Behind the Scenes: The Craftsmanship of Brass Reducers Manufacturers
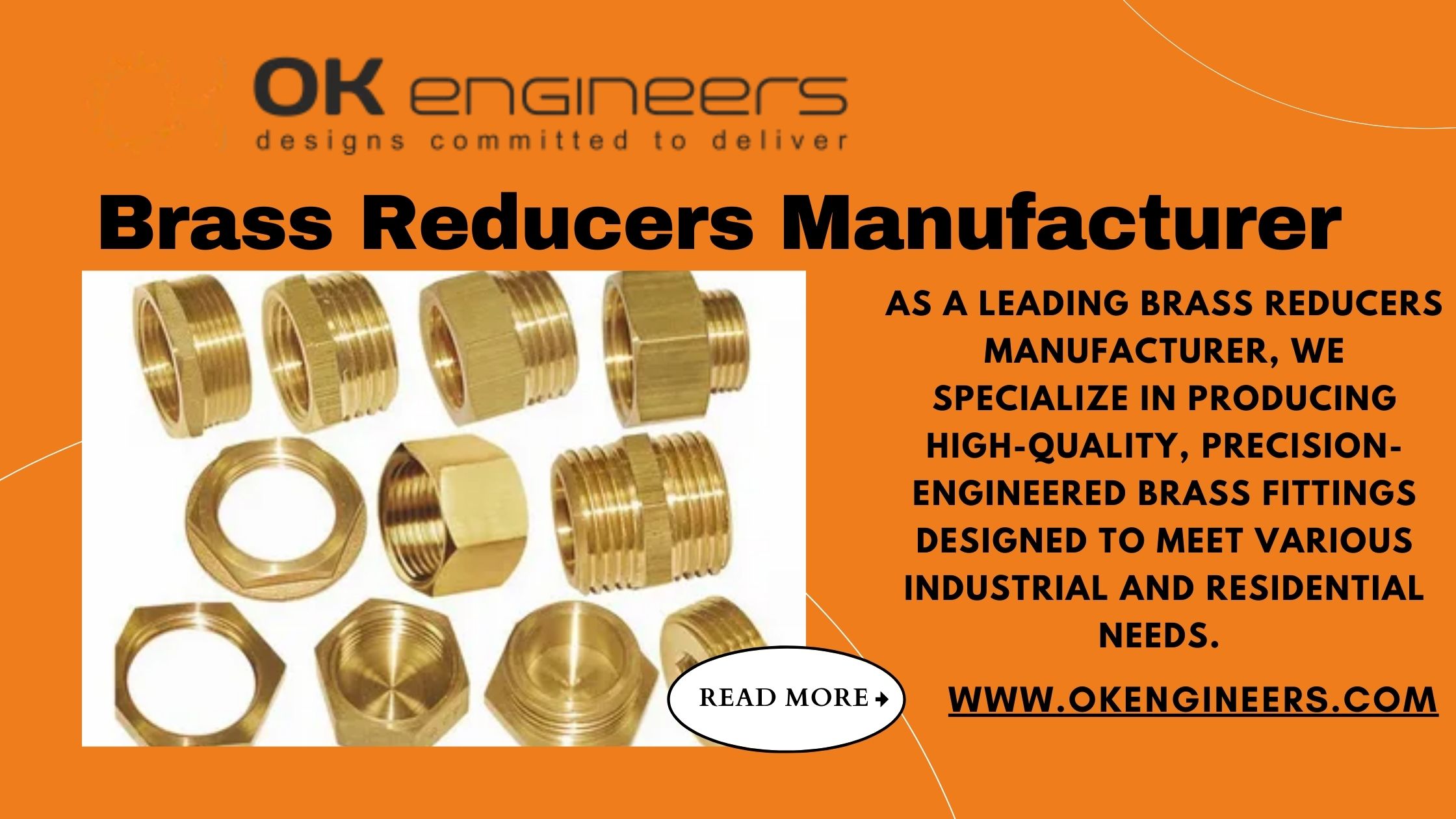
When it comes to plumbing, heating, and other applications requiring fluid dynamics, brass reducers are essential components that ensure the efficient flow of liquids and gases. These fittings, designed to transition between different pipe diameters, play a critical role in maintaining pressure and preventing leaks. However, behind the seemingly simple function of brass reducers lies a complex world of craftsmanship and engineering. In this blog, we will delve into the craftsmanship of brass reducers manufacturers, exploring their processes, materials, and the artistry involved in creating these vital components.
Understanding Brass Reducers
Before we dive into the craftsmanship, it's important to understand what brass reducers are and their purpose. Brass reducers are fittings made from brass, a durable alloy primarily composed of copper and zinc. Their primary function is to connect two pipes or tubes of different diameters, allowing for a smooth transition that minimizes turbulence and pressure loss.
Brass reducers come in various forms, including concentric and eccentric designs. Concentric reducers maintain the same axis, while eccentric reducers offset the center line, making them ideal for horizontal applications. Their versatility and reliability make them a staple in numerous industries, from plumbing and HVAC to manufacturing and automotive.
The Role of Brass Reducers Manufacturers
Brass reducers manufacturers are the unsung heroes behind the scenes, responsible for transforming raw materials into expertly crafted fittings. Their role encompasses several stages, each requiring precision, skill, and an understanding of metallurgy and fluid dynamics.
1. Material Selection
The journey of crafting brass reducers begins with the careful selection of materials. Brass is favored for its excellent corrosion resistance, malleability, and durability. Manufacturers must choose the right grade of brass to suit specific applications, balancing factors such as cost, mechanical properties, and environmental conditions.
In addition to brass, manufacturers may also consider other materials like bronze or stainless steel for specific applications, but brass remains the most popular choice due to its advantageous properties.
2. Design and Engineering
Once the materials are selected, the design process begins. This stage involves creating detailed drawings and specifications that outline the dimensions, tolerances, and overall functionality of the brass reducers. Advanced computer-aided design (CAD) software allows manufacturers to simulate the performance of the fittings under various conditions.
Designing brass reducers requires a deep understanding of fluid dynamics. Engineers must consider factors like flow rates, pressure drops, and potential turbulence to ensure that the final product meets industry standards and customer requirements.
3. Machining and Fabrication
After the design is finalized, the manufacturing process moves into machining and fabrication. This is where raw brass materials are transformed into precisely shaped fittings. Manufacturers employ various machining techniques, including:
Turning: This process involves rotating the brass material against a cutting tool to create the desired shape and dimensions.
Milling: Milling machines remove material from the brass stock to create intricate features, such as threads or grooves.
Drilling: Drill bits are used to create holes for connections, ensuring a perfect fit with other pipes or components.
Stamping and Forging: In some cases, manufacturers may use stamping or forging methods to create brass reducers in bulk, enhancing production efficiency.
Quality control is essential during this phase. Manufacturers regularly inspect the fittings for dimensional accuracy and surface finish, ensuring they meet rigorous quality standards.
4. Surface Treatment
Once the brass reducers are machined, they undergo surface treatment to enhance their appearance and protect against corrosion. Various methods can be employed, including:
Electroplating: A layer of metal, such as nickel or chrome, is deposited onto the brass surface to enhance its corrosion resistance and aesthetic appeal.
Polishing: A polishing process improves the surface finish, giving the fittings a shiny, attractive appearance.
Coating: Some manufacturers apply protective coatings to further enhance corrosion resistance, particularly for reducers used in harsh environments.
5. Assembly and Quality Assurance
In many cases, brass reducers are part of a larger assembly that includes other fittings and components. Manufacturers ensure that all parts fit together seamlessly by assembling the fittings with precision and care.
Quality assurance is a critical aspect of this process. Each batch of brass reducers is rigorously tested to ensure it meets industry standards. This may include pressure testing, leak testing, and performance testing under various conditions.
6. Packaging and Distribution
Once the brass reducers have passed quality assurance checks, they are carefully packaged for distribution. Manufacturers prioritize protecting the fittings from damage during transportation, using materials that safeguard against scratches, dents, and corrosion.
Efficient distribution channels are also vital. Manufacturers must coordinate with suppliers and logistics partners to ensure timely delivery to customers across various industries. This aspect of craftsmanship requires not only skill but also strong organizational and communication abilities.
The Art of Craftsmanship in Brass Reducers Manufacturing
While the processes outlined above may seem technical, there is an undeniable artistry involved in brass reducers manufacturing. Skilled craftsmen take pride in their work, paying attention to every detail to create fittings that are not only functional but also aesthetically pleasing.
1. Tradition Meets Technology
Many brass reducers manufacturers have honed their skills over generations, combining traditional craftsmanship with modern technology. Experienced artisans bring invaluable knowledge to the table, ensuring that the quality of the fittings remains high, even as manufacturing techniques evolve.
2. Customization and Innovation
The demand for customized solutions is ever-growing in today's market. Manufacturers often collaborate with clients to create bespoke brass reducers tailored to specific needs. This level of customization requires creativity and innovation, as manufacturers must adapt their processes to accommodate unique designs and requirements.
3. Sustainability Practices
With increasing awareness of environmental issues, many brass reducers manufacturers are adopting sustainable practices. This includes sourcing materials responsibly, reducing waste during production, and implementing eco-friendly packaging solutions. By focusing on sustainability, manufacturers can contribute positively to the environment while maintaining their commitment to quality craftsmanship.
Conclusion
The craftsmanship of brass reducers manufacturers is a fascinating blend of artistry, engineering, and precision. From material selection and design to machining and quality assurance, every step in the manufacturing process contributes to the creation of these vital components.
As industries continue to evolve and demand higher quality products, brass reducers manufacturers are well-positioned to meet these challenges head-on. Their commitment to quality, innovation, and sustainability ensures that brass reducers will continue to play a crucial role in fluid dynamics for years to come.
If you are looking for high-quality brass reducers, look no further than Brass Reducers Manufacturer. Our dedication to craftsmanship and excellence makes us a leading manufacturer in the industry. Let us help you find the right solutions for your projects, ensuring efficiency and reliability every step of the way.
Note: IndiBlogHub features both user-submitted and editorial content. We do not verify third-party contributions. Read our Disclaimer and Privacy Policyfor details.