Rock Wool Insulation Manufacturing Plant Project Report 2025: Market Trends, Process, and Project Insights
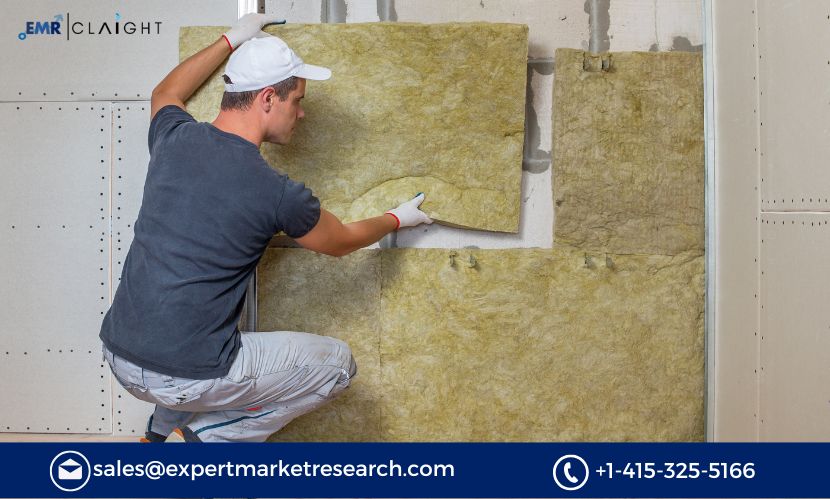
Introduction
Rock wool insulation, also known as mineral wool, is a type of thermal and sound insulation material made from volcanic rock or basalt. It is commonly used in residential, commercial, and industrial construction due to its excellent thermal insulation, fire resistance, and soundproofing properties. The demand for rock wool insulation is rising globally, driven by increased awareness of energy efficiency, sustainability, and green building standards. A Rock Wool Insulation Manufacturing Plant provides an opportunity to meet the growing demand for environmentally friendly building materials while contributing to energy conservation. This Rock Wool Insulation Manufacturing Plant Project Report aims to guide businesses through the essential steps involved in setting up such a plant, including raw material sourcing, production processes, and financial aspects.
Rock Wool Insulation Manufacturing Process
The manufacturing process for rock wool insulation involves the following key stages: raw material preparation, fiberization, binding, curing, cutting, and packaging. Below is a detailed breakdown of the process:
1. Raw Materials
The primary raw materials required for the production of rock wool insulation are:
Basalt or Volcanic Rock: The core material used to produce rock wool, selected for its high melting point and excellent insulation properties.
Binding Agents: Resins, usually phenolic or formaldehyde-based, are used to bind the fibers together and provide structural integrity to the finished product.
Water: Used for cooling and mixing during production.
Additional Additives: Sometimes, additional materials such as oils or lubricants are added to enhance the properties of the rock wool, including hydrophobic treatments or enhanced fire resistance.
2. Melting and Fiberization
The production of rock wool begins by melting basalt or volcanic rock in a furnace. The following steps are involved:
Melting: The basalt is heated in a furnace to a high temperature, usually around 1,500Β°C. The rock becomes molten and is ready for fiberization.
Fiberization: The molten rock is then rapidly spun or blown through fine nozzles to form fibers. The process of fiberization involves creating fine, wool-like strands from the molten rock. These fibers are cooled quickly to maintain their structural integrity.
3. Binding and Curing
After fiberization, the rock wool fibers are mixed with binding agents and additives:
Binding: The rock wool fibers are coated with a binding resin, which helps hold the fibers together and gives the product its desired properties, such as durability and structural strength.
Curing: The rock wool is then passed through an oven or curing tunnel, where the resin is heated to solidify the bonds between the fibers and cure the binding agents. This process ensures that the insulation material retains its shape and mechanical properties.
4. Shaping and Cutting
Once the binding and curing process is complete, the rock wool is shaped and cut into various forms:
Shaping: The rock wool is formed into mats, blankets, or boards, depending on the product requirements. The thickness and density of the final product are adjusted based on the intended application.
Cutting: The insulation material is then cut into specified dimensions, such as rolls, slabs, or custom sizes, depending on market needs.
5. Packaging
After cutting, the rock wool insulation is packaged for distribution. The packaging process includes:
Wrapping: The insulation is wrapped in plastic or other protective materials to prevent contamination and ensure the product is easy to transport and store.
Labeling: Product details such as size, insulation properties, and technical specifications are clearly labeled on the packaging for easy identification.
Key Considerations for Setting Up a Rock Wool Insulation Manufacturing Plant
1. Location and Infrastructure
Choosing the right location for the plant is crucial for operational efficiency. Considerations include:
Proximity to Raw Material Sources: Locating the plant near basalt or volcanic rock quarries can reduce raw material transportation costs. Availability of other materials like resins and additives should also be considered.
Transport and Logistics: The plant should be situated in an area with easy access to transportation routes, including highways and railways, to facilitate the distribution of finished products.
Utility Availability: Ensure that the location provides reliable access to electricity, water, and waste disposal systems. A stable power supply is essential for the high-temperature processes involved in production.
Skilled Workforce: The plant should be located in an area where there is a readily available pool of skilled labor, particularly in manufacturing and construction sectors.
2. Equipment and Technology
The production of rock wool insulation requires specialized equipment:
Furnaces: Used to melt the basalt or volcanic rock at high temperatures.
Fiberizing Equipment: Spinning or blowing nozzles that convert molten rock into fibers.
Mixing Tanks: For combining the rock wool fibers with binding agents and additives.
Curing Ovens: To solidify the binder and ensure the durability of the rock wool insulation.
Cutting Machines: For cutting the rock wool insulation into desired sizes.
Packaging Machines: For wrapping and labeling the final product.
3. Regulatory Compliance and Quality Standards
The rock wool insulation manufacturing plant must adhere to various safety, environmental, and quality standards:
ISO 9001: Certification for quality management systems that ensures consistent product quality and customer satisfaction.
ISO 14001: Certification for environmental management systems, ensuring that the plant follows sustainable practices and minimizes its environmental impact.
Fire Safety Standards: As rock wool insulation is often used for its fire-resistant properties, the plant must meet stringent fire safety standards set by regulatory authorities.
Building Code Compliance: The final products should comply with local or international building regulations, ensuring they meet the necessary standards for thermal and acoustic insulation, fire resistance, and environmental impact.
4. Market Analysis and Demand Forecasting
Before setting up a manufacturing plant, understanding the market demand for rock wool insulation is essential:
Target Market: The primary markets for rock wool insulation include the construction industry, industrial facilities, and residential buildings.
Market Trends: Increasing demand for energy-efficient buildings, green construction, and fireproof materials are driving the growth of rock wool insulation. Regulatory mandates on energy efficiency and sustainability in building codes are further boosting the demand.
Competitive Landscape: Understand the competition in the market, including pricing, product differentiation, and distribution channels. Evaluate major competitorsβ market share and their customer base to carve out a niche.
5. Financial Projections
Starting a rock wool insulation manufacturing plant requires significant capital investment. Key financial aspects include:
Capital Investment: This includes land acquisition, plant construction, machinery, raw materials, and initial working capital.
Operational Costs: Regular expenses include raw material procurement, labor, utilities, maintenance, and administrative costs.
Revenue Forecasting: Revenue projections depend on production capacity, pricing strategy, and market demand.
Return on Investment (ROI): The time it takes to recover the initial investment and begin earning profits. This is determined by factors like operational efficiency, market penetration, and sales volume.
FAQs
1. What is rock wool insulation?
Rock wool insulation is a material made from basalt or volcanic rock that is heated and spun into fibers. It is used for thermal insulation, soundproofing, and fire resistance in buildings and industrial applications.
2. What are the main applications of rock wool insulation?
Rock wool insulation is used in residential buildings, commercial buildings, industrial applications, HVAC systems, and fireproofing. It is ideal for thermal insulation, noise reduction, and fire resistance.
3. Is rock wool insulation environmentally friendly?
Yes, rock wool insulation is made from natural volcanic rock and is highly recyclable. It is considered environmentally friendly due to its long lifespan and energy efficiency.
4. What are the advantages of rock wool insulation over other types?
Rock wool offers excellent fire resistance, soundproofing, and thermal insulation. It is also resistant to mold and mildew, making it ideal for areas with high moisture content.
5. How long does rock wool insulation last?
Rock wool insulation is durable and has a long lifespan, often lasting the lifetime of the building. It does not degrade over time and maintains its performance for many years.
Media Contact
Company Name: Claight Corporation
Contact Person: Lewis Fernandas, Corporate Sales Specialist β U.S.A.
Email: [email protected]
Toll Free Number: +1β415β325β5166 | +44β702β402β5790
Address: 30 North Gould Street, Sheridan, WY 82801, USA
Website: www.expertmarketresearch.com
Aus Site: https://www.expertmarketresearch.com.au
Note: IndiBlogHub features both user-submitted and editorial content. We do not verify third-party contributions. Read our Disclaimer and Privacy Policyfor details.