How to Choose the Right Brass Moulding Insert for Your Application
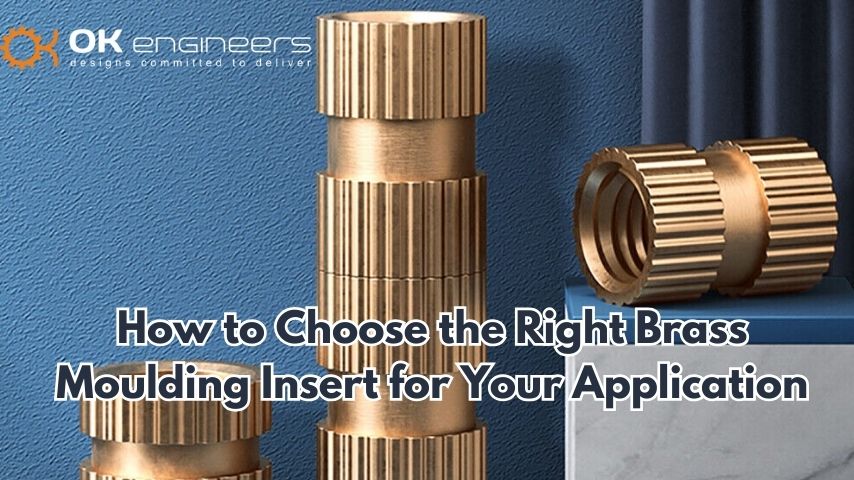
Brass Moulding Insert are essential components across various industries due to their durability, corrosion resistance, and versatility. Choosing the right brass moulding insert requires a careful assessment of the specific needs of your application to ensure reliable performance and longevity. In this comprehensive guide, we delve into the factors you must consider to make the best choice for your brass moulding insert.
Understanding the Benefits of Brass Moulding Insert
Brass is widely used for moulding inserts because it combines strength, malleability, and resistance to corrosion. When selecting a brass moulding insert, it's crucial to understand why brass is the preferred material. The main benefits include:
Corrosion Resistance: Brass is highly resistant to rust and corrosion, making it ideal for applications in humid or high-moisture environments.
High Durability: Brass provides strength while maintaining its structural integrity under pressure, which is essential for load-bearing or high-stress applications.
Electrical Conductivity: For applications requiring conductivity, such as electrical and electronic components, brass is highly suitable due to its excellent conductivity properties.
Ease of Machining: Brass is relatively easy to shape and customize, which allows manufacturers to produce highly specific, detailed designs to meet unique needs.
Types of Brass Moulding Insert
Different applications demand different types of brass moulding insert. Understanding these types helps narrow down the selection for your specific application:
Threaded Inserts: These inserts are ideal for applications that require secure and reliable threading, such as automotive parts and mechanical components.
Knurled Inserts: Knurled inserts are often used in plastic components where a tight grip is needed, making them perfect for appliances and electronics.
Ultrasonic Inserts: Designed for ultrasonic installation, these inserts work well in thermoplastics, where they bond without the need for adhesives or additional tools.
Heat Staked Inserts: Best suited for applications where heat staking is feasible, these inserts fuse with the plastic as they cool, creating a solid and durable connection.
Choosing the Right Brass Alloy
Not all brass is the same, and different alloys offer unique benefits. The choice of alloy impacts the insert’s strength, malleability, and corrosion resistance. Here are a few common alloys used in brass moulding insert:
CZ121 Brass (Free-Machining Brass): Known for its ease of machining, this alloy is widely used for threaded inserts and other detailed applications.
CZ131 Brass: With high resistance to dezincification, this alloy is suitable for marine applications or environments exposed to water and humidity.
CW602N Brass (DZR Brass): This alloy resists dezincification, making it ideal for plumbing and fittings where water exposure is common.
Key Factors to Consider When Selecting Brass Moulding Insert
Choosing the right brass moulding insert involves evaluating several key factors. Here’s a breakdown of what you should consider:
1. Application Requirements
Each application has unique requirements that will dictate the type, size, and characteristics of the brass insert. For example, electronics may require threaded inserts for secure, conductive connections, while plastic moulding applications may benefit from knurled or ultrasonic inserts to improve adhesion.
Load Bearing Capacity
For load-bearing applications, the insert must be able to withstand the stress without deforming or failing. Threaded brass inserts are particularly suitable for applications with high stress requirements due to their robustness.
Operating Environment
Consider the environmental conditions, such as temperature and humidity, that the insert will be exposed to. High-humidity environments or marine applications may require a brass alloy with greater corrosion resistance.
2. Insert Design and Size
The insert’s design and size directly impact its compatibility with the surrounding material. Choose an insert size that provides a secure fit without risking cracks or deformities in the host material.
Insert Length and Diameter
The length and diameter of the insert play a critical role in securing the insert within the material. An insert with a larger diameter and greater length will generally have a higher holding strength, but may require a larger host material.
Type of External Surface
The external surface of the insert can be smooth, knurled, or threaded. Knurled surfaces provide greater friction and grip within plastic applications, reducing the chances of the insert slipping or rotating.
3. Installation Method
Different inserts require different installation methods, which can impact assembly time, cost, and insert durability. Common installation methods include ultrasonic insertion, heat staking, and press-fitting.
Ultrasonic Insertion
In this method, ultrasonic vibrations generate heat that melts the surrounding material, allowing the insert to fuse in place. It’s suitable for plastic moulding applications requiring high precision.
Heat Staking
Heat staking uses controlled heat to soften the material around the insert, which is then pushed into place. As the material cools, it hardens and forms a secure bond with the insert.
Press Fitting
A press fit involves pressing the insert into a pre-drilled hole, relying on friction to hold it in place. This is ideal for applications where ease of installation is a priority.
4. Compatibility with the Host Material
Consider the properties of the material where the insert will be installed. For example, softer materials like thermoplastics may benefit from inserts with knurled surfaces, which provide added grip and prevent rotation. Metal applications may require inserts with threaded exteriors for secure fitting.
5. Electrical and Thermal Conductivity Needs
If the application involves electricity or heat, select a brass alloy that offers the required conductivity. Brass is a good conductor, but specific alloys and insert designs optimize conductivity for different applications.
Installation Tips for Brass Moulding Insert
Installing brass moulding insert correctly is crucial for maximizing performance and longevity. Here are a few tips to ensure a successful installation:
Pre-drill Properly: Make sure the hole is drilled to the right size to avoid a loose fit or causing stress on the surrounding material.
Use Controlled Heat: For heat-staked inserts, use controlled temperatures to prevent damage to the material and ensure the insert seats firmly.
Apply Steady Pressure: When press fitting, ensure even, steady pressure to prevent misalignment or deformation.
Benefits of Choosing the Right Brass Moulding Insert
Choosing the right brass insert delivers several advantages:
Enhanced Durability: Properly selected and installed brass inserts withstand wear and tear, reducing the need for maintenance.
Increased Performance: Inserts tailored to the specific application ensure reliable, long-lasting performance.
Cost-Efficiency: Using the correct insert for the job reduces replacement costs and downtime associated with component failure.
Improved Aesthetics and Functionality: A suitable brass moulding insert maintains both the look and functionality of the application, especially in high-visibility settings.
Applications of Brass Moulding Insert
Brass moulding insert find applications across diverse industries, including:
Automotive Industry: Brass inserts are commonly used in automotive parts due to their strength and durability.
Electronics: In electronics, brass’s conductivity and corrosion resistance make it ideal for threaded inserts and connectors.
Aerospace and Marine: High corrosion resistance alloys like DZR brass are used in aerospace and marine applications where durability in harsh conditions is essential.
Home Appliances: Brass inserts provide durable and reliable connections in household appliances, ensuring components remain securely fastened over time.
Conclusion
Choosing the right brass moulding insert requires an understanding of the specific demands of your application. By evaluating the material requirements, insert type, and environmental factors, you can ensure a choice that will deliver reliable performance and durability. Whether you need high conductivity for electronics or corrosion resistance for marine applications, the correct brass insert can make a significant difference in both functionality and longevity.
Note: IndiBlogHub features both user-submitted and editorial content. We do not verify third-party contributions. Read our Disclaimer and Privacy Policyfor details.