Hempcrete Manufacturing Plant Project Report 2024: Setup and Cost
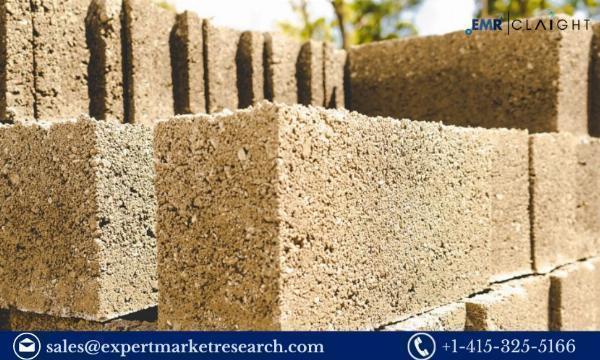
Introduction
The Hempcrete Manufacturing Plant Project Report provides a thorough framework for setting up a production facility dedicated to hempcrete, a sustainable building material made from hemp fibers and lime. As the construction industry increasingly embraces eco-friendly solutions, hempcrete is gaining traction for its exceptional insulation properties and minimal environmental impact. This report covers essential aspects such as market analysis, plant location, infrastructure requirements, raw material sourcing, manufacturing processes, and financial projections. By offering a detailed blueprint, the report aims to guide entrepreneurs and investors in making informed decisions and strategically planning their venture into the hempcrete manufacturing industry.
Market Analysis
Understanding Demand
Hempcrete is used primarily in construction for insulation and creating breathable, energy-efficient building envelopes. Its benefits include:
Sustainability: Hempcrete is made from hemp, a rapidly renewable resource, and lime, which sequesters carbon dioxide as it cures.
Insulation: It offers excellent thermal and acoustic insulation properties.
Health Benefits: Hempcrete helps regulate humidity and improves indoor air quality.
Get a Free Sample Report with Table of Contents @
https://www.expertmarketresearch.com/prefeasibility-reports/hempcrete-manufacturing-plant-project-report/requestsample
Trends and Opportunities
Green Building Movement: Growing awareness and demand for sustainable construction materials drive the adoption of hempcrete. Regulations and incentives for green building practices further boost its appeal.
Market Expansion: As more countries and regions adopt eco-friendly construction standards, the market for hempcrete is expanding globally. North America and Europe are leading in this trend, with increasing interest in other regions.
Competitive Landscape
The hempcrete market is relatively niche but growing. Key players include companies specializing in sustainable construction materials and those focusing on hemp-based products. Differentiation can be achieved through product quality, pricing, and customer education about the benefits of hempcrete.
Plant Location and Infrastructure
Choosing the Right Location
Selecting the ideal location for a hempcrete manufacturing plant involves several factors:
Proximity to Raw Materials: Being close to sources of hemp and lime can reduce transportation costs and ensure a steady supply of raw materials.
Access to Markets: Choose a location with good transportation links to reach target markets efficiently.
Regulatory Environment: Ensure that the location complies with local regulations related to manufacturing and environmental standards.
Infrastructure Requirements
Production Facility: The plant should be equipped with machinery for processing hemp fibers, mixing with lime, and forming the hempcrete blocks or panels. This includes mixers, presses, and curing chambers.
Storage: Adequate storage is required for raw materials like hemp fibers and lime, as well as for finished products. Proper storage conditions help maintain material quality.
Quality Control Laboratory: A laboratory for testing the quality of hempcrete, including its thermal insulation properties, strength, and moisture content, is essential to ensure product consistency and compliance with standards.
Raw Materials and Suppliers
Key Raw Materials
Hemp Fibers: The primary raw material for hempcrete. Sourcing high-quality, sustainably grown hemp is crucial for producing effective and reliable hempcrete.
Lime: Used as a binder in hempcrete. Ensure the lime is of high quality to achieve the desired properties in the final product.
Additives: Depending on specific formulations, additives might be required to enhance properties such as workability or durability.
Supplier Relationships
Building strong relationships with reliable suppliers is essential to ensure a consistent supply of high-quality raw materials. Consider establishing contracts to lock in prices and secure supply.
Manufacturing Process
The production of hempcrete involves several key steps:
Preparation of Hemp Fibers: Hemp stalks are processed to extract the fibers, which are then cleaned and shredded into smaller pieces. This prepares the fibers for mixing with lime.
Mixing: The hemp fibers are mixed with lime and water to create a slurry. The mixing process must be controlled to ensure the right consistency and uniform distribution of materials.
Forming: The mixed hempcrete is then formed into blocks or panels using molds. This step can involve pressing or pouring the mixture into mold forms.
Curing: The formed hempcrete products are left to cure. Curing is a critical step where the lime reacts with the air to harden the mixture and develop its insulating properties.
Quality Control: Throughout the manufacturing process, samples are tested for quality. This includes checking for consistency, strength, insulation properties, and moisture content.
Financial Projections
Initial Investment
Starting a hempcrete manufacturing plant requires significant initial investment. Key expenditures include:
Machinery and Equipment: Costs for mixers, presses, curing chambers, and other production machinery.
Facility Construction: Building or leasing a facility suitable for production and storage.
Raw Materials: Initial purchase of hemp fibers, lime, and any other additives.
Operational Costs
Regular operational costs include:
Labor: Wages for production staff, quality control personnel, and administrative staff.
Raw Materials: Ongoing costs for hemp fibers and lime.
Utilities: Costs for electricity, water, and other utilities required for manufacturing.
Revenue Projections
Revenue will depend on production capacity, market demand, and pricing strategy. Conduct a market analysis to set competitive pricing and estimate potential revenue based on expected sales volumes.
Profit Margins
Analyze profit margins by considering production costs, raw material expenses, and market prices. Efficient production processes and cost management are key to achieving profitable margins.
Risk Management
Identifying Risks
Raw Material Availability: Fluctuations in the availability and price of hemp and lime can impact production. Establish contracts with multiple suppliers to mitigate this risk.
Regulatory Compliance: Stay informed about changes in building regulations and environmental standards that may affect your operations.
Market Demand: Market demand for hempcrete can be influenced by construction trends and economic conditions. Regularly review market trends and adjust strategies accordingly.
Mitigation Strategies
Diversify Suppliers: Work with multiple suppliers to ensure a reliable supply chain.
Maintain Quality Control: Implement rigorous quality control measures to ensure product consistency and compliance with standards.
Monitor Market Trends: Stay updated on industry trends and adapt your business strategies to align with changing market conditions.
FAQ
What is hempcrete and what are its benefits?
Hempcrete is a sustainable building material made from hemp fibers and lime. It offers excellent thermal insulation, improves indoor air quality, and is a carbon-negative material due to the carbon sequestration of lime.
What are the main steps in the hempcrete manufacturing process?
The main steps include preparing hemp fibers, mixing with lime, forming into blocks or panels, curing, and conducting quality control.
How much initial investment is required for setting up a hempcrete manufacturing plant?
Initial investment varies based on plant size and location but includes costs for machinery, facility construction, and raw materials.
What factors should be considered when choosing a location for the plant?
Consider proximity to raw material sources, access to transportation networks, and compliance with local regulations.
How can I ensure the quality of hempcrete products?
Implement strict quality control measures, including testing for consistency, insulation properties, and strength. Use high-quality raw materials and maintain controlled production processes.
What are the major risks in hempcrete manufacturing and how can they be managed?
Major risks include raw material fluctuations, regulatory changes, and market demand shifts. Manage these risks by diversifying suppliers, staying informed about regulations, and monitoring market trends.
Media Contact:
Company Name: Claight Corporation
Contact Person: Lewis Fernandas, Corporate Sales Specialist — U.S.A.
Email: [email protected]
Toll Free Number: +1–415–325–5166 | +44–702–402–5790
Address: 30 North Gould Street, Sheridan, WY 82801, USA
Website: www.expertmarketresearch.com
Aus Site: https://www.expertmarketresearch.com.au/
Note: IndiBlogHub features both user-submitted and editorial content. We do not verify third-party contributions. Read our Disclaimer and Privacy Policyfor details.