Navigating Complexity: Designing Effective Load Systems in Motion Control
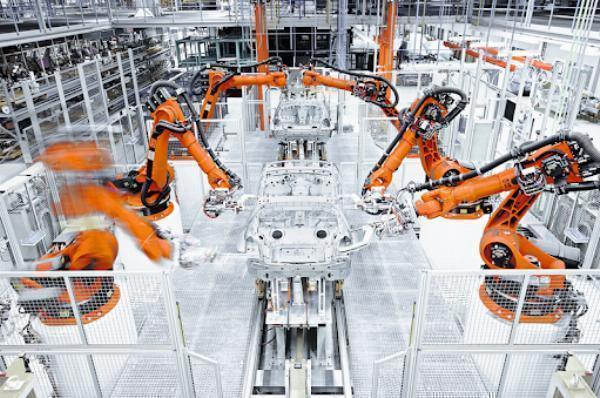
Introduction
In the realm of motion control, designing effective load systems is essential for achieving precise and reliable performance. Load systems, which encompass components such as actuators, bearings, and drive mechanisms, play a critical role in translating motion commands into tangible mechanical output. This article explores the intricacies of load system design, highlighting key considerations, challenges, best practices, and future trends in navigating the complexity of motion control.
Understanding Load Systems
What are Load Systems?
Load systems are mechanical structures or subsystems that support and manipulate loads within motion control applications. They are responsible for transmitting motion, force, and energy between actuators and the load being moved or manipulated.
Types of Load Systems
Load systems come in various configurations depending on the application requirements, such as linear systems for straight-line motion, rotary systems for rotational motion, and multi-axis systems for complex motion trajectories.
Factors Influencing Load System Design
Load Characteristics
Understanding the characteristics of the load, including weight, size, and distribution, is crucial for designing a load system that can effectively support and manipulate the load without compromising performance or safety.
Environmental Conditions
Consideration must be given to the operating environment, including factors such as temperature, humidity, and contamination levels, which can impact the selection of materials, lubricants, and sealing mechanisms for the load system.
Integration with Motion Control Systems
The load system must be seamlessly integrated with the overall motion control architecture, including actuators, sensors, controllers, and feedback mechanisms, to ensure precise and coordinated motion.
Design Considerations for Effective Load Systems
Load Capacity and Dynamics
Selecting components with appropriate load capacity and dynamic performance is essential for ensuring that the load system can handle the required loads and motion profiles without exceeding mechanical limits or compromising accuracy.
Stability and Vibration Damping
Designing the load system to minimize vibrations and instability is critical for maintaining precision and accuracy, especially in high-speed or high-precision applications where even minor disturbances can affect performance.
Precision and Accuracy Requirements
Meeting the precision and accuracy requirements of the application necessitates careful selection of components, such as bearings, gears, and drives, as well as meticulous calibration and tuning of the entire load system.
Challenges in Load System Design
Complex Motion Profiles
Designing load systems capable of executing complex motion profiles, such as curves, arcs, and splines, presents challenges in terms of synchronization, trajectory planning, and dynamic response.
High-Speed Operation
Achieving reliable performance at high speeds requires addressing issues such as inertia, friction, and dynamic response time, which can affect the stability and accuracy of the load system.
Multi-Axis Synchronization
Coordinating motion across multiple axes adds another layer of complexity to load system design, requiring precise synchronization and coordination to ensure smooth and accurate motion.
Best Practices for Load System Design
Proper Selection of Components
Carefully choose components based on performance specifications, reliability, and compatibility with the application requirements to ensure optimal performance and longevity of the load system.
Rigorous Testing and Validation
Thoroughly test and validate the load system under various operating conditions to identify potential issues, optimize performance, and verify compliance with specifications and standards.
Continuous Monitoring and Maintenance
Implement a proactive maintenance strategy that includes regular inspection, lubrication, and calibration of the load system to prevent downtime, extend lifespan, and ensure consistent performance.
Future Trends in Load System Technology
Advanced Materials and Manufacturing Techniques
The use of advanced materials, such as composites and alloys, combined with innovative manufacturing techniques, such as additive manufacturing and precision machining, will enable the development of lighter, stronger, and more durable load systems.
Integration with Industry 4.0 and IoT
Integration of load systems with Industry 4.0 concepts and IoT technologies will enable real-time monitoring, predictive maintenance, and optimization of load performance, enhancing overall efficiency and productivity.
Conclusion
Designing effective load systems is essential for achieving precise and reliable performance in motion control applications. By understanding the factors influencing load system design, addressing key challenges, and adopting best practices, engineers can navigate the complexity of load system design and unlock the full potential of motion control technology.
FAQs
What are some common types of actuators used in load systems?
Common types of actuators include electric motors, pneumatic cylinders, hydraulic actuators, and piezoelectric actuators, each offering specific advantages and limitations depending on the application requirements.
How can I determine the appropriate load capacity for my application?
The appropriate load capacity depends on factors such as the weight, size, and distribution of the load, as well as the dynamic forces and motion profiles involved. Consulting with a knowledgeable engineer or conducting thorough testing and analysis can help determine the optimal load capacity for your application.
What are some strategies for reducing vibrations in load systems?
Strategies for reducing vibrations include using vibration-damping materials, optimizing component stiffness and damping ratios, implementing advanced control algorithms for vibration suppression, and isolating sensitive components from external disturbances.
How can I ensure the reliability of my load system in harsh environments?
Ensuring reliability in harsh environments involves selecting ruggedized components, implementing protective measures such as seals and enclosures, and conducting thorough testing and validation under simulated environmental conditions to verify performance and durability.
What role do feedback systems play in load system design?
Feedback systems, such as encoders and sensors, provide real-time information about the position, velocity, and force of the load, allowing the control system to adjust and optimize performance accordingly. Incorporating feedback systems enhances precision, accuracy, and stability in load system operation.
https://deltasigmacompany.com/
Note: IndiBlogHub features both user-submitted and editorial content. We do not verify third-party contributions. Read our Disclaimer and Privacy Policyfor details.