Jute Bag Manufacturing Plant Project Report 2024: Analyzing Market Trends and Cost
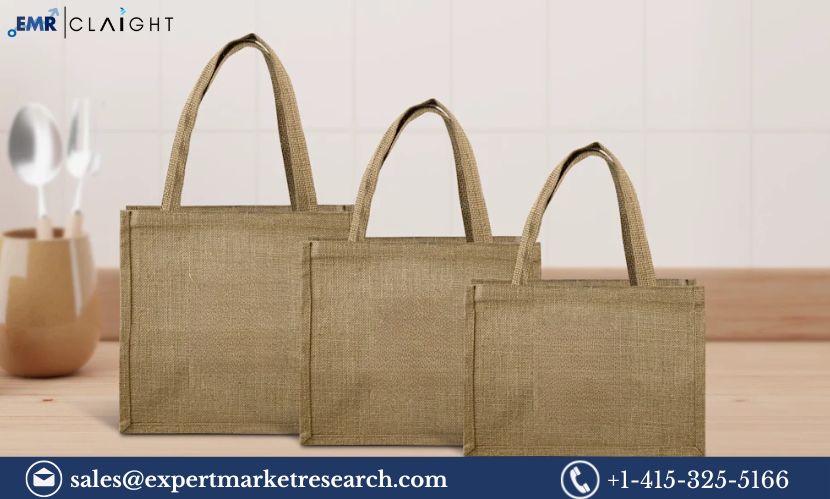
Introduction
The Jute Bag Manufacturing Plant Project Report provides an in-depth analysis of establishing a facility dedicated to the production of jute bags. With increasing environmental awareness and the push for sustainable alternatives to plastic, jute bags have emerged as a popular choice for consumers and businesses alike. This report outlines the essential components for setting up a jute bag manufacturing plant, covering market dynamics, production processes, economic feasibility, and operational considerations.
Overview of the Jute Bag Industry
Jute bags are eco-friendly, biodegradable, and strong, making them an ideal substitute for plastic bags. Jute, a natural fiber derived from the jute plant, is cultivated primarily in countries like Bangladesh, India, and China. The rising demand for sustainable packaging solutions is driving the growth of the jute bag industry globally.
Applications of Jute Bags
Retail: Jute bags are widely used in grocery stores and retail shops for carrying goods, providing an eco-friendly alternative to plastic bags.
Promotional Items: Businesses often use jute bags as promotional products, as they can be customised with logos and designs, enhancing brand visibility.
Agriculture: Jute bags are employed in the agricultural sector for packaging and transporting crops, ensuring durability and breathability.
Fashion and Accessories: Jute bags have found their way into the fashion industry, with designers creating stylish bags for everyday use.
Home DΓ©cor: Jute bags are increasingly used in home dΓ©cor, including storage solutions and decorative items.
Market Analysis
The jute bag market is witnessing significant growth due to heightened environmental consciousness and regulations against plastic bags. This surge in demand presents lucrative opportunities for new entrants in the jute bag manufacturing sector.
Key Market Drivers
Sustainability Trends: The global movement towards sustainability is pushing consumers and businesses to seek out eco-friendly packaging solutions, making jute bags increasingly popular.
Government Regulations: Many governments are implementing bans on single-use plastics, further accelerating the shift towards jute and other sustainable materials.
Consumer Preferences: An increase in consumer awareness about environmental issues is driving demand for biodegradable and reusable products like jute bags.
Competitive Landscape
The jute bag industry consists of established manufacturers and new entrants looking to capitalise on the growing market. To succeed, businesses must focus on product quality, innovation, and effective marketing strategies.
Project Feasibility Study
A comprehensive feasibility study is essential to evaluate the viability of a jute bag manufacturing plant.
Technical Feasibility
Technical feasibility assesses the production process, equipment requirements, and raw material sourcing.
Raw Materials: The primary raw material for jute bags is jute fiber, which needs to be sourced from reliable suppliers to ensure consistent quality.
Production Process: The manufacturing of jute bags involves several steps, including fiber processing, weaving, dyeing, cutting, sewing, and finishing. Each step requires careful attention to detail to produce high-quality bags.
Equipment Requirements: Essential equipment includes jute processing machines, weaving looms, dyeing machines, and sewing machines. Investing in advanced technology will enhance production efficiency and product quality.
Economic Feasibility
An economic feasibility analysis evaluates the financial aspects of the project, including capital investment, operating costs, and revenue projections.
Capital Investment: The initial investment will include land acquisition, facility construction, equipment purchases, and regulatory permits.
Operating Costs: Ongoing expenses will encompass raw material procurement, utilities, labor, maintenance, and marketing. Efficient management of these costs is crucial for profitability.
Revenue Projections: Revenue will depend on market demand, pricing strategies, and distribution channels. Conducting market research to identify potential customers is essential for accurate revenue forecasting.
Operational Feasibility
Operational feasibility focuses on the practical aspects of running the jute bag manufacturing plant.
Location: Choosing a strategic location is vital for minimising transportation costs and ensuring easy access to suppliers and customers.
Workforce: A skilled workforce is necessary for efficient operations. Training programs should be implemented to ensure employees are knowledgeable about production processes and quality control.
Regulatory Compliance: The facility must comply with local and international regulations governing manufacturing processes to ensure safety and environmental protection.
Manufacturing Process
The manufacturing process for jute bags involves several key stages, each crucial for producing high-quality products.
1. Raw Material Preparation
The process begins with preparing raw jute fibers, which are sourced from jute farms. The quality of the jute directly impacts the final product.
2. Fiber Processing
Jute fibers undergo processing, which includes retting, stripping, and drying. This step ensures the fibers are clean and suitable for weaving.
3. Weaving
The processed jute fibers are woven into fabric using looms. The weaving process can produce different types of fabric, depending on the desired texture and strength.
4. Dyeing
If coloured jute bags are required, the woven fabric is dyed using eco-friendly dyes to ensure sustainability.
5. Cutting and Sewing
Once the fabric is prepared, it is cut into specific dimensions and sewn into bags. Quality control measures should be implemented at this stage to ensure uniformity.
6. Finishing
The final step involves finishing the bags, which may include adding features like handles, closures, or decorative elements, and conducting quality checks before packaging.
Quality Control and Regulatory Compliance
Maintaining high-quality standards and adhering to regulatory requirements are critical aspects of jute bag manufacturing.
Quality Control
Raw Material Testing: All incoming raw materials must undergo rigorous testing to confirm their quality and suitability for production.
In-Process Monitoring: Continuous monitoring during the manufacturing process ensures optimal conditions for producing high-quality jute bags.
Final Product Testing: The final product must be tested for strength, durability, and aesthetic appeal before release for distribution.
Regulatory Compliance
Manufacturing Regulations: Compliance with local and international manufacturing regulations is mandatory to ensure the safety and quality of products.
Environmental Regulations: Ensuring compliance with environmental standards is crucial for minimising the impact of manufacturing processes.
Economic Viability
To ensure the economic success of a jute bag manufacturing plant, several factors must be considered.
Cost Management: Implementing cost-effective production methods and optimising resource usage are vital for maintaining profitability.
Market Positioning: Building strong relationships with retailers and distributors can enhance market positioning and drive sales.
Innovation: Investing in research and development to create new and improved jute bag products can provide a competitive edge.
FAQ
What are jute bags?
Jute bags are eco-friendly, biodegradable bags made from jute fiber, commonly used as alternatives to plastic bags.
What are the main applications of jute bags?
Jute bags are used in retail, agriculture, fashion, and home dΓ©cor, offering versatile and sustainable packaging solutions.
How are jute bags produced?
The production process involves raw material preparation, fiber processing, weaving, dyeing, cutting, sewing, and finishing.
What raw materials are needed for jute bag production?
The primary raw material is jute fiber, which should be sourced from reliable suppliers to ensure consistent quality.
What quality control measures are implemented?
Quality control includes raw material testing, in-process monitoring, and final product testing for strength and durability.
Media Contact:
Company Name: Claight Corporation
Contact Person: Lewis Fernandas, Corporate Sales Specialist β U.S.A.
Email: [email protected]
Toll Free Number: +1β415β325β5166 | +44β702β402β5790
Address: 30 North Gould Street, Sheridan, WY 82801, USA
Note: IndiBlogHub features both user-submitted and editorial content. We do not verify third-party contributions. Read our Disclaimer and Privacy Policyfor details.