Guide to Implement Barcode Technology in your Warehouse
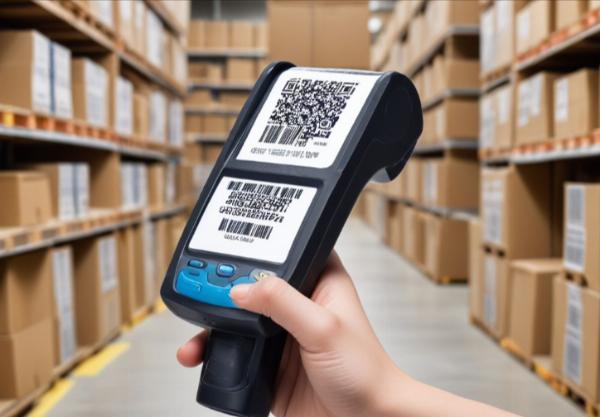
When it comes to managing a warehouse, keeping track of all your inventory manually can be a nightmare. This is why an increasing number of warehouse managers have been automating various processes for improved efficiency. One such technology that has revolutionized the warehousing sector is barcode scanning.
Deploying a barcode system not only makes it much easier to track and manage your warehouse’s inventory accurately but can also offer significant cost savings. Here is an in-depth guide to integrating barcodes into the operations of your warehouse, such that you can make the most of the technology.
In this article, we will dive into how barcodes can help, the different barcode types used in warehouses, and a step-by-step guide to implementing them.
Importance of barcode technology in warehouse management
First things first, let’s find out how the implementation of barcode technology can help you step up your warehouse management game. It’s more than just a way to record information – it’s a technology that can help streamline warehouse management, cut costs, and increase worker productivity. Here’s why warehouse managers should consider adopting barcode technology if they haven’t already.
- Streamlined workflow: Implementing barcodes in your warehouse can help streamline operations by enhancing accuracy, automating data capture, and speeding up various processes. It also allows warehouse managers to better organize their warehouse layout and inventory.
- Improved productivity: By automating otherwise tedious processes with barcode technology, warehouses can assign their workers to other tasks that require human attention. This improves the overall productivity of the operations significantly.
- Reduced costs: While manual data entry is error-prone and can incur a lot of additional costs (in case of a mistake), this is not an issue with barcode technology. Leveraging barcode scanning can eliminate or reduce clerical and operational expenses.
- Time-saving: With reduced errors, quicker order processing, automated data entry, and a streamlined workflow, barcode technology can save you a great deal of time. Once again, this contributes to the warehouse’s operational efficiency, saving a lot of time and making it more profitable.
Types of barcodes used in warehouses
One of the biggest perks of barcodes is that they can be used to collect and store a wide variety of data. Let’s explore which barcodes are popularly used in warehouse management.
1D Barcodes
- Code 39: This versatile 1D barcode encodes numbers, letters, and a handful of special characters. Ideal for labeling items that require alphanumeric data, Code 39 is particularly popular in the military and automotive industries.
- Code 128: Capable of encoding 128 characters, Code 128 barcodes are perfect for packing and shipping labels due to their high data density.
- UPC: Universal Product Code (UPC) is one of the most commonly used consumer barcodes. Capable of identifying a specific product and its manufacturer using 12 digits, it’s popularly used on products that would later be shipped to retail locations.
- EAN Code: This 1D barcode is more like a European version of UPC, with striking similarities. However, it is slightly more geared towards POS applications.
2D Barcodes
- QR Code: With its ability to store large volumes of data, including graphics and URLs, this is easily the most popular 2D barcode. QR codes have a capacity of 7,089 numeric characters or 4,269 alpha-numeric characters and offer quick access to product information in dynamic warehouse environments.
- Data Matrix: This 2D barcode is one of the best choices for encoding detailed information on small components and products, thanks to its small size and high data capacity.
- MaxiCode: Warehouses that are involved in shipping and receiving major parcel delivery and shipping activities often choose MaxiCode. This barcode is specifically designed to track and sort packages at high speed.
Steps to Implement Barcode Technology in Your Warehouse
Implementing barcode technology in a warehouse requires you to plan ahead and make several informed decisions. Here’s a detailed step-by-step guide to the process.
Step 1: Assessing the needs, planning based on the goals, and preparing for barcode implementation
As with the case of implementing most modern technologies, you’d have to start by assessing the barcoding needs and challenges at your warehouse. In addition to warehouse processes and goals, this also extends to your operations and production departments.
Defining your goals
You’d have to plan the barcode implementation based on your goals, which may include:
- Quicker inventory tracking
- Improving accuracy
- Enforcing standard operating procedures (SOPs)
- Reducing the training time needed to prepare new recruits
- Listing SKUs and variants
It would be smart to list all existing and potential SKUs and their respective variants. A convenient way to go about it is to key each SKU number and its variants into a database. While you’re at it, you may also include some additional data for each unit, such as the purchase costs, measurements, vendor information, a physical description, etc.
Configuring your centralized software platform
As you prepare to implement barcodes in your warehouse, it’s important to configure your centralized software platform or the warehouse management system. The barcode reading solution can be connected to the platform for real-time data synchronization later.
This way, you will add more capabilities to the system, such as real-time inventory tracking, accurate stock counts, handling stock-out situations, expiry products, and more. Also, you will get automatic updates to the system when products are received, picked, or shipped.
Step 2: Selecting the right barcode technology for your warehousing needs
As described earlier, there’s a variety of barcode technologies to choose from, each of them ideal for specific applications. Once you have shortlisted the barcode types compatible with your software platform, it’s time to choose the one that suits your barcoding needs the best. Warehouse managers have to consider several factors while choosing the barcode design, such as:
- The nature of the inventory
- Product or item size
- Environmental conditions
- Compatibility with the warehouse management system
- Level of detail in the information that needs to be stored
It’s best to choose a barcoding option that’s as simple and logical as possible while covering all your requirements. There’s no need to go for a complicated 2D barcode design when something as simple as UPC barcodes would get the job done.
In this regard, it would also pay off to study the product supply chain. Warehouses working closely with vendors and retailers might want to align their barcode scanning systems with those used across the supply chain by adopting similar coding designs.
Note: Warehouse locations that process retail products might benefit from registering with GS1 – a global organization responsible for standardizing barcodes used among manufacturers, suppliers, and retailers.
Step 3: Barcode Labeling
The effectiveness of a barcode depends largely on the quality and the suitability of its physical medium, i.e., the labels. Now that you have picked a barcode technology of your choice, it’s time to print the barcode labels.
To streamline your barcode implementation, it’s crucial to formulate a standardized labeling plan. Consider how you’d be labeling your existing inventory or new goods received at your warehouse. For instance, you may either label them in batches or simply re-label the entire inventory in one go. It helps to come up with a standard process that covers accurate and consistent labeling of products, such as determining when and how to re-label them or reprint damaged labels.
Step 4: Barcode Scanner Selection
With the labels ready, it’s now time to choose your hardware. Every warehouse has its unique requirements and challenges, which must be taken into account while selecting the barcode scanners. It is imperative to make a well-researched decision with the following factors in mind:
Scanner range
Depending on the layout of your warehouse, you may consider investing in long-range logistics scanners that would allow workers to scan products on elevated racks from ground level. A convenient alternative is to use duplicate barcodes on the ground level.
Connection method
Consider whether you want your barcode scanners to be mobile-attached, computer-attached, or wireless. Some scanners also come integrated with multiple connection methods, offering enhanced versatility.
Scan engine
You’d have to choose a suitable scan engine based on the barcode design you plan to use. Your options include laser scanners, linear image scan engines, and 2D area imagers.
Lastly, make sure to choose a logistics scanner that is compatible with the warehouse management software used at your warehouse.
Step 5: Barcode Reader Software Installation and Configuration
Once you have all the necessary hardware, it’s time to get them ready for use. Pick a suitable barcode reader solution that meets your warehousing requirements. It is critical to ensure that the barcode reader software of your choice is:
- Easy to use with a quick learning curve
- Integrates seamlessly with all your devices
- Compatible with your barcode scanners
- Suits your scanning needs
Warehouse managers looking for specialized barcode scanning solutions can also use custom-developed scanning software. All you need is a comprehensive barcode scanning SDK that is geared specifically towards developing barcode scanning software.
Step 6: Employee Training and Adoption
The final stage in the successful adoption of barcode technology in your warehouse is to train your employees to use it effectively. Proper employee training is crucial to preventing mistakes, confusion, and potential damage to the barcoding hardware due to improper use.
Besides the barcoding hardware, employees must also be trained in using the related software properly for a streamlined workflow. Employees handling specific roles, such as managing the now-automated database, would also require training on relevant platforms and programs. Only when all employees are appropriately trained, a warehouse can adopt barcoding completely and make the most of it.
Conclusion
To sum it up, barcode technology implementation is a comprehensive process that calls for well-informed decisions. From choosing a barcode design to developing your barcode scanning software, every step requires careful deliberation if you are to maximize efficiency and productivity.
Now that you have a thorough understanding of how to go about it, you shouldn’t have much trouble implementing barcode technology in your warehouse.
Â
Note: IndiBlogHub features both user-submitted and editorial content. We do not verify third-party contributions. Read our Disclaimer and Privacy Policyfor details.