Maintenance Best Practices for Water-Cooled and Air-Cooled Screw Chillers
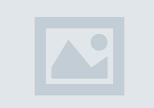
In the realm of industrial and commercial cooling, the impact of proper maintenance cannot be overstated.
Consider this: a well-maintained screw chiller can achieve full-load efficiency ratings of approximately 0.55-0.60 kW per ton, while poorly maintained units may see efficiency drop to 0.90-1.0 kW per ton, leading to increased operational costs by 20-25% annually for the same cooling output. This stark contrast underscores the critical importance of implementing robust maintenance practices for both water-cooled screw chillers and air-cooled screw chillers.
At Climaveneta, we recognize that optimal chiller performance is not just about preventing breakdowns; it's about maximizing efficiency, reducing energy consumption, and extending equipment lifespan. This article delves into the best practices for maintaining these screw chillers, offering insights valuable for facility managers, technicians, and decision-makers across the globe.
The Importance of Maintenance in Screw Chillers
Beyond the efficiency gains mentioned above, regular maintenance plays a pivotal role in several key areas:
Energy Conservation: Industry studies show that approximately 95% of chillers waste between 5-30% of electricity due to avoidable inefficiencies stemming from poor maintenance practices.
Cost Savings: Implementing a structured maintenance program can reduce annual energy costs by up to 25%, translating to significant financial benefits over time.
Equipment Longevity: Proper upkeep can extend the lifespan of chillers, often exceeding 15 years with appropriate care.
Reliability: A well-maintained screw chiller minimizes the risk of unexpected breakdowns, ensuring continuous operation in critical environments.
Common Best Practices for Both Types of Chillers
While water-cooled screw chillers and air-cooled screw chillers have their unique maintenance needs, several practices benefit both:
Regular Inspections
Conduct routine checks of all components, including compressors, evaporators, and condenser units. This proactive approach helps identify potential issues before they escalate.
Refrigerant Level Monitoring
Regularly check refrigerant levels to prevent inefficiencies caused by low levels or leaks. Implement leak detection systems for early issue identification.
Lubrication
Ensure all moving parts are adequately lubricated according to manufacturer specifications. Regularly check oil levels in compressors and replace filters as needed.
Electrical System Checks
Inspect electrical connections for signs of wear or corrosion. Ensure all electrical components function correctly to prevent operational failures.
Performance Monitoring
Utilize advanced monitoring systems to track performance metrics such as temperature, pressure, and energy consumption. Analyze data trends to identify potential issues and optimize system efficiency.
Record Keeping
Maintain detailed logs of all maintenance activities, inspections, and repairs. This data is invaluable for developing proactive maintenance schedules and identifying long-term performance trends.
Training Personnel
Provide ongoing training for maintenance staff on best practices and troubleshooting techniques. Foster a culture of safety and awareness regarding screw chiller operations.
Specific Practices for Water-Cooled Screw Chillers
Water-cooled screw chillers require unique maintenance due to their use of water as a heat transfer medium:
Water Quality Management: Implement a comprehensive water treatment program to manage pH levels and chemical balance. This prevents scaling and corrosion, which can significantly impact screw chiller’s efficiency and longevity.
Condenser Maintenance: Regularly clean condenser tubes to ensure efficient heat exchange. Inspect for fouling or corrosion that can impede performance.
Water Flow Inspection: Regularly check water inlets and outlets for leaks and blockages. Proper water flow is essential for efficient heat transfer and overall system performance.
Specific Practices for Air-Cooled Screw Chillers
Air-cooled screw chillers rely on ambient air for heat rejection, necessitating specific maintenance practices:
Airflow Management: Ensure that air filters are clean and free from debris; replace them as needed. Keep the area around the chiller clear of obstructions to allow for proper airflow.
Condenser Coil Cleaning: Regularly clean condenser coils to remove dirt and debris that can reduce efficiency. Use appropriate cleaning solutions and techniques to avoid damaging fins.
Fan Maintenance: Inspect fan blades and motors for wear; ensure they are properly lubricated. Check for vibrations or unusual sounds that may indicate mechanical issues.
Belt Tensioning: Monitor belt tension regularly and adjust as necessary to prevent slippage or wear. Replace worn belts promptly to maintain optimal performance.
Implementing a Maintenance Strategy for Screw Chillers
To maximize the benefits of these maintenance practices, implement a comprehensive strategy:
Develop a Maintenance Schedule
Utilize Predictive Maintenance Techniques
Invest in Training
Partner with Experts
Regularly Review and Update Practices
Conclusion
As we circle back to our opening statistic, the importance of proper screw chiller maintenance becomes even more evident. The difference between a well-maintained chiller operating at 0.55-0.60 kW per ton and a poorly maintained one at 0.90-1.0 kW per ton is not just a matter of numbers—it represents significant energy savings, reduced operational costs, and a smaller environmental footprint.
At Climaveneta, we're committed to supporting our clients in achieving these optimal efficiency levels through innovative solutions and expert guidance. By implementing the best practices, facilities can not only avoid the 20-25% increase in annual operational costs associated with poor maintenance but can also extend equipment lifespan, improve reliability, and contribute to overall sustainability goals.
Remember, a well-maintained screw chiller is not just a cost-saving measure; it's an investment in the long-term success and sustainability of your operations. Let the stark efficiency contrast serve as a constant reminder of the value of diligent screw chiller maintenance in your facility's operations.
Note: IndiBlogHub features both user-submitted and editorial content. We do not verify third-party contributions. Read our Disclaimer and Privacy Policyfor details.