Precision MEMS Sensors for Accuracy
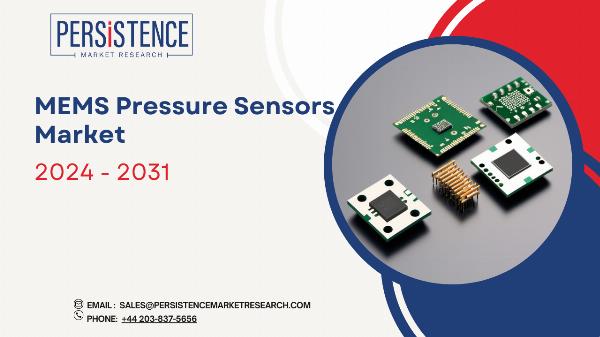
Micro-Electro-Mechanical Systems (MEMS) sensors have revolutionized the way we measure and monitor various physical parameters across multiple industries. Their precision and accuracy make them indispensable in applications ranging from automotive systems to healthcare and industrial automation. This article explores the significance of precision MEMS sensors, their operating principles, advantages, and the future of accuracy in sensor technology.
For More Industry Insight: https://www.persistencemarketresearch.com/market-research/mems-pressure-sensors-market.asp
Understanding MEMS Technology
MEMS technology integrates mechanical components, sensors, actuators, and electronics on a microscopic scale. Precision MEMS sensors are designed to provide highly accurate measurements of parameters such as pressure, temperature, and acceleration. These sensors rely on advanced fabrication techniques, enabling the creation of intricate microstructures that enhance their sensitivity and performance.
The fundamental operation of a MEMS sensor involves detecting changes in physical parameters and converting them into electrical signals. For instance, in a pressure sensor, a diaphragm deforms under pressure, which is then measured by piezoresistive or capacitive sensing elements to produce a corresponding electrical output.
Key Features of Precision MEMS Sensors
High Sensitivity: Precision MEMS sensors can detect minute changes in physical parameters. This sensitivity is critical for applications where even the slightest variations can lead to significant impacts, such as in medical devices or aerospace systems.
Compact Size: The small footprint of MEMS sensors allows for easy integration into existing systems and devices. Their miniaturized design is especially advantageous in applications with space constraints, such as in smartphones and wearable devices.
Low Power Consumption: Many MEMS sensors operate with low power requirements, making them ideal for battery-operated devices. This energy efficiency extends the lifespan of devices and reduces operational costs.
Robustness: Precision MEMS sensors are designed to withstand harsh environmental conditions, including temperature fluctuations and mechanical stress. Their durability ensures reliable performance in demanding applications.
Real-Time Data Processing: With advancements in integrated circuits, many MEMS sensors now offer real-time data processing capabilities. This feature allows for immediate feedback and quick decision-making in critical applications.
Applications of Precision MEMS Sensors
Automotive Industry: Precision MEMS sensors play a crucial role in enhancing vehicle safety and performance. They are used in systems like tire pressure monitoring, where accurate readings are essential for safe driving. Additionally, these sensors are integral to engine control units (ECUs), providing real-time data that optimizes fuel efficiency and reduces emissions.
Healthcare: In the medical field, precision MEMS sensors are vital for monitoring patient health. Devices such as blood pressure monitors, glucose meters, and respiratory devices rely on these sensors to deliver accurate measurements. The ability to provide real-time data is essential for effective patient care and timely medical interventions.
Industrial Automation: In manufacturing and process control, MEMS sensors monitor critical parameters like pressure, temperature, and humidity. Their precision ensures optimal performance and efficiency in automated processes. For example, in HVAC systems, MEMS temperature sensors help maintain desired climate conditions, enhancing energy efficiency.
Aerospace and Defense: Precision MEMS sensors are widely used in aerospace applications for navigation and control systems. In inertial measurement units (IMUs), they measure acceleration and angular velocity, providing crucial data for flight stabilization and navigation. Their reliability is critical in high-stakes environments where accuracy can mean the difference between success and failure.
Consumer Electronics: MEMS sensors are prevalent in consumer electronics, enabling features like motion sensing, environmental monitoring, and touch sensitivity. For instance, smartphones use MEMS accelerometers to detect orientation, enhancing user experiences with applications and games.
Innovations in Precision MEMS Sensor Technology
The ongoing development of precision MEMS sensors is driven by advancements in materials science and manufacturing techniques. Some notable innovations include:
Enhanced Materials: New materials, such as silicon carbide (SiC) and piezoelectric ceramics, are being utilized to improve sensor performance, particularly in harsh environments. These materials enhance durability and expand operational ranges.
Smart Sensors: Integration with artificial intelligence (AI) and machine learning algorithms allows precision MEMS sensors to analyze data trends and patterns, enabling predictive maintenance and improved decision-making in industrial applications.
Wireless Technology: The advent of wireless communication in MEMS sensors eliminates the need for cumbersome wiring, allowing for flexible installations and real-time monitoring in various applications. Wireless MEMS sensors are particularly beneficial in remote monitoring scenarios.
Multi-Functionality: The trend towards multi-functional sensors is on the rise. Modern MEMS sensors can measure multiple parameters, such as pressure, temperature, and humidity, from a single device. This capability simplifies system design and reduces costs.
Challenges and Future Outlook
Despite their advantages, precision MEMS sensors face several challenges:
Calibration and Accuracy: Ensuring long-term accuracy requires regular calibration. Environmental factors can affect sensor performance, necessitating careful selection and calibration of sensors based on specific applications.
Market Competition: As MEMS technology becomes more widespread, competition is intensifying. Manufacturers must continuously innovate to maintain market relevance and meet the evolving demands of various industries.
Integration Complexity: Integrating precision MEMS sensors into existing systems can be complex, particularly in older equipment. Manufacturers must ensure compatibility and ease of installation to facilitate adoption.
Note: IndiBlogHub features both user-submitted and editorial content. We do not verify third-party contributions. Read our Disclaimer and Privacy Policyfor details.