Air and Manual Actuator: Combining Safety with Performance
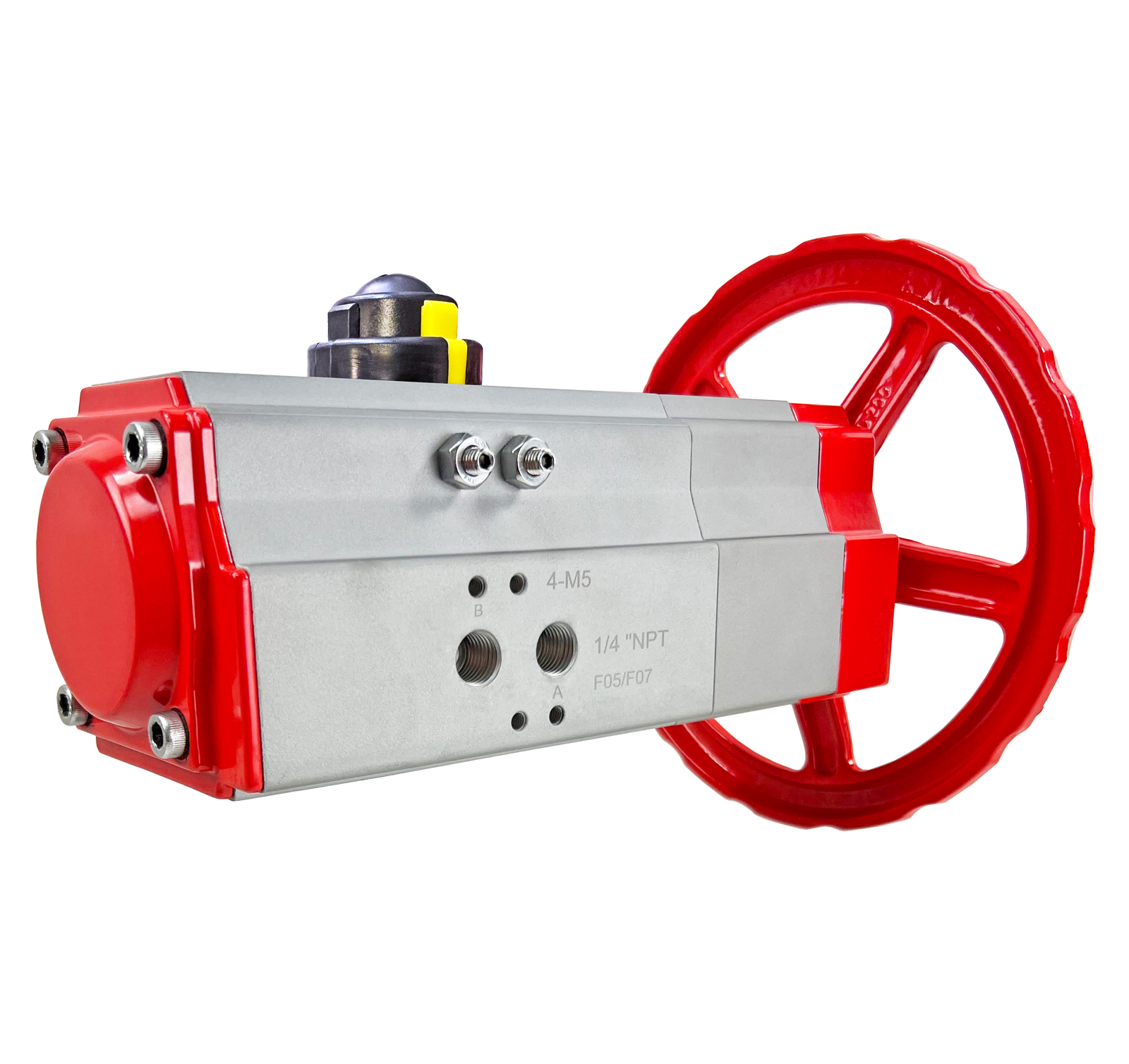
Industrial valve control systems face constant pressure to deliver both automation efficiency and operational safety. The air and manual actuator represents a breakthrough solution that addresses these dual requirements, offering pneumatic automation capabilities alongside manual backup controls. This versatile combination ensures continuous operation even during power failures or maintenance situations, making it an essential component in critical industrial applications.
The integration of pneumatic and manual control systems within a single actuator unit provides operators with unprecedented flexibility. When automation systems function normally, the pneumatic components deliver precise, rapid valve positioning. Should technical issues arise, operators can seamlessly transition to manual control without system downtime. This redundancy proves invaluable in industries where process interruption carries significant safety or economic consequences.
Understanding how these combination actuators achieve their dual functionality helps engineers and operators maximize their potential. The design incorporates sophisticated mechanical linkages that allow smooth transitions between automated and manual operation modes. This seamless integration maintains consistent valve control regardless of the active operating mode.
Understanding Air and Manual Actuator Technology
Core Components and Design Philosophy
Air and manual actuators integrate two distinct control mechanisms within a unified housing. The pneumatic system utilizes compressed air to generate the primary operating force, while the manual system provides mechanical backup through handwheels, levers, or gear trains. This dual-system approach ensures operational continuity under all circumstances.
The pneumatic portion typically features a spring-return mechanism that positions the valve safely during air supply interruptions. This fail-safe design automatically moves the valve to a predetermined position when system pressure drops below operational thresholds. The manual override system allows operators to maintain control during these emergency conditions.
Advanced actuator designs incorporate declutching mechanisms that prevent interference between pneumatic and manual systems. When manual operation becomes necessary, the declutching system disengages the pneumatic components, allowing full manual control without fighting against air pressure or spring forces.
Operational Modes and Switching Mechanisms
Modern combination actuators support multiple operational modes to accommodate various process requirements. Normal automated operation relies on pneumatic power to position valves according to control system commands. The manual mode provides direct operator control through mechanical interfaces, useful during maintenance or emergency situations.
The transition between modes occurs through carefully engineered switching mechanisms. Some actuators feature automatic switching that activates manual mode when pneumatic pressure drops below specified levels. Others require deliberate operator action to engage manual control, providing additional safety through intentional mode selection.
Position indication systems track valve positioning regardless of the active control mode. These systems ensure operators maintain awareness of valve status during mode transitions, preventing operational confusion or safety hazards.
Performance Advantages in Industrial Applications
Enhanced System Reliability
The combination of pneumatic and manual control systems significantly improves overall system reliability. Single-point failures that might disable purely pneumatic systems become manageable events when manual backup remains available. This redundancy reduces unplanned downtime and maintenance costs.
Statistical analysis of actuator performance shows that combination units achieve availability rates exceeding 99.5% in typical industrial applications. This exceptional reliability stems from the independent nature of the pneumatic and manual systems, which rarely experience simultaneous failures.
Maintenance flexibility represents another reliability advantage. Pneumatic components can undergo servicing while manual operation maintains process continuity. This approach eliminates the need for complete system shutdowns during routine maintenance activities.
Improved Safety Performance
Safety performance benefits from the inherent redundancy of combination actuators. Emergency valve positioning remains possible even during complete automation system failures. This capability proves critical in process industries where rapid valve closure prevents catastrophic incidents.
The manual override system provides operators with direct physical control over valve positioning. This hands-on capability builds operator confidence and ensures human intervention remains possible during complex emergency scenarios. Many safety standards specifically require manual override capabilities for critical valve applications.
Fail-safe positioning through spring-return mechanisms adds another safety layer. These systems automatically position valves safely when air supply fails, preventing dangerous process conditions from developing during power outages or equipment failures.
Operational Flexibility and Efficiency
Combination actuators accommodate diverse operational requirements within a single system. Process startup procedures often require manual valve positioning before automated control becomes active. The integrated manual system eliminates the need for separate manual valves during these transitional periods.
Maintenance efficiency improves through the ability to test and calibrate systems using manual operation. Technicians can verify valve travel, seating, and positioning without requiring full automation system activation. This capability simplifies commissioning procedures and reduces testing time.
Energy efficiency benefits from the option to operate valves manually during low-demand periods. Some facilities switch to manual operation during maintenance windows or reduced production periods, eliminating compressed air consumption for non-critical valve positioning.
Installation and Setup Considerations
System Integration Requirements
Successful installation requires careful coordination between pneumatic, mechanical, and electrical systems. The pneumatic supply must provide clean, regulated air at appropriate pressure levels throughout the actuator's operating range. Contaminated or inadequately pressurized air causes performance degradation and component wear.
Mechanical mounting systems must accommodate the additional complexity of combination actuators. These units typically require more installation space than simple pneumatic actuators due to the integrated manual components. Proper clearance ensures both pneumatic and manual operation remain accessible.
Electrical integration involves connecting position feedback systems, limit switches, and control interfaces. Modern combination actuators often include sophisticated electronics that require proper grounding, shielding, and surge protection. Following manufacturer specifications prevents electrical interference and component damage.
Calibration and Testing Procedures
Calibration procedures must address both pneumatic and manual operating modes. Pneumatic calibration involves adjusting pressure settings, response times, and position accuracy to meet process requirements. Manual calibration focuses on operating effort, position indication, and smooth operation throughout the valve's travel range.
Testing protocols should verify proper operation under various conditions including normal operation, emergency scenarios, and mode transitions. These tests ensure the actuator performs reliably under all anticipated operating conditions. Documentation of test results provides baseline data for future troubleshooting and maintenance activities.
Safety system testing receives particular attention during commissioning. Fail-safe operation, emergency stops, and position interlocks must function correctly to prevent accidents. Regular testing schedules maintain safety system reliability throughout the actuator's service life.
Maintenance and Troubleshooting Strategies
Preventive Maintenance Approaches
Effective maintenance programs address both pneumatic and manual components through targeted inspection and service procedures. Pneumatic components require regular lubrication, seal replacement, and air supply system maintenance. Manual components need periodic lubrication, adjustment, and wear inspection.
Condition monitoring systems track actuator performance parameters including response time, positioning accuracy, and operating forces. These systems identify developing problems before they cause failures, enabling proactive maintenance scheduling and cost optimization.
Spare parts management becomes more complex with combination actuators due to the dual system components. Maintaining appropriate inventory levels for both pneumatic and manual parts ensures rapid repair capability when failures occur.
Common Issues and Solutions
Pneumatic system problems typically involve air supply contamination, pressure regulation failures, or seal degradation. Regular air system maintenance, including filter replacement and moisture removal, prevents most pneumatic issues. Seal replacement follows predictable schedules based on operating cycles and environmental conditions.
Manual system problems often stem from inadequate lubrication, mechanical wear, or improper adjustment. Regular lubrication schedules prevent most manual operation issues. Proper adjustment techniques ensure smooth operation and appropriate operating forces throughout the actuator's service life.
Mode switching problems require specialized troubleshooting procedures. These issues often involve mechanical linkages, electrical controls, or operator training deficiencies. Systematic diagnosis procedures identify root causes and guide effective corrective actions.
Maximizing Performance and Longevity
The combination of pneumatic automation and manual backup control represents a significant advancement in valve actuator technology. These systems deliver exceptional reliability, safety, and operational flexibility while maintaining the efficiency benefits of automated control. Success depends on proper installation, regular maintenance, and comprehensive operator training.
Organizations implementing combination actuators should invest in thorough training programs that cover both pneumatic and manual operation procedures. This knowledge ensures operators can effectively utilize all system capabilities while maintaining safety standards. Regular refresher training keeps skills current as technology evolves.
Future developments in combination actuator technology promise even greater integration between pneumatic and manual systems. Smart actuators with advanced diagnostics, predictive maintenance capabilities, and improved human-machine interfaces will further enhance the value proposition of these versatile systems.
Note: IndiBlogHub features both user-submitted and editorial content. We do not verify third-party contributions. Read our Disclaimer and Privacy Policyfor details.