Tray vs. Packed Distillation Columns: Which is Right for Your Application?
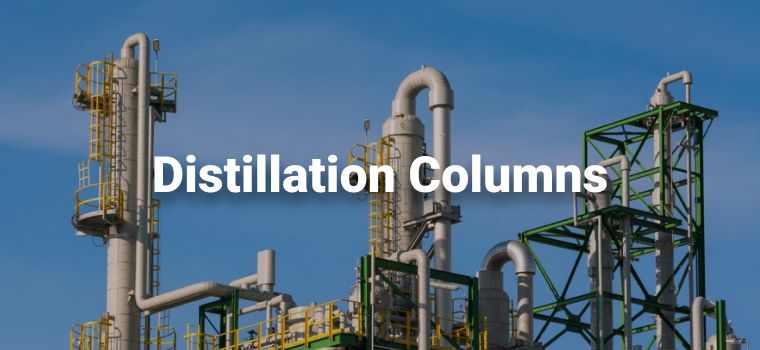
When selecting a distillation system, the choice between tray and packed distillation columns can significantly impact efficiency, effectiveness, and overall operational costs. Both types of columns serve the primary function of separating liquid mixtures based on their boiling points, but they do so in distinct ways. This guide will explore the differences between tray and packed distillation columns to help you determine which is best suited for your application.
Understanding Distillation Columns
Distillation columns are essential in industries such as petrochemicals, pharmaceuticals, and food processing. They utilize the principles of vaporization and condensation to separate components in a liquid mixture. The process relies on the differences in boiling points of the various components, allowing for efficient separation.
Tray Distillation Columns
How They Work
Tray columns consist of a vertical vessel with a series of horizontal plates, known as trays, arranged at different heights. As the vapor rises through the column, it passes through these trays, where it contacts the liquid that flows down from above. This interaction facilitates mass transfer, allowing lighter components to vaporize while heavier ones remain in the liquid phase.
Advantages
High Efficiency: Tray columns are known for their high efficiency in separating components with significant differences in boiling points. This makes them particularly effective for applications where purity is critical.
Ease of Cleaning: The design of tray columns allows for straightforward access, making maintenance and cleaning easier than in packed columns. This is particularly beneficial in industries where product changeovers are common.
Visual Monitoring: Operators can visually monitor liquid levels on the trays, enabling better process control and adjustments as needed.
Disadvantages
While tray columns offer many advantages, they also have some drawbacks. They tend to experience higher pressure drops due to the resistance created by the trays. This can lead to increased energy consumption and operating costs.
Packed Distillation Columns
How They Work
Packed columns, in contrast, are filled with packing materials—such as rings or structured packing—that provide a large surface area for vapor-liquid contact. As vapor rises through the packing, it interacts with the descending liquid, allowing for separation based on boiling points.
Advantages
Lower Pressure Drop: Packed columns generally have lower pressure drops compared to tray columns, which can result in lower energy costs and better overall efficiency.
Versatility: These columns can accommodate a broader range of flow rates and liquid compositions. They are ideal for applications such as gas absorption and separation processes involving more complex mixtures.
Compact Design: The smaller footprint of packed columns makes them suitable for facilities with space constraints. This is increasingly important in modern industrial setups where real estate can be limited.
Disadvantages
However, packed columns also come with challenges. Cleaning can be more difficult due to the packing material, which can trap residues. Additionally, monitoring the flow and separation processes within the packing is less straightforward than in tray columns.
Choosing the Right Column for Your Application
The decision between tray and packed distillation columns should be based on several factors:
Type of Mixture: For mixtures with large boiling point differences, tray columns may be preferable. For closer boiling points or gas absorption applications, packed columns are often more effective.
Flow Rates: Tray columns are suitable for high flow rates, while packed columns excel in lower flow rate applications, especially where energy efficiency is crucial.
Space and Maintenance: If space is a constraint, packed columns offer a compact solution. However, if ease of maintenance is a priority, tray columns may be the better choice due to their accessible design.
Conclusion
Both tray and packed distillation columns have their unique strengths and weaknesses. Selecting the right type for your application involves considering factors such as mixture type, flow rates, and available space. By understanding these differences, you can make a well-informed decision that enhances your distillation processes, ensuring efficiency, effectiveness, and high-quality results
Note: IndiBlogHub features both user-submitted and editorial content. We do not verify third-party contributions. Read our Disclaimer and Privacy Policyfor details.