How Precast Panel Detailing Improves Structural Integrity
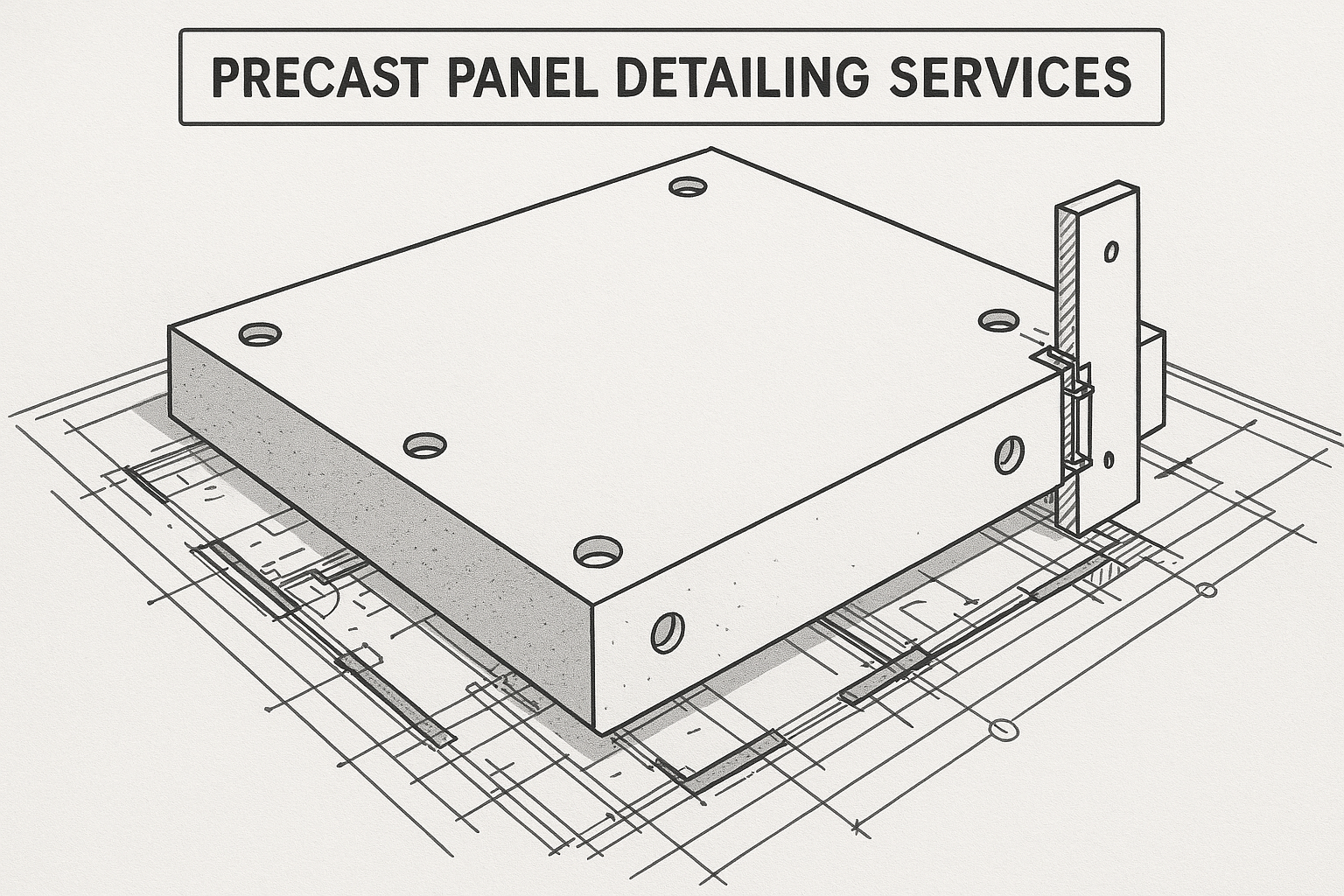
Introduction
The building industry has seen transformative innovations over the past few decades, and precast concrete panels stand out as one of the most revolutionary advancements. These prefabricated components are manufactured in a controlled environment and transported to the site for installation. While the concept of precast is not new, the increasing focus on panel detailing is where the real value emerges. Proper Precast Panel Detailing significantly enhances the structural integrity of buildings, ensuring longevity, safety, and resilience. In this article, we delve deep into how this aspect of engineering impacts the structural robustness of modern structures.
Understanding Precast Panels
Precast panels are concrete components cast in a reusable mold, cured in a controlled environment, and then transported to the site. They come in various forms including wall panels, floor slabs, beams, columns, and facades. The consistency in manufacturing allows for high-quality production with minimal defects. However, the real strength of precast panels lies not just in the concrete itself but in the way they are designed and detailed.
What is Precast Panel Detailing?
Panel detailing involves the precise design and engineering of precast elements to ensure that they can be seamlessly connected, supported, and integrated with other building components. This includes everything from:
- Joint design and placement
- Load transfer mechanisms
- Reinforcement detailing
- Embedded connection hardware
- Tolerance considerations
Coordination with structural and architectural requirements
Effective detailing bridges the gap between design intent and structural performance.
Improving Load Distribution and Transfer
One of the primary ways panel detailing contributes to structural integrity is through optimized load distribution. A well-detailed precast panel ensures that vertical and horizontal loads are effectively transferred to the supporting structure.
By incorporating robust connection systems, such as dowels, anchor bolts, and embedded plates, engineers can ensure that forces such as dead load, live load, wind, and seismic activity are safely directed through the structure without causing localized stress concentrations or failures.
Minimizing Tolerances and Misalignments
Tolerances and misalignments are common challenges on any site. Poorly aligned components can compromise structural performance. Detailed precast panel designs account for tolerances and include alignment aids such as lifting anchors, guide pins, and keyways. These features allow for faster and more accurate assembly, reducing the likelihood of errors that can weaken the structure.
Enhancing Structural Redundancy
Redundancy in engineering refers to the ability of a structure to remain stable even when some components fail. Detailed precast panel designs often include overlapping reinforcements and multiple connection paths. These redundancies serve as a backup, providing an alternate load path that helps the structure maintain integrity under unforeseen conditions, such as an impact or partial collapse.
Improving Seismic and Wind Performance
Precast detailing plays a crucial role in ensuring that structures can withstand dynamic loads from natural forces. In seismic zones, the connections and joints between precast panels are designed to allow controlled movement and energy dissipation. This flexibility reduces the chance of catastrophic failure during an earthquake.
Similarly, in areas exposed to high winds, the detailing must ensure the panels are securely anchored to resist uplift and lateral forces. Attention to anchorage details, reinforcement layout, and joint sealing contributes significantly to structural performance under such conditions.
Waterproofing and Durability
Poor joint detailing can lead to water ingress, which over time can corrode reinforcements and degrade concrete. Effective precast detailing addresses waterproofing by integrating sealants, water stops, and proper joint profiles. This not only preserves structural strength but also increases the service life of the structure.
Durability also extends to protection against environmental factors like freeze-thaw cycles, chemical exposure, and abrasion. Detailing helps ensure that panels can endure these stressors without significant degradation.
Fire Resistance and Thermal Performance
Precast panels are inherently fire-resistant due to their concrete composition. However, detailed panel designs take this further by including fire-stopping measures at joints and around embedded elements. This enhances the structure’s ability to contain fire and prevent it from spreading through structural gaps.
Moreover, good detailing improves thermal insulation by incorporating appropriate materials and design strategies like thermal breaks. This reduces energy consumption and contributes to the sustainability of the structure.
Facilitating Inspection and Maintenance
Detailed design documentation makes future inspections and maintenance easier. By clearly indicating locations of embedded components, connection points, and reinforcements, engineers and facility managers can more easily identify potential issues and plan interventions.
Such foresight in the detailing stage ensures that the structure can be maintained effectively, further extending its lifespan and reliability.
Enabling Modular and Repetitive Construction
Precast detailing supports modular design, allowing for repeated use of panel molds and standard connection systems. This consistency not only speeds up the process but also ensures uniform quality across the structure. Repetition enhances reliability and minimizes variability — a key factor in achieving high structural integrity.
Integration with Building Information Modeling (BIM)
Modern precast detailing is often done using BIM software, which allows for 3D visualization, clash detection, and simulation of loads and sequences. This digital integration enhances accuracy, coordination, and communication among stakeholders, reducing errors and improving overall structural performance.
Conclusion
The role of precast panel detailing in ensuring structural integrity cannot be overstated. From precise load transfer and joint design to redundancy, durability, and digital integration, detailing touches every aspect of a structure’s performance. As structures grow taller, more complex, and more sustainable, the importance of getting the details right becomes increasingly critical.
For expert assistance with precast panel detailing, contact Silicon Engineering Consultant Pty Ltd.
Note: IndiBlogHub features both user-submitted and editorial content. We do not verify third-party contributions. Read our Disclaimer and Privacy Policyfor details.