Control Valve Working Principle: A Comprehensive Guide
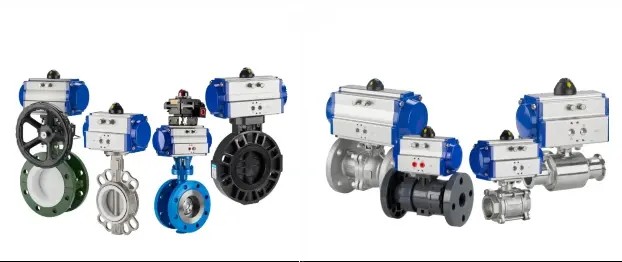
Introduction
Control valves are essential components in various industrial systems, responsible for regulating critical parameters such as pressure, temperature, and flow rate. These China Control Valves are fundamental in ensuring that systems operate efficiently, precisely, and reliably. By adjusting the pressure or flow on either side of the valve, control valves help fine-tune processes, whether manually or automatically. This article explores the working principle of control valves, explaining their operation, components, and applications.
Control valves regulate the flow of fluids—such as gases, liquids, or steam—within a pipeline or system. They achieve this by modifying the size of the flow passage, which in turn controls the rate of fluid movement. This regulation is typically done via actuators, which respond to signals from a control system. By maintaining desired process conditions, control valves ensure optimal performance, safety, and efficiency in industrial applications.
Control Valve Working Principle
A control valve operates by modulating the flow of fluid in a pipeline to achieve specific process conditions, such as maintaining a set flow rate, pressure, or temperature. This is accomplished through a combination of sensors, controllers, and actuators working together to monitor and adjust the system. Below is a breakdown of how a control valve functions:
1. Sensors Collect Real-Time Data
The process begins with sensors installed along the pipeline. These sensors measure critical process variables such as flow rate, pressure, and temperature. For example, in a high-pressure steam system, sensors monitor steam flow and pressure to ensure they remain within specified limits. The data is then transmitted to the control system for analysis.
2. Control System Compares Data to Set Points
The control system—either a Distributed Control System (DCS) or a Programmable Logic Controller (PLC)—receives the sensor data and compares it to predefined set points. These set points represent the desired process conditions. If the data deviates from these set points (e.g., pressure is too low), the control system calculates the corrective action required.
3. Signal Sent to the Actuator
Once a deviation is detected, the control system generates a signal to adjust the control valve. This signal can be transmitted in various ways depending on the type of actuator:
Manual Signals: Used in basic or low-priority systems where an operator manually adjusts the valve using a handwheel.
Pneumatic Signals: Common in industrial settings, pneumatic actuators use compressed air to operate, offering durability and the ability to withstand harsh conditions.
Electric Signals: Modern systems favor electric actuators for their precision and ease of automation, receiving electronic signals to adjust the valve position.
Hydraulic Signals: Hydraulic actuators are ideal for high-force applications, such as large valves, using hydraulic fluid to generate the necessary force.
4. Actuator Adjusts the Valve Position
The actuator converts the control signal into mechanical motion, adjusting the position of the valve stem. This movement changes the size of the flow passage, either:
Narrowing the Valve: To decrease the flow rate.
Widening the Valve: To increase the flow rate.
For example, in a liquid pipeline, reducing the valve opening from 50% to 30% will decrease the flow rate, enabling precise control over the process.
5. Continuous Feedback and Fine-Tuning
A critical aspect of control valve operation is the feedback loop. After adjusting the valve position, the control system monitors the new process variables to ensure they align with set points. If further adjustments are required, additional signals are sent to the actuator for fine-tuning, ensuring process stability within acceptable error limits.
Types of Control Valves
Control valves come in several designs, each suited to specific applications and operating conditions. Some common types include:
Globe Valves: Known for their precise flow control, ideal for applications requiring frequent adjustments.
Ball Valves: Provide quick shut-off capabilities, suitable for on/off control in high-pressure systems.
Butterfly Valves: Compact design, ideal for large-volume flow control in low-pressure systems.
Diaphragm Valves: Used for corrosive or abrasive fluids, as the diaphragm isolates the fluid from valve components.
Plug Valves: Common in systems requiring tight shut-off and moderate flow control.
Applications of Control Valves
Control valves are widely used in various industries, including:
Oil and Gas: Regulating flow in pipelines and refineries for crude oil, natural gas, and refined products.
Power Generation: Controlling steam flow in turbines and managing cooling systems in power plants.
Chemical Processing: Maintaining pressure and temperature in reactors and distillation columns.
Water Treatment: Adjusting flow in filtration systems and managing distribution networks.
Pharmaceuticals: Ensuring accurate dosing and mixing of ingredients in drug manufacturing.
Advantages of Control Valves
Precision: Control valves offer accurate regulation of process variables, ensuring optimal performance.
Efficiency: By maintaining desired conditions, control valves reduce energy consumption and minimize waste.
Reliability: Advanced control systems and feedback mechanisms reduce the risk of system failures.
Versatility: Control valves can be customized to suit a variety of applications and conditions.
Challenges and Considerations
Despite their advantages, control valves face certain challenges:
Cavitation and Flashing: Occurs when the pressure drop causes fluid to vaporize, potentially damaging valve components.
Erosion and Corrosion: Harsh operating conditions, like high temperatures or corrosive fluids, can degrade valve materials.
Actuator Failure: Malfunctions in actuators can disrupt valve operation, requiring regular maintenance.
Complexity: Advanced systems demand skilled personnel for installation, calibration, and troubleshooting.
Conclusion
Control valves are indispensable in modern industrial systems, enabling precise regulation of key process variables like pressure, temperature, and flow rate. By using sensors, control systems, and actuators, control valves maintain process efficiency and reliability. Understanding their working principle helps in selecting the right valve for each application and ensures the smooth functioning of industrial processes.
Control valves are vital in industries such as oil and gas, power generation, and water treatment, where they maintain system stability and performance. By investing in high-quality valves and adopting best practices in operation and maintenance, industries can enhance efficiency, reliability, and cost-effectiveness. As control valve technology continues to advance, it will further improve system capabilities, driving smarter and more efficient processes.Know more about Google SEO Directory
Note: IndiBlogHub features both user-submitted and editorial content. We do not verify third-party contributions. Read our Disclaimer and Privacy Policyfor details.