Vibrating Tables for 3D-Printed Concrete: Special Considerations
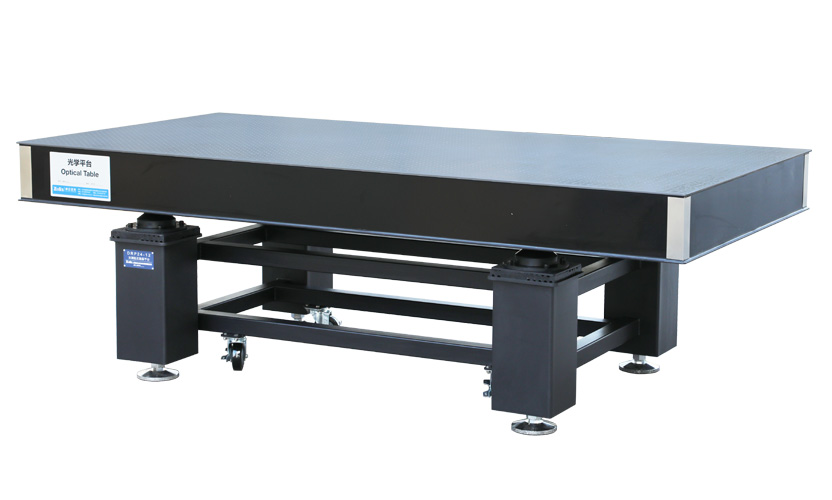
The marriage of 3D printing and concrete has opened doors to architectural possibilities once deemed impossible—curved facades, intricate lattices, and structurally optimized forms that defy traditional casting. But as layer-by-layer extrusion meets cementitious mixtures, a new challenge emerges: ensuring proper compaction without compromising geometric precision. Enter vibrating tables an age-old solution with fresh complexities when applied to additive manufacturing.
Unlike conventional concrete pours, 3D-printed layers are delicate, prone to deformation if over-vibrated, yet vulnerable to weak interlayer bonds if under-compacted. The vibration parameters frequency, amplitude, duration must walk a tightrope between consolidation and structural integrity. Too much agitation, and the printed structure slumps; too little, and voids remain, weakening the final product. This balancing act demands a reevaluation of vibration techniques, especially when dealing with the unique rheology of printable concrete mixes.
The Hidden Physics of Vibration in Additive Manufacturing
Traditional vibrating tables work on a simple principle: mechanical oscillations rearrange particles, expelling air and improving density. But 3D-printed concrete isn’t just poured it’s extruded in precise ribbons, each layer needing to bond seamlessly with the one below. The vibration here isn’t just about compaction; it’s about interfacial healing ensuring molecular cohesion between layers without disrupting their alignment.
This is where the impact hammer, a tool more commonly associated with structural testing, finds an unexpected role. By delivering controlled, localized impulses, an impact hammer can assess the stiffness of freshly printed layers, helping calibrate vibration intensity in real-time. Think of it as a feedback mechanism: too soft, and the vibration needs to increase; too rigid, and the table’s agitation should ease off. It’s a dynamic interplay between force and material response that conventional concrete work rarely demands.
Frequency Matters More Than You Think
Not all vibrations are equal. Low-frequency oscillations (10–30 Hz) are excellent for settling thick, viscous mixes but risk overworking 3D-printed concrete’s finer layers. High-frequency vibrations (50–100 Hz), on the other hand, can achieve consolidation with minimal displacement ideal for preserving intricate geometries. However, they also demand precise control; even slight misalignment can propagate waves unevenly, leading to weak spots or surface blemishes.
Some advanced systems now employ variable-frequency vibrating tables that adapt to layer thickness and material stiffness. Imagine a printer that not only extrudes but also "listens" to the concrete’s response, modulating vibrations like a musician tuning an instrument. This level of synchronization is still emerging, but early trials suggest it could revolutionize how we approach printed concrete’s structural reliability.
The Delicate Dance of Amplitude and Duration
Amplitude the height of vibrational movement is another tightrope. Too high, and layers shift; too low, and air pockets linger. For 3D-printed concrete, the sweet spot often lies in micro-amplitudes (0.1–0.5 mm), just enough to nudge particles into place without disturbing the printed form. Duration is equally critical. Prolonged vibration risks segregation, where heavier aggregates settle while paste rises a disaster for layer adhesion.
Here, pulsed vibration patterns show promise. Instead of continuous shaking, short, intermittent bursts allow partial settling without overheating the mix or inducing fatigue in the printer’s frame. It’s a technique borrowed from metallurgy, where pulsed vibrations refine grain structures in cast metals. Applied to concrete, it could mean stronger interlayer bonds and fewer defects without sacrificing print accuracy.
Material Considerations: Not All Mixes Vibrate Alike
Printable concrete isn’t a single recipe; it’s a spectrum of tailored rheologies. Some mixes rely on superplasticizers for flow, while others use viscosity modifiers to hold shape. Each responds differently to vibration. A highly thixotropic mix, for instance, might fluidize under agitation, losing its printed form, while a stiffer mix could resist consolidation altogether.
This variability demands a bespoke approach. Vibration parameters must align with mix design—something still largely determined by trial and error. However, machine learning is beginning to predict optimal settings based on mix composition, potentially eliminating guesswork. Imagine inputting your material specs and receiving a vibration profile tailored to your exact formulation. That future isn’t far off.
The Overlooked Challenge: Vibration Transmission
In traditional casting, vibration spreads uniformly through a monolithic pour. In 3D printing, the structure evolves layer by layer, meaning vibrational energy must traverse a growing, often irregular, geometry. This can lead to dampening where upper layers receive less agitation than lower ones or resonance, where certain frequencies amplify unpredictably, causing localized over-vibration.
Solutions are emerging. Some systems now use multiple, independently controlled vibration points along the print bed, dynamically adjusting to the structure’s changing profile. Others employ non-contact methods, like electromagnetic pulsers, to deliver energy precisely where needed. The goal is uniform compaction, regardless of shape complexity a hurdle traditional vibrating tables were never designed to clear.
Operator Skill Meets Automation
Even with advanced equipment, the operator’s role remains pivotal. Knowing when to intervene or when to let the system self-correct requires an intuitive grasp of material behavior. This is where hybrid systems shine, blending automated vibration control with manual override options. For instance, if a layer appears under-compacted, a technician might trigger a localized impact hammer pulse to spot-treat the area without disrupting the entire print.
Training is evolving alongside technology. Workshops now teach not just printing techniques but also vibration diagnostics how to "read" a printed layer’s response to agitation, much like a baker judges dough by touch. It’s a skill set that bridges old-school craftsmanship with cutting-edge fabrication.
For a deeper dive into vibration physics and material response, explore MIT’s research on granular material dynamics.
Concluding Up: Vibration as a Precision Tool, Not a Brute Force
The era of one-size-fits-all vibrating tables is ending. For 3D-printed concrete, vibration isn’t just about compaction it’s a precision instrument, as critical as the print nozzle itself. The right frequency, amplitude, and timing can mean the difference between a fragile prototype and a load-bearing marvel.
As the field matures, expect smarter systems that integrate real-time feedback, adaptive algorithms, and perhaps even self-learning vibration profiles. The goal isn’t just to consolidate concrete but to elevate it ensuring that the futuristic promise of 3D-printed construction doesn’t crumble under the weight of its own innovation.
For now, the industry’s task is clear: treat vibration not as an afterthought but as a core pillar of printable concrete’s success. Because in additive manufacturing, every layer counts and how it’s compacted could determine whether the future of construction is built to last.
Note: IndiBlogHub features both user-submitted and editorial content. We do not verify third-party contributions. Read our Disclaimer and Privacy Policyfor details.