The Evolution and Technology of Snus Packing Machines
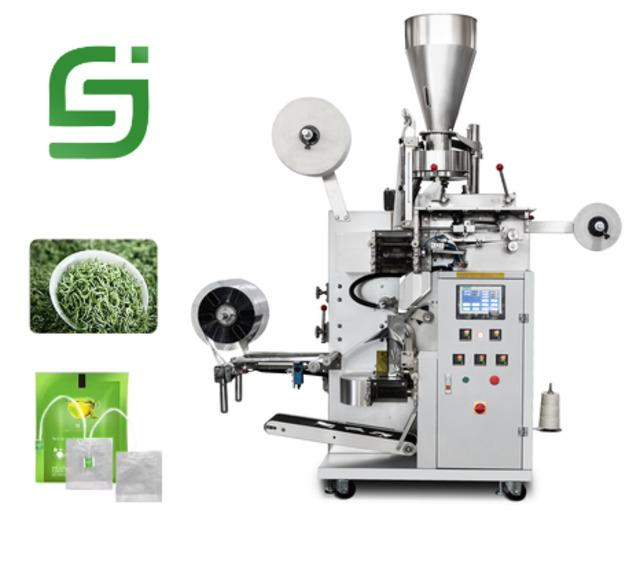
Introduction
Snus, a moist powder tobacco product originating from Sweden, has gained popularity worldwide, necessitating advancements in its manufacturing processes. Central to the production of snus is the packing machine, a critical component that ensures efficiency, consistency, and compliance with regulatory standards. This article explores the evolution and technological innovations of snus packing machines, highlighting their pivotal role in the industry.
Early Developments in Snus Packing
Early snus packing machine were rudimentary, designed primarily for manual operations. These machines relied on basic mechanical mechanisms to portion and pack snus into pouches or containers. The emphasis was on simplicity and reliability, as manufacturers sought to meet growing demand while maintaining product quality.
Automation and Precision Engineering
With advancements in automation and precision engineering, snus packing machines evolved significantly during the late 20th century. Automated processes replaced manual labor, improving efficiency and reducing production costs. Modern machines utilize computer-controlled systems to accurately measure and pack snus, ensuring consistent product weight and quality.
Innovative Materials and Packaging Designs
The development of innovative materials and packaging designs revolutionized snus packing machines in the 21st century. Manufacturers introduced materials that enhance moisture retention and flavor preservation, prolonging snus shelf life. Moreover, ergonomic designs in packaging allow for enhanced user convenience and portability, catering to diverse consumer preferences.
Regulatory Compliance and Safety Standards
Stringent regulatory compliance and safety standards have driven advancements in snus packing technology. Machines are equipped with features to ensure hygiene, traceability, and compliance with health regulations. Automated cleaning systems and quality control measures mitigate contamination risks, safeguarding product integrity and consumer health.
Integration of Industry 4.0 Technologies
The integration of Industry 4.0 technologies represents the latest frontier in snus packing machine innovation. IoT (Internet of Things) connectivity allows real-time monitoring of production metrics and predictive maintenance scheduling. Artificial intelligence and machine learning algorithms optimize packing processes, improving efficiency and reducing downtime.
Future Trends and Sustainability Initiatives
Looking ahead, future trends in snus packing machines focus on sustainability and environmental responsibility. Manufacturers are exploring biodegradable materials and eco-friendly packaging solutions to reduce carbon footprint. Additionally, energy-efficient designs and recycling initiatives aim to minimize waste and resource consumption throughout the production lifecycle.
Conclusion
In conclusion, the evolution of snus packing machines mirrors the dynamic growth of the snus industry itself. From manual operations to automated precision engineering and IoT integration, these machines have continually adapted to meet evolving consumer demands and regulatory requirements. As technology advances, the focus remains on efficiency, quality, and sustainability, ensuring that snus packing machines continue to play a crucial role in the global tobacco market.
2. Weekly Inspection and Maintenance
Perform a detailed inspection of the machine on a weekly basis to identify any signs of wear, tear, or malfunctioning parts. Check the condition of seals, gaskets, and bearings for signs of deterioration or leaks. Lubricate moving parts according to manufacturer specifications to reduce friction and prolong component life. Replace worn-out parts promptly to prevent unexpected breakdowns during production.
3. Deep Cleaning Procedures
Periodically schedule deep cleaning sessions to remove stubborn residues and maintain sanitation levels. Use approved cleaning agents and disinfectants suitable for food-grade equipment. Disassemble components such as hoppers, chutes, and filling heads for thorough cleaning. Scrub components with soft brushes or use high-pressure water jets for effective residue removal. Allow all cleaned parts to air dry completely before reassembling the machine.
4. Calibration and Adjustment
Regularly calibrate the machine to ensure accurate weighing and packaging of powders. Use calibrated weights or test powders to verify the accuracy of filling and sealing operations. Adjust settings such as fill volumes, sealing temperatures, and conveyor speeds according to product specifications and production requirements. Document calibration procedures and results to maintain consistency and compliance with quality standards.
Note: IndiBlogHub features both user-submitted and editorial content. We do not verify third-party contributions. Read our Disclaimer and Privacy Policyfor details.