How to Digitize Complex Logos with Professional Embroidery Digitizing Services
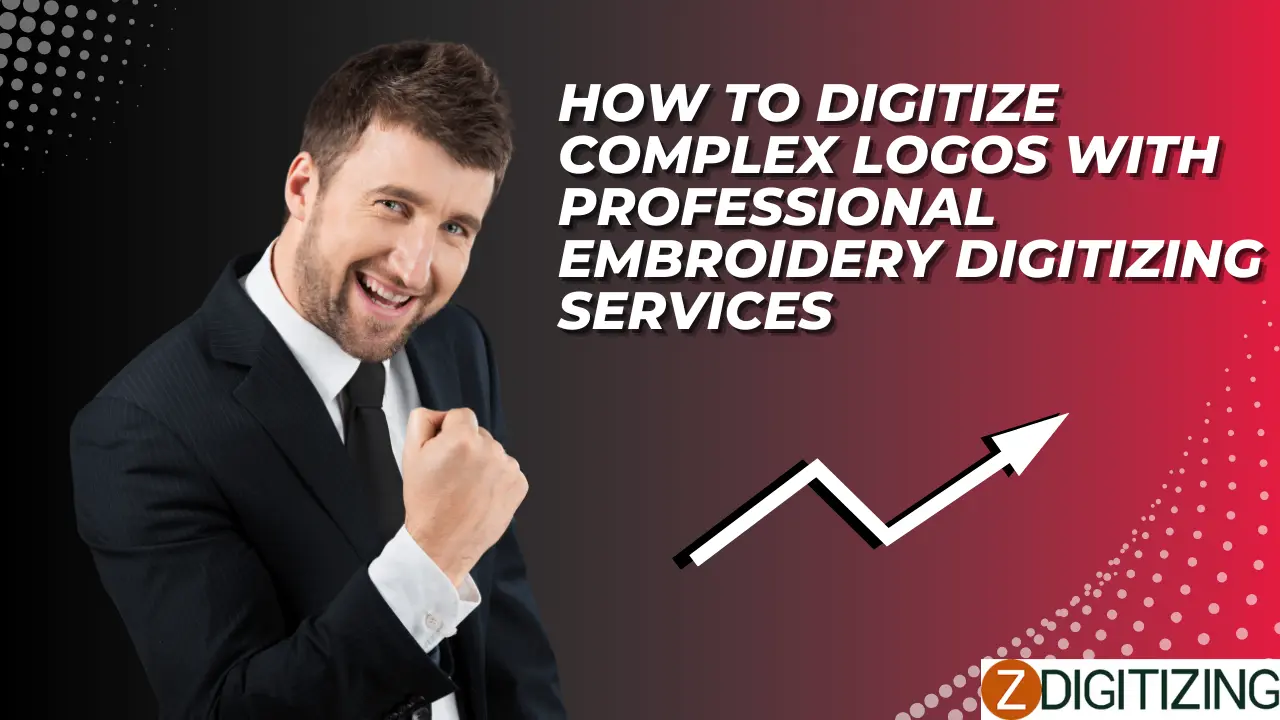
Logos are the face of a brand, and when digitized for embroidery, they must maintain clarity, precision, and aesthetic appeal. However, complex logos with intricate details, fine lettering, and multiple colors can be challenging to digitize. Professional embroidery digitizing services specialize in converting these logos into machine-readable stitch files while preserving their visual integrity.
This guide explores the best practices for digitizing complex logos, the tools used, and the factors that influence high-quality embroidery digitizing.
Understanding the Challenges of Complex Logo Digitization
1. Fine Details and Small Text
- Intricate designs can lose clarity when embroidered, especially on small surfaces.
- Letters smaller than 4mm may become unreadable due to stitch limitations.
2. Color Blending and Gradients
- Embroidery machines use thread colors, which differ from digital color blending.
- Achieving gradients requires careful stitch techniques like blending and layering.
3. Fabric Compatibility
- Different fabrics react differently to stitches, requiring custom adjustments.
- Stretchy or textured fabrics may distort complex designs if not properly stabilized.
4. Stitch Density and Design Scalability
- High-density stitches can lead to thread breakage or puckering.
- Logos must be scalable for various applications like hats, shirts, and jackets.
Step-by-Step Guide to Digitizing Complex Logos
1. Analyze the Logo Design
- Break the design into individual elements.
- Identify areas that require special attention, such as small text and shading.
2. Choose the Right Software
- Use industry-standard digitizing software like Wilcom, Pulse, or Hatch.
- These tools provide advanced features for controlling stitch direction, density, and underlay.
3. Convert the Logo to a Vector Format
- Start with a high-resolution vector file (AI, EPS, SVG) for clarity.
- If using a raster image (JPG, PNG), convert it to a vector format for cleaner digitization.
4. Set Up Stitch Types for Different Elements
- Use satin stitches for smooth edges and small text.
- Apply fill stitches for large, solid areas.
- Use running stitches for fine details and outlines.
5. Adjust Stitch Density and Pull Compensation
- Ensure proper stitch spacing to prevent fabric distortion.
- Add pull compensation to counteract fabric stretching and shifting.
6. Plan the Stitching Order and Pathing
- Arrange elements to minimize jump stitches and trims.
- Start from the center and work outward for better alignment.
7. Incorporate Underlay Stitches
- Underlay provides a foundation for top stitches.
- Choose the appropriate type (edge run, center walk, zigzag) based on fabric type.
8. Test the Digitized File
- Run a test stitch-out on similar fabric to check for accuracy.
- Make necessary adjustments before final production.
Best Practices for High-Quality Embroidery Digitization
1. Simplify When Necessary
- Reduce overly complex elements that won't translate well into embroidery.
- Convert intricate details into stitch-friendly shapes.
2. Use the Right Thread Colors
- Match thread colors as closely as possible to the original logo.
- Consider using specialty threads for metallic or gradient effects.
3. Optimize for Different Fabric Types
- Adjust settings based on the fabric’s thickness and texture.
- Use stabilizers and backing materials to enhance stitch quality.
4. Consider the Logo's Final Size
- Ensure that the logo remains legible and well-defined at all sizes.
- Adjust stitch types and densities for small vs. large-scale embroidery.
5. Avoid Excessive Jump Stitches
- Minimize unnecessary jumps and trims for a cleaner finish.
- Use efficient stitch sequencing to improve embroidery speed.
Common Mistakes to Avoid
1. Ignoring Fabric Type
- Different fabrics require specific digitizing settings.
- What works on cotton may not work on leather or polyester.
2. Overloading with Excessive Stitch Density
- High density leads to thread breakage and machine strain.
- Balance stitch count to maintain fabric integrity.
3. Overcomplicating Small Details
- Fine details may get lost when embroidered.
- Simplify or enlarge small text and intricate elements.
4. Not Testing Before Production
- Always run a test stitch-out to detect issues.
- Adjust settings based on real embroidery results.
5. Incorrect Underlay Application
- Missing underlay stitches can cause distortion and uneven embroidery.
- Proper underlay ensures a stable base for top stitches.
Conclusion
Digitizing complex logos for embroidery requires precision, expertise, and the right tools. Professional embroidery digitizing services ensure that even the most intricate designs are transformed into high-quality stitch files. By following best practices, testing thoroughly, and avoiding common mistakes, you can achieve stunning embroidery results that preserve brand identity and visual appeal.
For businesses and individuals looking for top-tier embroidery digitization, partnering with an experienced service provider is the best way to ensure high-quality, durable, and visually accurate embroidered logos.
FAQs About Digitizing Complex Logos for Embroidery
1. Can all complex logos be digitized for embroidery?
Most logos can be digitized, but intricate details may need adjustments for embroidery compatibility.
2. How do I ensure small text remains readable in embroidery?
Use satin stitches for text larger than 4mm and simplify or enlarge fonts for better clarity.
3. What is the best file format for submitting a logo for digitization?
Vector formats like AI, EPS, and SVG provide the best quality, but high-resolution PNGs or JPGs can also work.
4. How can I achieve gradient effects in embroidered logos?
Gradients can be simulated using stitch layering and blending techniques with multiple thread shades.
5. Why does my embroidered logo look different from the digital design?
Fabric type, stitch density, and thread colors affect the final embroidery outcome. Testing and adjustments help improve accuracy.
6. How long does it take to digitize a complex logo?
The time varies depending on the complexity, but professional services typically take 24-48 hours.
7. Can I resize a digitized logo without affecting quality?
Minor resizing is possible, but significant changes require re-digitization to maintain stitch quality.
8. How do I prevent puckering in my embroidered logo?
Use proper stabilizers, adjust stitch density, and apply correct underlay to prevent fabric puckering.
9. What is pull compensation in embroidery digitizing?
Pull compensation adjusts for fabric stretch during embroidery, ensuring proper alignment and design integrity.
10. Should I use a professional embroidery digitizing service?
Yes, professionals ensure high-quality results with optimized settings for different fabrics and designs.
Note: IndiBlogHub features both user-submitted and editorial content. We do not verify third-party contributions. Read our Disclaimer and Privacy Policyfor details.