Two Wheeler Clutch Plate Manufacturing Plant Project Report 2024: Machinery and Technology Requirements
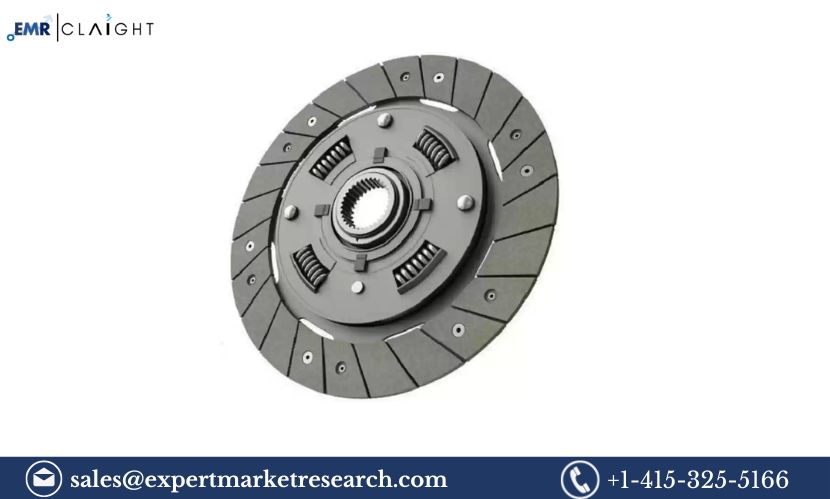
Introduction
The Two Wheeler Clutch Plate Manufacturing Plant Project Report provides a comprehensive blueprint for establishing a facility dedicated to producing clutch plates for two-wheelers. Clutch plates are a crucial component of a motorcycle's transmission system, allowing the rider to smoothly engage or disengage the engine's power to the wheels. With the increasing demand for two-wheelers globally, driven by growing urbanization, affordability, and changing lifestyles, the demand for reliable and high-quality clutch plates is also on the rise.
This report outlines the steps involved in setting up a manufacturing plant for two-wheeler clutch plates, including an overview of the production process, equipment required, market analysis, raw materials, and financial considerations to establish and operate a successful plant. It aims to serve as a guide for entrepreneurs and investors looking to enter the automotive parts manufacturing industry, specifically in the two-wheeler market.
Understanding Two Wheeler Clutch Plates
A clutch plate is an essential part of the transmission system in a motorcycle or scooter. It is responsible for transmitting power from the engine to the wheels while allowing the rider to disengage the engine power when shifting gears. Clutch plates are designed to handle extreme levels of heat, friction, and pressure as they engage and disengage the engine’s power.
Types of Clutch Plates:
Friction Plates: These plates are made from materials that provide high friction, allowing the clutch to engage and disengage smoothly. They are usually made of a combination of metal and friction material like organic compounds or sintered metal.
Steel Plates: Steel plates serve as the backing for the friction plates and are used in conjunction to transfer the pressure applied when the clutch lever is engaged. They are durable and resistant to wear.
Clutch Springs: These are used to apply the necessary force to hold the clutch plates in place and maintain their engagement during operation.
Function of Clutch Plates:
Power Transmission: The clutch plates transmit power from the engine to the transmission and ultimately to the wheels, allowing the rider to control speed and acceleration.
Smooth Gear Shifting: The clutch helps disengage the engine power momentarily when shifting gears, preventing grinding and allowing for smooth transitions between gears.
Durability: Clutch plates are designed to withstand wear and heat generated during the frictional process. They must be durable enough to handle long periods of use.
Market Demand for Two Wheeler Clutch Plates
The global two-wheeler market is expanding at a rapid pace, driven by factors such as urbanization, increasing disposable incomes, and the rising popularity of motorcycles and scooters for daily commuting. This has led to a corresponding demand for high-quality automotive parts, including clutch plates.
Key Factors Driving Market Growth:
Increasing Two-Wheeler Sales: As motorcycle and scooter sales rise worldwide, the demand for spare parts, particularly clutch plates, also increases.
Automotive Aftermarket Growth: Many two-wheeler owners prefer to replace parts like clutch plates during regular maintenance or repair, leading to consistent demand in the aftermarket sector.
Technological Advancements in Clutch Design: As manufacturers develop better-performing clutch systems that improve the overall riding experience, there is a rising demand for high-quality clutch plates that can withstand more heat and pressure.
Key Market Segments:
OEM (Original Equipment Manufacturers) Market: Clutch plates manufactured for new two-wheelers, where suppliers provide components for assembly lines.
Aftermarket Sales: Replacement clutch plates for existing motorcycles and scooters, which form a significant portion of the demand.
Regional Insights:
Asia-Pacific: The region is the largest consumer of two-wheelers globally, particularly in countries like India, China, and Indonesia. This drives the demand for clutch plates for both new vehicles and the aftermarket.
Europe and North America: Although two-wheeler adoption is lower compared to Asia, the demand for clutch plates remains steady, particularly for high-performance motorcycles.
Steps to Set Up a Two Wheeler Clutch Plate Manufacturing Plant
Setting up a two-wheeler clutch plate manufacturing plant involves a combination of strategic planning, investment in infrastructure, and establishing efficient manufacturing processes. Below are the essential steps to set up the plant.
1. Feasibility Study and Market Research
A feasibility study is crucial to assess the viability of the clutch plate manufacturing business. This includes:
Market Demand Analysis: Evaluate the market demand for clutch plates, both in terms of OEM production and replacement parts. This includes identifying target customers (OEMs, aftermarket distributors, or end customers).
Cost Analysis: Estimate the initial capital investment required for setting up the plant, as well as operational costs such as labor, utilities, and raw materials.
Competitor Analysis: Analyze competitors in the clutch plate manufacturing space, focusing on their market share, product quality, pricing strategies, and production processes.
2. Site Selection
Choosing the right location for the manufacturing plant is crucial for smooth operations. Some key factors to consider include:
Proximity to Raw Material Suppliers: Access to suppliers of materials like steel, friction compounds, and other materials is essential to minimize transportation costs.
Labor Availability: Ensure the location has access to a skilled workforce or the ability to train workers in manufacturing processes.
Transportation Infrastructure: Good road and rail connectivity is important for the movement of raw materials and finished products.
3. Raw Materials and Components
The key raw materials required for manufacturing clutch plates include:
Steel Plates: For the base of the clutch plate.
Friction Material: Typically made of organic compounds, carbon composites, or sintered metals for providing the necessary friction.
Clutch Springs and Rivets: For assembling the clutch plate components.
Heat-resistant Coatings: Used to ensure durability and heat resistance in the clutch plates.
4. Equipment and Technology
The manufacturing of two-wheeler clutch plates requires various specialized machinery and equipment, such as:
Pressing Machines: These are used to form the steel plates and the friction material into the desired shape.
CNC Machines: Used for precision cutting and machining of clutch plates to ensure uniformity in thickness, diameter, and overall design.
Heat Treatment Furnace: Used for hardening the clutch plates, making them more durable and heat-resistant.
Riveting Machines: For attaching springs and other components to the clutch plates.
Quality Control and Testing Equipment: To ensure that the finished products meet industry standards and specifications for strength, heat resistance, and durability.
5. Manufacturing Process
The process for manufacturing two-wheeler clutch plates involves the following steps:
Raw Material Preparation: Steel plates are cut into the required shapes, and the friction material is pre-processed for molding.
Stamping and Forming: The steel plates are stamped or pressed into the required shape using specialized dies and molds.
Heat Treatment: The formed steel plates are subjected to heat treatment to enhance their strength and durability, allowing them to withstand high temperatures and pressure.
Friction Material Application: Friction materials are applied to the plates, either by bonding or pressing.
Assembly: The clutch plates are assembled, often with springs or other components like rivets, depending on the design.
Quality Control and Testing: The plates undergo rigorous testing for their functionality, strength, durability, and ability to withstand wear and tear.
6. Packaging and Distribution
Once the clutch plates are manufactured, they need to be packaged and prepared for shipping to OEMs, distributors, and retailers. The packaging process involves labeling, quality checks, and storing the products in a safe manner.
7. Regulatory Compliance and Safety Standards
Complying with industry standards and regulations is crucial to ensure product quality and consumer safety. Some of the important standards include:
ISO Certification: Ensures that the manufacturing process meets global quality standards.
Environmental Compliance: Manufacturers must adhere to environmental regulations related to waste disposal, emissions, and energy use.
Safety Standards: The factory must comply with occupational health and safety standards to ensure worker safety.
Financial Considerations
Setting up a two-wheeler clutch plate manufacturing plant requires significant financial investment. Some key financial considerations include:
Capital Investment: The initial capital required for purchasing land, machinery, and setting up production lines.
Operational Costs: This includes raw materials, labor, utilities, and overhead expenses.
Revenue Projections: Estimated income from selling clutch plates to OEMs, aftermarket suppliers, and end customers.
Profitability Analysis: Analyzing the break-even point, return on investment, and long-term profitability of the plant.
FAQs
1. What is the role of a clutch plate in a two-wheeler?
A clutch plate is an essential component of the two-wheeler's transmission system, allowing the rider to engage or disengage engine power from the wheels.
2. What materials are used to manufacture clutch plates?
Clutch plates are typically made from steel and high-friction materials like organic compounds or sintered metals.
3. How does the manufacturing process work?
The process involves stamping or pressing steel plates, applying friction materials, heat treatment, and assembling the plates before undergoing quality testing.
4. What are the key challenges in clutch plate manufacturing?
Key challenges include ensuring high-quality standards, minimizing defects, and adapting to the increasing demand for more durable and heat-resistant clutch plates.
5. Who are the primary customers for clutch plates?
Primary customers include OEMs (motorcycle manufacturers), aftermarket suppliers, and distributors who sell replacement parts for two-wheelers.
Media Contact:
Company Name: Claight Corporation
Contact Person: Lewis Fernandas, Corporate Sales Specialist — U.S.A.
Email: [email protected]
Toll Free Number: +1–415–325–5166 | +44–702–402–5790
Address: 30 North Gould Street, Sheridan, WY 82801, USA
Note: IndiBlogHub features both user-submitted and editorial content. We do not verify third-party contributions. Read our Disclaimer and Privacy Policyfor details.