Global Market for 3D Printed Prosthetics Poised for Rapid Expansion
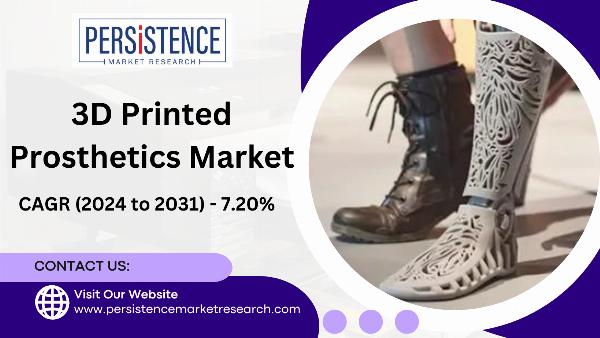
The global 3D printed prosthetics market is set to grow from US$1.69 billion in 2024 to US$2.77 billion by 2031, at a CAGR of 7.20%. This market revolutionizes medical technology by using additive manufacturing to create customized prosthetic limbs. 3D printed prosthetics enhance comfort and mobility, offering a better fit and functionality than traditional prosthetics. This technology democratizes access to advanced limb replacements by reducing costs and streamlining production, making them affordable and accessible, especially in underserved communities. The market's growth is driven by continuous innovations in design and functionality, promising improved efficacy and aesthetics in prosthetic solutions.
Factors Driving Market Growth
Technological Advancements
3D printing technology has evolved dramatically over the past decade, enabling the production of highly customized and complex prosthetic devices. Innovations in material science, printing techniques, and the integration of electronic components have significantly enhanced the functionality and accessibility of 3D printed prosthetics.
Material Science Innovations: Advances in materials such as thermoplastics, metals, and biocompatible polymers have provided the necessary strength, flexibility, and biocompatibility for effective prosthetic devices. High-performance thermoplastics like nylon and polycarbonate offer superior strength and flexibility, while metals like titanium provide exceptional durability.
Printing Techniques: The development of more precise and efficient printing techniques has reduced production times and costs. Multi-material printing capabilities allow for the creation of prosthetics with varying properties in different regions, enhancing their overall performance.
Integration of Electronics: The ability to integrate sensors and electronic components into 3D printed prosthetics has led to the development of smart prosthetics. These devices offer real-time feedback and improved control, significantly enhancing the user experience.
Increasing Demand for Personalized Prosthetics
The demand for personalized prosthetics is growing as patients seek devices tailored to their unique anatomical needs. Traditional manufacturing methods often fall short in providing the necessary customization, leading to discomfort and reduced functionality. 3D printing technology, however, allows for the creation of prosthetics that fit perfectly, improving comfort and usability.
Customization: 3D printing enables the production of prosthetics designed specifically for an individual's anatomy, enhancing the fit and comfort. This high level of customization is particularly beneficial for children, who require frequent adjustments to their prosthetics as they grow.
Rapid Prototyping: The ability to quickly produce prototypes allows for iterative design improvements, ensuring the final product meets the highest standards of performance and comfort.
Rising Incidence of Limb Loss
Globally, the incidence of limb loss due to accidents, diabetes, vascular diseases, and cancer is increasing. According to the Amputee Coalition, approximately 185,000 amputations occur annually in the United States alone. This growing need for effective prosthetic solutions is a significant driver for the 3D printed prosthetics market.
Advantages of 3D Printed Prosthetics
Cost-Effectiveness
3D printing technology offers a cost-effective alternative to traditional prosthetic manufacturing methods. The ability to produce prosthetics on-demand reduces inventory costs and waste. Additionally, the use of advanced plastics and other materials in 3D printing is generally less expensive than metals and specialized materials used in traditional manufacturing.
Affordable Materials: Plastics, particularly thermoplastics, are less expensive to produce and process compared to metals. This affordability makes 3D printed prosthetics more accessible to a broader population.
Reduced Production Costs: The ability to produce prosthetics on-demand reduces the need for large inventories and minimizes waste, further lowering costs.
Enhanced Design Flexibility
3D printing technology enables the creation of complex geometries that are difficult or impossible to achieve with traditional manufacturing methods. This design flexibility allows for innovative prosthetic designs that improve functionality and aesthetics.
Complex Geometries: 3D printing allows for the production of prosthetics with intricate designs and internal structures, enhancing their performance and durability.
Aesthetic Customization: Patients can choose from a variety of colors, textures, and finishes, allowing for greater personalization and satisfaction.
Rapid Prototyping and Production
The use of 3D printing in prosthetic production significantly reduces development and delivery times. This speed is particularly beneficial for developing custom prosthetics tailored to individual patients and for quick replacement of damaged or worn-out devices.
Faster Development: Rapid prototyping allows for the quick production of prototypes, enabling iterative design improvements and faster development cycles.
Quick Replacement: The ability to quickly produce custom prosthetics ensures patients can receive replacements without long wait times, improving their overall experience.
Challenges and Opportunities
Despite the promising growth, the 3D printed prosthetics market faces several challenges that need to be addressed:
Regulatory and Quality Control Issues
Ensuring the safety and efficacy of 3D printed prosthetics is crucial. Regulatory bodies such as the FDA are working to establish guidelines and standards for the production of medical devices using 3D printing technology. Compliance with these regulations can be costly and time-consuming, but it is essential for ensuring patient safety.
Regulatory Compliance: Manufacturers must adhere to strict guidelines and standards to ensure the safety and efficacy of their products, which can be a significant challenge.
Quality Control: Ensuring consistent quality in 3D printed prosthetics is essential, requiring rigorous testing and validation processes.
Cost Management
While 3D printing technology offers cost advantages, managing the costs associated with high-quality, specialized materials can be challenging. Efforts to develop more affordable yet equally effective materials are essential to reducing the overall cost of 3D printed prosthetics.
Material Costs: Advanced materials used in 3D printed prosthetics can be expensive, necessitating ongoing research to find cost-effective alternatives.
Production Costs: Managing production costs, particularly for custom and complex designs, is essential for maintaining affordability.
Future Outlook and Market Projections
The future of the 3D printed prosthetics market is promising, with several trends expected to shape its growth:
Expansion into Developing Markets
As 3D printing technology becomes more affordable and accessible, there is significant potential for expanding 3D printed prosthetics into developing markets. These regions often face challenges in accessing high-quality prosthetic care, and 3D printing could provide a viable solution.
Affordability: As costs continue to decrease, 3D printed prosthetics will become more accessible to patients in developing markets.
Accessibility: 3D printing technology can be deployed locally, reducing the need for expensive and time-consuming shipping from centralized manufacturing facilities.
Continued Technological Advancements
Ongoing research and development in 3D printing technology will likely lead to further innovations in prosthetic design and production. Advances in materials science, printing techniques, and integration of electronic components will continue to enhance the functionality and affordability of 3D printed prosthetics.
New Materials: The development of new materials with improved performance and lower costs will drive further growth in the market.
Technological Innovations: Continued advancements in 3D printing technology will enable the production of more complex and functional prosthetics.
Collaborations and Partnerships
Collaborations between medical device manufacturers, research institutions, and healthcare providers will play a crucial role in advancing the 3D printed prosthetics market. Partnerships can facilitate knowledge sharing, resource pooling, and expertise, driving innovation and improving patient outcomes.
Knowledge Sharing: Collaborative efforts will enable the sharing of best practices and advancements in technology and materials.
Resource Pooling: Partnerships can leverage collective resources to accelerate research and development efforts.
Conclusion
The global market for 3D printed prosthetics is poised for rapid expansion, driven by advancements in technology, increasing demand for personalized prosthetics, and the rising incidence of limb loss. Plastics and other advanced materials play a crucial role in this transformation, providing the necessary properties for high-quality, durable, and functional prosthetics. Addressing challenges related to regulation, cost management, and quality control will be essential to fully realizing the potential of 3D printed prosthetics. With continued advancements and collaborations, the future of 3D printed prosthetics looks promising, poised to revolutionize the industry and improve the lives of countless individuals worldwide.
Note: IndiBlogHub features both user-submitted and editorial content. We do not verify third-party contributions. Read our Disclaimer and Privacy Policyfor details.