provide the necessary mechanical strength while remaining significantly lighter than many other materials, such as metals or conventional foams. The increased strength is a result of the crosslinked polymer structure, which improves the foam's resistance to deformation, cracking, and environmental stresses. As a result, these foams can be used in components that must endure high mechanical loads and vibrations, such as wing structures, fuselage components, and load-bearing parts.
Because weight is a critical factor in aircraft performance, closed cell crosslinked foams are increasingly used in areas where weight reduction is paramount, such as in the construction of aircraft wings, interior panels, and other key structural elements.
Improved Durability and Impact Resistance
Another advantage of closed cell crosslinked foams in aerospace is their enhanced durability. The foam’s closed-cell structure helps prevent moisture absorption and ensures that the material retains its mechanical properties even in extreme weather conditions. This is especially important in aerospace applications, where components must be able to withstand harsh environmental conditions such as fluctuating temperatures, humidity, and corrosive atmospheres.
Additionally, the crosslinked structure of the foam makes it more resistant to impact and wear. This is particularly important for components that are exposed to constant stress, including those used in high-speed aircraft. The foam's durability ensures that it maintains its integrity over time, reducing the need for maintenance or replacement, which in turn leads to longer service life and lower operational costs for airlines.
Thermal and Acoustic Insulation
Closed cell crosslinked foams also play a critical role in improving the thermal and acoustic insulation properties of aircraft. Their closed-cell structure provides an effective barrier against heat transfer and sound waves. This makes them ideal for applications where temperature regulation and noise reduction are crucial, such as in the insulation of cabins and engines.
In the aerospace industry, maintaining the right internal temperature and minimizing noise pollution are essential for both passenger comfort and operational efficiency. The lightweight and insulating properties of closed cell crosslinked foams help meet these requirements without adding unnecessary weight to the aircraft. As a result, aircraft manufacturers are increasingly adopting these foams for insulation in both the interior and exterior of the aircraft, where they contribute to both energy savings and passenger experience.
Applications of Closed Cell Crosslinked Foams in Aerospace
Closed cell crosslinked foams are being utilized in a variety of aerospace applications, contributing to performance improvements and cost savings. Here are some of the key areas where these foams are being integrated:
1. Aircraft Interiors
The interiors of modern aircraft require materials that are not only lightweight but also durable and safe. Closed cell crosslinked foams are used extensively in seating, cabin insulation, and overhead compartments. These foams offer a high level of comfort due to their cushioning properties while simultaneously providing noise and thermal insulation, which enhances the overall passenger experience.
In addition, the fire-resistant properties of many closed cell crosslinked foams ensure compliance with strict safety standards for aviation materials. They can be incorporated into seat cushions, sidewall panels, and flooring, offering an ideal balance between safety, comfort, and weight reduction.
2. Structural Components
Closed cell crosslinked foams are being increasingly used in structural components such as wing spars, fuselage skins, and floor panels. These materials provide the necessary structural integrity without the excessive weight typically associated with metal parts. The combination of strength, lightness, and resistance to environmental factors such as moisture and corrosion makes closed cell foams an ideal choice for replacing or complementing traditional materials like aluminum.
For example, closed cell foams are often used in composite materials, where they serve as a core material between layers of carbon fiber or fiberglass. This type of composite structure, often referred to as sandwich construction, offers excellent strength while maintaining a low weight. The foams’ ability to withstand significant forces while being light enough to reduce the overall mass of the aircraft makes them indispensable in the construction of modern aircraft.
3. Thermal Insulation in Engine Components
The aerospace industry requires advanced materials that can withstand extreme temperatures. Closed cell crosslinked foams are now being used in thermal insulation applications for engine components, such as heat shields, insulation blankets, and combustion chamber linings. These foams provide a lightweight solution for managing heat while protecting sensitive components from damage caused by high temperatures.
By incorporating closed cell crosslinked foams in these components, manufacturers can ensure that engines operate at optimal temperatures, improving efficiency and preventing overheating. This enhances the overall performance of the aircraft and extends the lifespan of engine components.
4. Fuel Tanks and Pressure Vessels
Closed cell foams are also used in the aerospace industry to line fuel tanks and pressure vessels. These foams act as a protective layer that helps prevent leaks and adds an extra layer of structural integrity. Their resistance to both thermal and mechanical stresses ensures that fuel tanks remain safe and secure during long flights.
In addition to protecting the structural components of the aircraft, these foams also help reduce the weight of the aircraft’s fuel system, contributing to overall weight reduction and improved fuel efficiency.
The Future of Closed Cell Crosslinked Foams in Aerospace
As the aerospace industry continues to innovate and seek more efficient, lightweight, and sustainable materials, the role of closed cell crosslinked foams will only continue to grow. Research and development efforts are focused on improving the foam’s performance by making it even lighter, stronger, and more adaptable to diverse aerospace applications.
Future advancements may include foams that offer even better thermal and acoustic insulation, enhanced fire resistance, and improved environmental sustainability. For instance, efforts are being made to create bio-based foams that reduce dependence on petroleum-based materials, aligning with the increasing demand for sustainable manufacturing processes.
Additionally, as the push for electric and hybrid-electric aircraft grows, the need for lightweight materials will become even more pressing. Closed cell crosslinked foams, with their excellent strength-to-weight ratio, will continue to be an essential material in the development of next-generation aircraft, contributing to both performance and sustainability.
Conclusion
Closed cell crosslinked foams have become an integral part of the aerospace industry, enabling the development of lighter, more efficient aircraft components. These foams provide the ideal combination of strength, durability, and low weight, which is critical in the aerospace industry, where performance and fuel efficiency are paramount.
From aircraft interiors to structural components and engine insulation, closed cell foams are playing a crucial role in advancing aerospace technologies. As the industry moves toward more sustainable and energy-efficient solutions, these materials will continue to evolve, contributing to the creation of next-generation aircraft that are safer, more efficient, and environmentally friendly.
Read the complete blog: https://www.nextmsc.com/blogs/aerospace-foam-market-trends
Note: IndiBlogHub features both user-submitted and editorial content. We do not verify third-party contributions. Read our Disclaimer and Privacy Policyfor details.