Data-Driven Six Sigma Process: A Comprehensive Guide
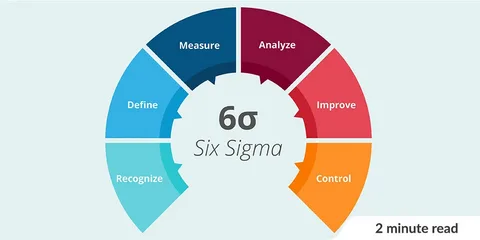
In today's highly competitive business landscape, companies must continually improve processes to stay ahead. Six Sigma is one of the most effective methodologies for achieving this goal, focusing on quality improvement through data-driven decisions. The fusion of Six Sigma with a data-driven approach allows businesses to optimize operations, reduce defects, and enhance customer satisfaction. This blog delves into how the data-driven Six Sigma processΒ works and how it can transform your organization.
1. What is Six Sigma?
Six Sigma is a disciplined, data-driven methodology used to eliminate defects in any process. The goal is to achieve near perfection in quality management by focusing on measurable financial returns and enhancing customer satisfaction. Six Sigma follows a structured problem-solving approach, known as DMAIC (Define, Measure, Analyze, Improve, Control).
2. The Importance of Data in Six Sigma
The success of Six Sigma is heavily dependent on accurate data. Data serves as the backbone of the methodology, providing the necessary insights to make informed decisions. Without data, it's nearly impossible to identify defects, inefficiencies, or areas of improvement. This is why a data-driven Six Sigma process is crucial for maximizing results.
3. The DMAIC Process
The Six Sigma process follows five key stages, known as DMAIC:
Define
In this phase, the problem is defined. The objective is to identify the process that needs improvement and determine customer requirements and business goals. Critical metrics are also set during this stage.
Measure
The Measure phase involves gathering relevant data to understand the current performance level. This data will serve as the baseline for any improvements. Key performance indicators (KPIs) are identified and measured to assess the effectiveness of the process.
Analyze
During the Analyze phase, the collected data is examined to identify root causes of defects or inefficiencies. Data analysis tools such as Pareto charts, histograms, and scatter plots are often used to uncover patterns and problem areas.
Improve
Once the root causes are identified, the Improve phase focuses on developing solutions to eliminate defects and optimize the process. Data is again used to validate the effectiveness of these solutions.
Control
The final phase is Control, where measures are implemented to ensure the improvements are sustained over time. Data is continuously monitored to ensure the process remains stable and any variations are addressed promptly.
4. The Role of Data in Each DMAIC Stage
Define Phase:
Data-Driven Insight: Understanding customer needs and identifying problems is critical. Surveys, customer feedback, and market data help define the scope and set measurable goals.
Measure Phase:
Data Collection: Gathering performance data such as defect rates, cycle times, and production capacity. Data ensures accurate benchmarking before improvement begins.
Analyze Phase:
Root Cause Analysis: Data analytics is essential in determining the root causes of defects. Statistical tools, such as regression analysis and hypothesis testing, guide the identification of critical factors.
Improve Phase:
Solution Validation: Data is used to evaluate the effectiveness of proposed solutions. Simulation models and pilot testing with actual data help ensure success before full implementation.
Control Phase:
Ongoing Monitoring: Control charts and continuous data monitoring ensure the improvements are maintained. Regular data reviews enable timely corrections if the process deviates.
5. Tools for Data-Driven Six Sigma
Several tools are used to facilitate a data-driven Six Sigma process:
Control Charts: Monitor process variation over time.
Pareto Analysis: Identifies the most common causes of defects.
Fishbone Diagrams: Helps in identifying cause-and-effect relationships.
Histograms: Visual representation of data distribution.
Hypothesis Testing: Validates assumptions with data.
6. Benefits of a Data-Driven Approach in Six Sigma
Implementing Six Sigma with a focus on data provides several benefits:
Improved Decision-Making: Data eliminates guesswork, leading to more informed decisions.
Reduced Variability: Data helps identify and reduce variations in processes.
Increased Efficiency: Process improvements based on data lead to faster, more efficient operations.
Cost Reduction: Data-driven decisions help eliminate waste and reduce operational costs.
Higher Customer Satisfaction: A better understanding of customer requirements through data improves product and service quality.
7. Common Challenges and Solutions
While the data-driven Six Sigma process is highly effective, it comes with challenges:
Data Overload: With an overwhelming amount of data available, it can be difficult to focus on what matters. Solution: Prioritize critical data and filter out irrelevant information.
Data Accuracy: Incorrect data can lead to flawed decisions. Solution: Implement data validation protocols to ensure accuracy.
Resistance to Change: Employees may resist new processes based on data. Solution: Engage employees early and use data to demonstrate the benefits of the change.
8. Real-World Applications of Data-Driven Six Sigma
Several leading companies have successfully implemented Six Sigma to optimize their processes:
General Electric (GE): GE saved billions of dollars by applying Six Sigma to improve operational efficiency.
Motorola: Motorola, the pioneer of Six Sigma, used the methodology to reduce manufacturing defects, leading to significant cost savings.
Honeywell: Data-driven Six Sigma helped Honeywell enhance product quality and reduce waste, contributing to overall profitability.
9. Conclusion
The data-driven Six Sigma process is a proven methodology for organizations striving to improve quality, efficiency, and customer satisfaction. By leveraging data at every stage of the DMAIC cycle, businesses can make more informed decisions, minimize defects, and drive continuous improvement. Whether you're in manufacturing, healthcare, or service industries, implementing a data-driven Six Sigma process can be a game-changer for your operations.
Note: IndiBlogHub features both user-submitted and editorial content. We do not verify third-party contributions. Read our Disclaimer and Privacy Policyfor details.