Mixing Tanks: Enhancing Efficiency in Chemical Processing
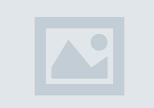
Introduction
In the chemical processing industry, mixing tanks play a crucial role in ensuring product consistency, improving reaction rates, and optimizing resource utilization. Whether used for blending raw materials, dissolving solids, or carrying out chemical reactions, efficient mixing tanks contribute to higher productivity and reduced operational costs. This article explores the importance of mixing tanks in chemical processing, their benefits, types, design considerations, and best practices for maintenance and optimization.
Importance of Mixing Tanks in Chemical Processing
Mixing tanks are fundamental to various chemical processes, including emulsification, dispersion, dissolution, and reaction enhancement. The efficiency of a mixing tank directly impacts product quality, production time, and overall process effectiveness. Inadequate mixing can lead to inconsistent chemical compositions, sedimentation, and even product failure. Therefore, selecting the right mixing tank and ensuring its proper operation is critical for achieving desired results in chemical manufacturing.
Benefits of Using Mixing Tanks
1. Improved Homogeneity
Mixing tanks facilitate uniform distribution of substances, ensuring consistent product quality. Proper agitation and mixing prevent separation, sedimentation, or layering of chemical components.
2. Faster Reaction Times
Effective mixing reduces the time required for chemical reactions by ensuring thorough contact between reactants. This leads to higher production efficiency and lower energy consumption.
3. Energy Efficiency
Modern mixing tank are designed with advanced impellers and mixing mechanisms that optimize energy use while achieving maximum blending efficiency.
4. Scalability
Mixing tanks are available in various sizes, allowing chemical manufacturers to scale up production without compromising quality. Automated control systems further enhance efficiency by adjusting mixing parameters in real time.
5. Enhanced Safety
Properly designed mixing tanks minimize the risk of hazardous reactions, pressure buildup, or leaks, ensuring a safe working environment for chemical plant operators.
Types of Mixing Tanks
Different types of mixing tanks are used in chemical processing, depending on the nature of the substances being mixed and the required process conditions.
1. Stainless Steel Mixing Tanks
These are widely used in the chemical industry due to their corrosion resistance, durability, and ease of cleaning. Stainless steel tanks are suitable for handling reactive chemicals and high-temperature processes.
2. Plastic Mixing Tanks
Made from high-density polyethylene (HDPE) or polypropylene, plastic mixing tanks are ideal for handling corrosive chemicals. They are lightweight, cost-effective, and resistant to certain chemical reactions.
3. Glass-Lined Mixing Tanks
These tanks have a protective glass coating that prevents contamination and corrosion. They are commonly used for highly acidic or alkaline chemical processes.
4. Jacketed Mixing Tanks
These tanks feature an outer layer or jacket that allows for temperature control using heating or cooling fluids. They are ideal for exothermic or endothermic reactions where precise temperature regulation is required.
5. Agitated Mixing Tanks
Equipped with impellers, paddles, or turbines, agitated tanks ensure thorough mixing and prevent sedimentation. The type of agitator used depends on the viscosity and properties of the chemical mixture.
Design Considerations for Efficient Mixing Tanks
To maximize efficiency, mixing tanks must be designed with specific process requirements in mind. Some critical design factors include:
1. Tank Shape and Size
The shape and size of a mixing tank affect fluid flow patterns, energy consumption, and mixing efficiency. Cylindrical tanks with conical bottoms are preferred for optimal mixing and drainage.
2. Impeller Selection
Different types of impellers (e.g., axial, radial, or helical) are chosen based on the viscosity and density of the materials being mixed. Proper impeller design enhances turbulence and mixing efficiency.
3. Baffle Placement
Baffles help prevent vortex formation and improve mixing performance. Strategically placed baffles ensure uniform distribution of mixing energy.
4. Material Compatibility
The tank material must be compatible with the chemicals being processed to prevent corrosion, contamination, or degradation of the tank structure.
5. Automation and Control Systems
Modern mixing tanks are equipped with automated controls for real-time monitoring of mixing speed, temperature, and other process parameters. Automation enhances precision, consistency, and safety.
Best Practices for Maintaining and Optimizing Mixing Tanks
Proper maintenance and optimization of mixing tanks ensure longevity and efficiency. Here are some best practices to follow:
1. Regular Cleaning and Inspection
Frequent cleaning prevents chemical buildup, contamination, and corrosion. Inspection of seals, gaskets, and agitators helps detect early signs of wear and tear.
2. Calibration of Mixing Parameters
Periodic calibration of mixing speed, temperature, and impeller settings ensures that the tank operates at optimal efficiency without excessive energy consumption.
3. Lubrication of Moving Parts
Agitator bearings and other moving components should be lubricated regularly to minimize friction and extend equipment lifespan.
4. Monitoring of Chemical Reactions
Tracking reaction progress and adjusting mixing conditions accordingly prevents unwanted byproducts and enhances process control.
5. Preventive Maintenance Schedules
Implementing a preventive maintenance plan reduces the risk of unexpected breakdowns and production delays. Scheduled maintenance checks help identify potential issues before they escalate.
Conclusion
Mixing tanks are indispensable in chemical processing, providing enhanced efficiency, consistency, and safety. By selecting the right type of mixing tank, optimizing design parameters, and implementing proper maintenance practices, manufacturers can achieve higher productivity and cost savings. As technology advances, automation and improved tank designs will continue to revolutionize chemical processing, making mixing tanks more efficient and reliable than ever before.
Note: IndiBlogHub features both user-submitted and editorial content. We do not verify third-party contributions. Read our Disclaimer and Privacy Policyfor details.