Advanced Technologies in Additive Manufacturing: Metal Additive Manufacturing Trends
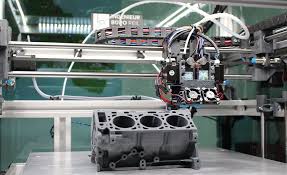
Introduction to Additive Manufacturing
Additive Manufacturing (AM), commonly known as 3D printing, has revolutionized various industries by enabling the creation of complex geometries and customized products. Unlike traditional subtractive manufacturing methods, which involve cutting away material from a solid block, AM builds objects layer by layer from digital models. This process significantly reduces material waste and allows for innovative design possibilities. Among the various forms of AM, metal additive manufacturing has garnered significant attention due to its potential to produce strong, lightweight components for critical applications.
In this article, we will delve into the latest trends in metal additive manufacturing, focusing on emerging techniques such as binder jetting and directed energy deposition. We will explore their applications, particularly in the aerospace and automotive industries, where precision and performance are paramount.
Understanding Metal Additive Manufacturing
Metal additive manufacturing encompasses several techniques that allow for the creation of metal parts using additive processes. Key methods include:
1. Powder Bed Fusion (PBF)
2. Directed Energy Deposition (DED)
3. Binder Jetting
Each of these techniques has its own unique advantages and challenges, making them suitable for different applications and industries.
Emerging Techniques in Metal Additive Manufacturing
Binder Jetting
Overview
Binder jetting is an innovative additive manufacturing technique that involves the selective deposition of a binder liquid onto a bed of metal powder. The process creates a "green" part, which is then sintered to fuse the particles together and achieve the desired mechanical properties. This method is particularly noteworthy for its ability to produce complex geometries and multi-material components without the need for support structures.
Trends and Developments
1. Increased Material Range: Recent advancements have expanded the range of materials that can be utilized in binder jetting, including high-performance alloys and composites. This diversification enhances the method's applicability across various sectors.
2. Improved Sintering Techniques: Innovations in sintering technology, including the use of advanced furnace designs and atmospheres, have improved the mechanical properties and density of parts produced via binder jetting.
3. Rapid Prototyping and Production: Binder jetting is becoming a go-to method for rapid prototyping, enabling manufacturers to quickly iterate designs and reduce lead times.
4. Cost-Effectiveness: As technology advances, the cost of binder jetting is decreasing, making it more accessible for small and medium-sized enterprises (SMEs) in addition to large manufacturers.
Applications in Aerospace and Automotive
โข Aerospace: Binder jetting is being employed to produce lightweight, complex components for aircraft, such as brackets and housings. Its ability to create intricate designs helps reduce weight and improve fuel efficiency.
โข Automotive: In the automotive sector, binder jetting is used for manufacturing parts like engine components and custom tooling, providing manufacturers with the flexibility to produce low-volume, high-performance parts.
Directed Energy Deposition (DED)
Overview
Directed energy deposition is another prominent technique in metal additive manufacturing. It involves the deposition of material onto a substrate using focused energy sources like lasers or electron beams. DED allows for the fabrication of near-net-shape components and the repair of existing parts, making it a versatile method for various applications.
Trends and Developments
1. Hybrid Manufacturing Systems: There is a growing trend toward integrating DED with traditional machining processes. Hybrid systems allow for the repair and additive manufacturing of components in a single setup, optimizing production efficiency.
2. Advanced Material Properties: DED techniques are being refined to produce components with superior mechanical properties, including improved fatigue resistance and thermal stability. This is particularly beneficial in industries where performance under extreme conditions is critical.
3. Automation and Control: Enhanced automation and real-time monitoring systems are being developed to improve the consistency and quality of DED processes. These advancements help reduce defects and improve overall production rates.
4. Scalability: DED technology is becoming more scalable, allowing for the production of larger components that are essential in aerospace and heavy machinery applications.
Applications in Aerospace and Automotive
โข Aerospace: DED is extensively used for manufacturing critical engine components, such as turbine blades and fuel nozzles. The ability to repair high-value components extends their life cycle and reduces material waste.
โข Automotive: In the automotive industry, DED is utilized for producing parts that require high strength-to-weight ratios. This is particularly important for electric vehicles (EVs), where reducing weight can enhance battery efficiency.
Comparing Binder Jetting and Directed Energy Deposition
While both binder jetting and directed energy deposition have unique advantages, they cater to different manufacturing needs. Binder jetting excels in producing complex geometries with lower costs, making it ideal for prototyping and production of non-critical parts. In contrast, DED is better suited for applications requiring high-performance materials and the ability to repair existing components.
Advantages and Limitations
โข Binder Jetting:
o Advantages: Cost-effective, versatile material use, no need for support structures.
o Limitations: Lower mechanical properties compared to DED, requires post-processing for final part strength.
โข Directed Energy Deposition:
o Advantages: High-performance materials, repair capabilities, larger component production.
o Limitations: Higher initial setup costs, more complex process control.
Future Outlook for Metal Additive Manufacturing
The future of metal additive manufacturing is bright, driven by continuous advancements in technology and materials. Key trends that are likely to shape the landscape include:
1. Increased Adoption of Industry 4.0: As manufacturers embrace Industry 4.0 principles, integrating AM technologies with IoT, AI, and data analytics will lead to smarter production processes.
2. Sustainability Initiatives: With growing concerns about environmental impact, AM's ability to reduce waste and enable recycling of materials will become increasingly important. The development of sustainable metal powders is also on the rise.
3. Collaborative Manufacturing: The trend toward collaborative manufacturing networks will facilitate the sharing of AM technologies and expertise, allowing smaller manufacturers to access advanced capabilities.
4. Regulatory Developments: As metal additive manufacturing becomes more prevalent, regulatory bodies will need to establish standards and guidelines to ensure safety and quality, particularly in aerospace and automotive sectors.
Conclusion
Advanced technologies in metal additive manufacturing, particularly binder jetting and directed energy deposition, are reshaping the landscape of production in the aerospace and automotive industries. These emerging techniques are not only enhancing design capabilities but also contributing to more sustainable manufacturing practices. As the technology continues to evolve, it promises to unlock new possibilities for innovation, efficiency, and performance in metal part production.
See the full article: https://www.nextmsc.com/blogs/additive-manufacturing-market-trends
Note: IndiBlogHub features both user-submitted and editorial content. We do not verify third-party contributions. Read our Disclaimer and Privacy Policyfor details.