Industrial Hose: The Unsung Hero Powering Modern Industry
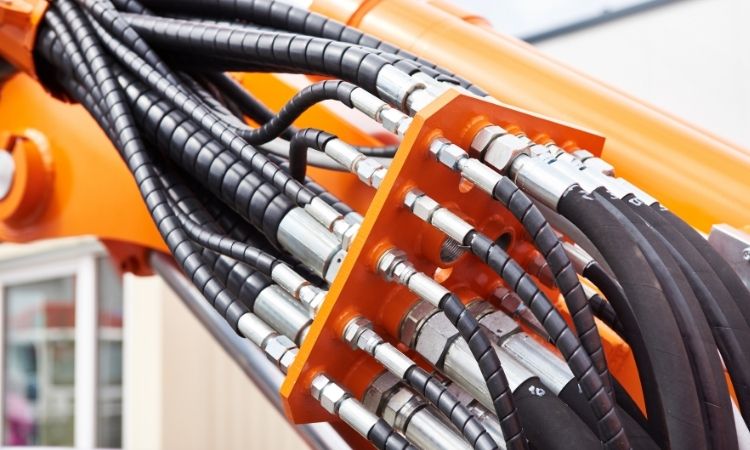
In the world of industrial operations, power tools, heavy machinery, and towering infrastructure often steal the spotlight. Yet, behind the scenes, one flexible yet powerful component keeps systems running smoothly: the industrial hose. This often-overlooked marvel plays a vital role across a range of sectors—from mining and oil refining to agriculture, chemical plants, food processing, and beyond. Its durability, flexibility, and ability to handle extreme conditions make it a core component in the flow of materials, liquids, gases, and even energy.
Expert Market Research: A Strategic Perspective
As industries evolve toward automation, sustainability, and higher safety standards, the demand for high-performance hose systems is accelerating. According to Expert Market Research, advancements in materials technology and smart manufacturing are driving innovations in hose design and durability. Their insights reveal a growing shift towards custom solutions—hoses that can be tailored to exact performance parameters in high-risk applications, helping reduce energy consumption, lower operational costs, and improve overall system integrity.
This strategic intelligence allows businesses to make informed decisions when upgrading systems or choosing suppliers, ensuring long-term resilience and compliance with evolving industry regulations.
Not Just a Pipe: Understanding the Industrial Hose
To the untrained eye, an industrial hose may resemble a thick, rubber tube. But in truth, it’s a highly engineered product crafted to endure hostile environments, corrosive substances, and high-pressure operations. These hoses are specifically designed to carry a wide range of media, including air, water, petroleum, chemicals, steam, and dry materials—each with its own requirements in terms of temperature, pressure rating, and chemical compatibility.
Unlike rigid pipes, industrial hoses offer flexibility in confined spaces and moving machinery. Their design allows them to bend, stretch, and twist, all while maintaining a reliable seal. This adaptability is what makes them indispensable in dynamic environments where movement and vibration are constants.
How Industrial Hoses Keep the World Moving
From massive construction sites to the delicate sterilization processes in pharmaceutical facilities, industrial hoses act as lifelines, transferring essential materials precisely where they're needed. In agriculture, they irrigate crops and spray fertilizers. In oil and gas, they transport fuel, crude oil, and chemicals safely. In firefighting, they channel life-saving water under immense pressure.
Moreover, these hoses are not one-size-fits-all. They come in a variety of materials—rubber, PVC, silicone, and metal-reinforced types—each crafted for specific applications. Some are heat-resistant; others resist freezing. Some stand up to abrasive materials, while others ensure hygiene in food-grade environments. It's this remarkable versatility that makes industrial hoses an irreplaceable tool in practically every sector.
Built for Extremes: The Strength Behind the Flexibility
What makes an industrial hose truly remarkable is its ability to perform in extreme conditions. Think high-pressure steam lines, super-cooled cryogenic environments, or transporting acids in chemical plants. These hoses are reinforced with braids of high-tensile fibers or steel wire, adding strength without sacrificing flexibility.
In many industries, even a minor hose failure can lead to disastrous outcomes—production halts, safety hazards, and expensive downtime. That’s why modern industrial hoses are rigorously tested for burst pressure, tensile strength, fatigue, and chemical resistance. Safety, durability, and longevity are no longer optional—they’re the foundation.
Precision Matters: The Role of Hose Assemblies
It’s not just about the hose itself. The connectors, fittings, clamps, and couplings—collectively known as hose assemblies—are engineered with the same precision. These components ensure secure, leak-free connections in high-stress environments. A poorly fitted hose is not only inefficient but dangerous, especially when dealing with hazardous fluids or pressurized systems.
Regular maintenance and correct installation are crucial. Many facilities employ technicians specifically trained in hose inspection, replacement, and failure analysis to maintain peak system performance and workplace safety.
Innovation in Industrial Hose Design
Today’s industrial hoses are not the same as those used a decade ago. Material innovation has made them lighter, stronger, and more resistant to a broader range of substances. Thermoplastic hoses, for instance, offer enhanced flexibility and temperature resistance, while hybrid designs combine the best properties of rubber and plastic for unmatched performance.
There are even smart hoses equipped with sensors to monitor wear, pressure, and flow rate in real-time, helping operators prevent failures before they occur. This fusion of mechanical engineering and digital technology is paving the way for predictive maintenance, reducing downtime and boosting efficiency across the board.
The Silent Force Driving Progress
While they may not be as flashy as giant machines or high-tech robots, industrial hoses are the silent force powering nearly every modern operation. They ensure that materials flow seamlessly from point A to point B—safely, efficiently, and reliably. As industries demand more from their equipment, the importance of high-quality hose systems continues to grow.
Note: IndiBlogHub features both user-submitted and editorial content. We do not verify third-party contributions. Read our Disclaimer and Privacy Policyfor details.