Redefining Strength and Lightweight Design with Carbon Fiber Composites
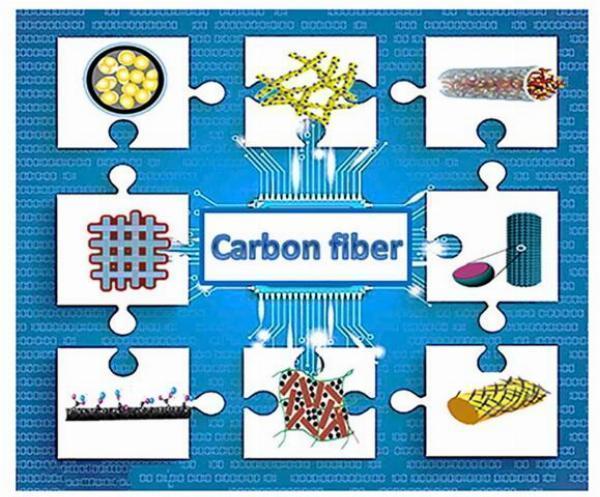
Strength and lightweight design are essential considerations for engineers across numerous industries, ranging from aerospace and automotive to sporting goods and infrastructure. Carbon fiber composites are a class of materials that offer a remarkable balance of strength and lightweight properties, which have made them increasingly popular as an alternative to traditional materials such as metals and polymers.
What is carbon fiber composites?
Carbon fibers are thin, flexible strands composed mostly of carbon atoms. They are extremely strong, rigid, and lightweight, making them an excellent choice for reinforcing materials. According to the preparation precursor, carbon fiber can be further divided into PAN-based carbon fiber, pitch-based carbon fiber and activated carbon fiber.
Carbon fiber composites are made by combining carbon fibers with a polymer matrix, such as epoxy resin, to form composite materials. The manufacturing process for carbon fiber composites involves several key steps, including fiber production, fiber treatment, layup, and curing. At present, the molding methods of carbon fiber reinforced composite materials include dry molding, wet molding, vacuum molding, compression molding, winding molding and resin transfer molding.
Characteristics of Carbon Fiber Composites
Mechanical and dynamic properties: high strength, high modulus, low density, low creep rate, good vibration absorption, fatigue resistance.
Chemical properties: chemically inert, non-corrosive, strong acid, alkali and organic solvent resistance.
Thermal properties: low thermal expansion, low thermal conductivity.
Electromagnetic properties: low X-ray absorption rate, non-magnetic.
Electrical properties: high conductivity.
Lightweight Applications of Carbon Fiber Composites
Aerospace Industry Applications
In order to improve fuel efficiency and reduce emissions while still ensuring structural integrity, the aerospace sector has widely implemented carbon fiber composites. These materials possess remarkable strength and are lightweight, enabling substantial reduction in the weight of aircraft components. Consequently, this leads to enhanced fuel economy, increased capacity to carry payload, and decreased manufacturing expenses. Carbon fiber composite applications in aerospace range from structural components, such as wings, fuselages, and tail sections, to interior panels and seats, offering substantial design flexibility and durability.
Automotive Industry Applications
The implementation of carbon fiber composites has brought considerable advantages to the automotive industry in terms of lightweighting. By utilizing these materials, significant reductions in weight have been achieved for various parts including body panels, chassis, and interior components. This not only leads to improved fuel efficiency and handling but also offers exceptional energy absorption abilities. As a result, carbon fiber composites are well-suited for safety elements like crash structures and impact-absorbing panels.
Sporting Goods Applications
Carbon fiber's high strength, high modulus and lightweight properties allow sports products to reach new performance levels. The performance of golf clubs, tennis rackets, skis, snowboards, hockey sticks, fishing rods, baseball bats and bicycles are all enhanced by carbon fiber reinforcements, and the opportunities for further additions to sports equipment are endless.
Advancements in Surface Modification
The inherent surface properties of carbon fibers, such as their hydrophobicity and low interfacial adhesion, may limit their potential applications in composites. It is worth mentioning that an important challenge in the lightweight design of carbon fiber composites is the need to develop effective surface modification strategies. Effective surface modification strategies for carbon fibers include chemical modification (such as surface-grafting, sizing), electrochemical surface modification, etching modification and surface micro-nano structure modification.
Note: IndiBlogHub features both user-submitted and editorial content. We do not verify third-party contributions. Read our Disclaimer and Privacy Policyfor details.