What Are the Latest Trends in Mold Making and Plastic Molding Industries?
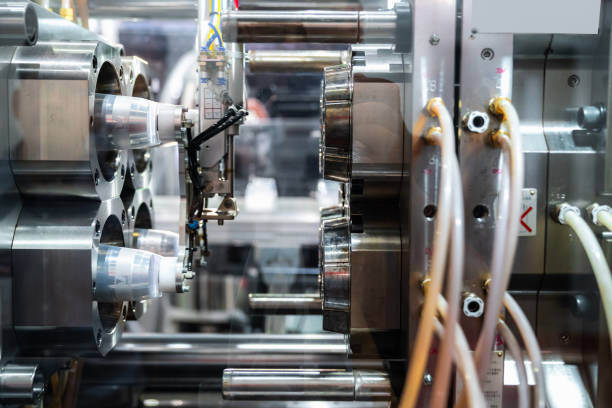
The mold-making and plastic molding industries constantly change. The development of technology, sustainable practices, and new demands from the markets bring about changes. Understanding recent trends makes companies like NUBS Plastics Inc. keep up-to-date and always one step ahead in competition and offer quality products to medical electronics and even consumer goods industries. In this article, we will understand the trends and the plastic molding company in depth.
1. Integration of 3D printing and rapid prototyping
Additive manufacturing is also referred to as three-dimensional printing. It is among the pivotal tools in mold-making, where three-dimensional printing fastens the procedure of making prototypical molds before mass production, thereby testing and simplifying it along the way, which accelerates production but also comes with the potential of reducing the costs of earlier prototyping technologies. Companies would be able to produce geometrical complexities that might have been daunting earlier with just 3-D printing. That is the direction toward greater ease in design plus innovation.
2. Adoption of Advanced Materials
The demand for high-performance, eco-friendly materials is changing the plastic molding industry. Engineered plastics and composites, with superior characteristics such as improved thermal resistance and lower weight, are increasingly used. These are particularly valuable within sectors such as automotive and aerospace, where performance and efficiency are critical. Thus, today, mold making company can use advanced materials to meet specific industry requirements.
3. Sustainability
Environmental factors increasingly dictate manufacturing processes. Companies specializing in plastic molding incorporate green solutions, such as recycled and biodegradable products, into product development. Moreover, organizations design molds that reduce waste and energy consumption during manufacturing processes. Sustainable practices have many benefits, such as a smaller footprint and progress toward the consumers' desire for greener products.
4. Automation and Smart Technologies Implementation
Automation is revolutionizing the mold-making and plastic molding industries. Incorporating robotic systems and smart technologies makes production more efficient, precise, and consistent. Automated machinery can perform repetitive tasks, thus cutting labor costs and minimizing human error. Additionally, sensors and Internet of Things (IoT) devices in molds enable the real-time monitoring of pressure and temperature parameters, making proactive maintenance and quality control easier.
5. Artificial Intelligence in Designing
Artificial Intelligence is being used extensively in mold design. AI algorithms can process large data sets to optimize design parameters, predict potential issues, and provide improvements. This creates more efficient and effective molds suited to the needs of the manufacturing process. Complex calculations and simulations can be automated, thus speeding up the design process and enhancing the quality of the final product.
6. Focus on High Precision Molding
The need for precision injection molds has increased as electronic and medical devices become miniaturized. High-precision injection molds are needed to produce very small and complex parts with very tight tolerances, which are necessary for gadgets and medical instruments. The requirement for precision pushes forward mold design innovations and creates sophisticated molding machines that can precisely carry out complicated tasks.
7. Multi-material injection molding expansion
With this trend, many materials come together in a single molding process. Multi-material molding is good for creating complicated parts with changing properties, such as colors, textures, or mechanical properties. This technique is especially useful for components requiring rigidity and flexibility or for integrating soft-touch surfaces with hard substrates. With multi-material molding, plastic molding companies can provide their clients with more versatile and innovative solutions.
8. Quality Assurance Commitment
Quality checks at each production stage ensure the products deliver value and function effectively. Advanced inspection technologies, such as automated optical inspection systems and coordinate measuring machines, are integrated into plastic molding company so that each piece meets the specified standard. Formidable quality-assurance measures at an early stage help reduce waste and develop customer satisfaction.
Conclusion
In conclusion, the mold-making and plastic-molding industries have been dynamically changing and are powered by the development of new technology and the pursuit of sustainability and accuracy. Companies such as NUBS Plastics Inc. remain at the forefront of adopting trends to ensure they continue to lead in delivering front-line solutions to different sectors. However, companies adopting advancements in 3D printing, advanced materials, automation, AI, and multi-material molding are poised to thrive and serve emerging market needs and requirements, leading toward a more efficient and sustainable manufacturing domain.
Note: IndiBlogHub features both user-submitted and editorial content. We do not verify third-party contributions. Read our Disclaimer and Privacy Policyfor details.