What is the difference Quality Between HDPE and LDPE sheets?
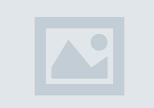
HDPE (High-Density Polyethylene) sheets and LDPE (Low-Density Polyethylene) sheets are both types of plastic sheets, but they differ in several key aspects, including their molecular structure, physical properties, and typical applications ,HDPEย sheets.
Molecular Structure:
HDPE: High-Density Polyethylene has a higher density and a more linear molecular structure compared to LDPE. This molecular arrangement results in greater strength, stiffness, and resistance to heat and chemicals.
LDPE: Low-Density Polyethylene has a more branched and less dense molecular structure. It is softer, more flexible, and exhibits higher elongation properties compared to HDPE.
Physical Properties:
HDPE: HDPE sheets are known for their exceptional strength, durability, and rigidity. They offer excellent resistance to impact, abrasion, and chemical exposure, making them suitable for applications requiring toughness and dimensional stability.
LDPE: LDPE sheets are characterized by their flexibility, elasticity, and low tensile strength. They are more prone to deformation under load and have lower resistance to abrasion and chemical solvents compared to HDPE.
Typical Applications:
HDPE: HDPE sheets find applications in industries requiring robust and durable materials, such as construction, packaging, automotive, and marine sectors. Common uses include water and chemical storage tanks, pipes, playground equipment, cutting boards, and outdoor furniture.
LDPE: LDPE sheets are commonly used in applications where flexibility, impact resistance, and ease of fabrication are paramount. They are often employed in packaging materials, plastic bags, shrink wraps, agricultural films, and flexible tubing.
Performance Under Different Conditions:
HDPE: Due to its higher density and molecular structure, HDPE sheets exhibit superior resistance to environmental factors such as temperature fluctuations, UV radiation, and chemical exposure. This makes them well-suited for outdoor applications where durability and weather resistance are crucial.
LDPE: While LDPE sheets offer excellent flexibility and impact resistance, they are more susceptible to degradation from UV radiation and temperature extremes. Therefore, LDPE may not be suitable for prolonged outdoor exposure or applications requiring resistance to harsh environmental conditions.
Environmental Impact:
HDPE: High-Density Polyethylene is considered a relatively environmentally friendly material due to its recyclability and durability. HDPE products can be recycled into new items, reducing waste and conserving resources. Additionally, HDPE's resistance to chemical degradation means it can withstand harsh conditions without leaching harmful substances into the environment.
LDPE: Low-Density Polyethylene is also recyclable, but its lower density and flexibility make it less suitable for some recycling processes compared to HDPE. LDPE products may have a shorter lifespan due to their lower durability, potentially leading to more frequent replacement and increased waste generation.
Cost Considerations:
HDPE: While HDPE sheets may have a higher initial cost compared to LDPE, their durability and longevity often result in lower lifecycle costs. HDPE's resistance to wear and tear means it may require less frequent replacement, saving money in the long run.
LDPE: LDPE sheets are typically more affordable upfront due to their lower production costs. However, their shorter lifespan and lower durability may result in higher overall costs over time, especially in applications requiring long-term performance and reliability.
Summary:
In summary, the main differences between HDPE and LDPE sheets lie in their molecular structure, physical properties, and typical applications. HDPE sheets offer superior strength, rigidity, and chemical resistance, making them suitable for demanding applications requiring durability and dimensional stability. On the other hand, LDPE sheets excel in flexibility, elasticity, and ease of fabrication, making them ideal for applications where flexibility and impact resistance are essential. Understanding these differences is crucial for selecting the right material for specific project requirements.
Note: IndiBlogHub features both user-submitted and editorial content. We do not verify third-party contributions. Read our Disclaimer and Privacy Policyfor details.