The Process of Turbo Recondition: Step-by-Step
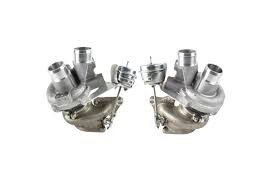
Introduction
In this article, we’ve chosen to illustrate the step-by-step process of turbo recondition, which essentially helps one to restore or bring a used turbocharger back to full performance while maintaining a high level of efficiency. Turbo recondition has proved to significantly help elongate the life of a turbocharger, hence, it is common among users.
Step 1: Initial Inspection and Diagnosis
The very first thing to come necessary to perform in turbo recondition process is a diagnostic inspection, which will require the following steps:
Visual Inspection: Look for any obvious signs of damage, such as cracks, leaks, or evidence of other failures.
Diagnostics: Tests that are used to assess the function of the turbo. Any defects will be made apparent.
Disassembly: Carefully dismantling the turbocharger to examine internal components for wear and tear.
Step 2: Cleaning
After the inspection the turbocharger has to be cleaned, to eliminate carbon deposits, oil deposits and contaminants from the part. Cleaning includes following steps: 1. The first step in turbocharger cleaning is a wash in solvent naphtha or toluene. 2. After that the turbocharger has to be degreased using
Chemical Cleaning: Soaking parts in special solvents to dissolve and remove stubborn deposits.
Ultrasonic Cleaning: Using ultrasonic waves to dislodge dirt and grime from hard-to-reach areas.
Sandblasting: For tougher residues, sandblasting can be used to clean metal surfaces thoroughly.
Step 3: Detailed Component Inspection
Then, each pig gets cut up into parts, and after cleaning, each part is checked carefully in detail to make sure it is up to standard. This includes:
Microscopic examination: Checking components for invisible micro-cracks or wear.
Measurement: Using precision tools to measure components and ensure they meet OEM specifications.
Functional testing of parts such as the turbine wheel and compressor to ensure they work as expected.
Step 4: Replacement of Worn Parts
An inspection would include looking for any parts that have worn or damaged, and would replace these parts: Tires of the Caterpillar are made of fabric and steel belts.
Bearings: These are one of the first to go and will need to be replaced to maximise operation.
Nos 32, 34 and 37 Seals and Gaskets: Fried seals and gaskets are a major cause of oil leaks, and should be replaced.
Turbine and compressor wheels: If necessary, they must be replaced for proper functioning.
Step 5: Reassembly
After all of its parts are cleaned, inspected and replaced if needed, the turbocharger is put together again. Reassembly is a process that needs to be done with care to correctly reinstall all the components in their proper location and firmly hold them. A complete reassembly involves:
Balance: Make sure the turbine and compressor are balanced so that they do not vibrate too much and work more easily.
Lubrication: Applying the correct lubricants to moving parts to reduce friction and wear.
Sealing: Properly sealing the turbocharger to prevent leaks and maintain pressure.
Step 6: Final Testing and Calibration
Supercharged, or turbocharged engines: Carefully, crews assemble the turbocharger components, following the tear down. Once put back together, the turbocharger is tested and tuned to proper specifications:
Performance Testing: Running the turbocharger on a test bench to simulate operating conditions and look for faults.
Calibration: Adjusting the turbo's settings to ensure optimal performance and efficiency.
Quality Control: Next, is the final inspection to verify that all processes have met quality standards and the turbocharger is ready to use.
Step 7: Packaging and Delivery
After the turbocharger has successfully passed inspections, quality is determined and the product will be packed. Proper packing is required to prevent the parts from being damaged. There are three steps to this process. Upchecking, shrink wrapping, and safekeeping. Up checking is the process of examining which turbochargers have been quality-checked and which parts go together. Shrink-wrapping involves wrapping the product in difficult-to-tear poly-bubble wrap for clear identification and safety. The final step is safekeeping where the product is properly stored from vibration, extreme temperature, and dust.
Protective Packaging: Using materials that cushion and protect the turbocharger.
Marking: Make sure the package is properly marked with the correct information including the turbocharger model and serial number.
Documentation: Providing documentation that outlines the reconditioning process and warranty information.
Conclusion
Turbo recondition is a time consumerage take and it is vital to execute all the turbo recondition process correctly because every component is extremely important to the overall working of the turbocharger. Turbo recondition starts from inspecting and verifying how much dirt the turbo is having before being dismantling everything being deeper more inspect on certain components, afterwards will be cleaning followed by precise quality inspect, and lastly be tested on a dyno until certain performance arrived. By knowing the process of turbo recondition, car owner would understand there worth of reconditioning and skill that require to conduct the service correctly besides from saving from exchange or buying new carrying the turbo recondition has a significant contribution to a sustainable approach and concept.
Note: IndiBlogHub features both user-submitted and editorial content. We do not verify third-party contributions. Read our Disclaimer and Privacy Policyfor details.