Hydrophobic Polymers: The Magic of Repelling Water
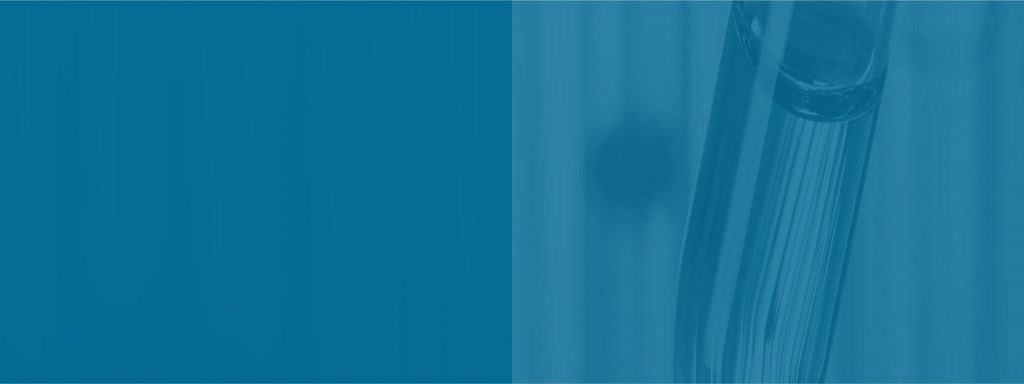
What are the Hydrophobic Polymers?
Hydrophobic polymers are fascinating materials with a wide range of applications. These polymers are water-repelling polymers; a property entrenched in their scientific name—hydrophobic which translates to 'water-fearing'. This article will delve into the biomedical applications of hydrophobic polymers, their use in microelectronics, and the concept of superhydrophobic polymers.
What are the Applications of Hydrophobic Polymers in Biomedical?
Biomedical applications of hydrophobic polymers are numerous. The hydrophobicity of these polymers contributes to their biocompatibility and stability, making them useful in the creation of medical devices and drug delivery systems.
What are the Applications of Hydrophobic Polymers in Biomedical
For instance, polyethylene and polypropylene are hydrophobic polymers that are widely used in sutures, catheters, and artificial joints due to their durability, chemical resistance, and biological inertness. Furthermore, hydrophobic polymers such as poly(lactic-co-glycolic acid) (PLGA) and poly(caprolactone) (PCL) are intrinsic in controlled drug delivery systems. Their main benefit lies in their ability to encapsulate a wide range of drugs and deliver them in a controlled manner over extended periods.
Moreover, hydrogels made from hydrophobic polymers have shown promise in tissue engineering and regenerative medicine. These hydrogels mimic the natural extracellular matrix, promoting cell adhesion, proliferation, and differentiation.
What are the Uses of Hydrophobic Polymers in Microelectronics?
The implementation of hydrophobic polymers in microelectronics is a significant advancement in the field. These polymers possess water-resistant capabilities which make them beneficial in preventing water damage to electrical components. They are utilized in the encapsulation and protection of electronic devices, thus significantly expanding their lifespan and durability.
Further support for this point can be seen through several pertinent examples and data. A study demonstrated the efficacy of hydrophobic polymers in enhancing the lifetime of organic light-emitting diodes (OLEDs). The polymer layer was found to increase the operational lifetime of the devices by more than 20 times. Its moisture resistance also improved the performance consistency of the OLEDs, leading to stable and optimal operations.
In addition, the efficiency of hydrophobic polymers in microelectronics chips was reported by the research conducte. The scientists created a high-performance plastic that can be used to substitute conventional, but more expensive, protective coatings like parylene. The experiments showed that such hydrophobic polymers erect a protective shield against moisture, therefore diminishing the risk of damage caused by dampness.
The importance of Hydrophobic Conformal Coating in protecting printed circuit boards (PCBs) against moisture and contamination is comfirmed. The hydrophobic polymers easily apply and cure at room temperature, which lowers cost, and are impressively bendable, which reduces PCB stress.
Furthermore, hydrophobic polymers are extensively employed in solar photovoltaic (PV) modules as encapsulants because of the same water resistance characteristics. A study has proven that hydrophobic polymers effectively counter Potential Induced Degradation (PID).
Applications:
Industrial field: The super-hydrophobic surface coating film of a lotus leaf with a micro-nano double microstructure can be prepared on the metal surface by traditional mechanical treatment and dispersion of nano-silica. The contact angle of the coating film is up to 173°, which can be widely used in large-scale facilities such as building exterior walls. In addition, the superhydrophobic coating film is widely used in gene transmission, microfluidics, lossless liquid transportation, anti-pollution and anti-oxidation with its unique properties.
Agricultural field: The rapid development of greenhouse vegetables urgently requires a large area of the hydrophobic film. Using the principle of phase separation, a general-purpose plastic can be used as a raw material to prepare a large area of a hydrophobic film with good adhesion. In addition, using a sol-gel process at room temperature, a hydrophobic surface can also be constructed with super-large molecular silicone.
Optical field: For some optical instruments, the self-cleaning function is particularly important, so a lot of researches has emerged on super-hydrophobic, non-reflective or highly reflective super-hydrophobic surfaces. In order to obtain the light transmittance of the surface, the particles constituting the rough surface structure must be smaller than the wavelength of visible light. Some researchers have prepared a super-reflective silver mirror surface with super-hydrophobic properties by controlling the silver mirror reaction, making it possible to prepare a super-hydrophobic base surface while ensuring high reflectivity.
Biomedical field: In the biological field, bioadhesion on the surface of the substrate is a complex phenomenon, which includes many different interactions between organic matter and the interface. There are some researchers immersed the prepared hydrophilic/superhydrophobic surface in the protein solution, and the superhydrophobic part formed an air layer. This "separation wall" prevents the cell from contacting the surface, forming a separation area, and living cells can grow freely on the hydrophilic surface. In clinical treatment, the hydrophobic surface exhibits anti-cell adhesion properties. For example, a partially fluorinated and biocompatible polyurethane surface is used to test the adhesion to platelets. Experiments have shown that compared with the strong adhesion of ordinary polyurethane surface to platelets, the surface with super-hydrophobic properties has almost no adhesion to platelets.
Life field: The hydrophobic fabric not only requires high water repellency, but also ensures the principle of non-toxicity and comfort. Therefore, super-hydrophobic fabrics can be woven into fabrics, for example, block polymers formed from polycaprolactone, styrene and dimethylsiloxane can be made into fibers. Because of their excellent water repellency and low rolling angle, they are the preferred spare materials for textiles with hydrophobic and self-cleaning functions.
Note: IndiBlogHub features both user-submitted and editorial content. We do not verify third-party contributions. Read our Disclaimer and Privacy Policyfor details.