Ensure Workplace Safety with High-Quality LOTO Stations in Plants
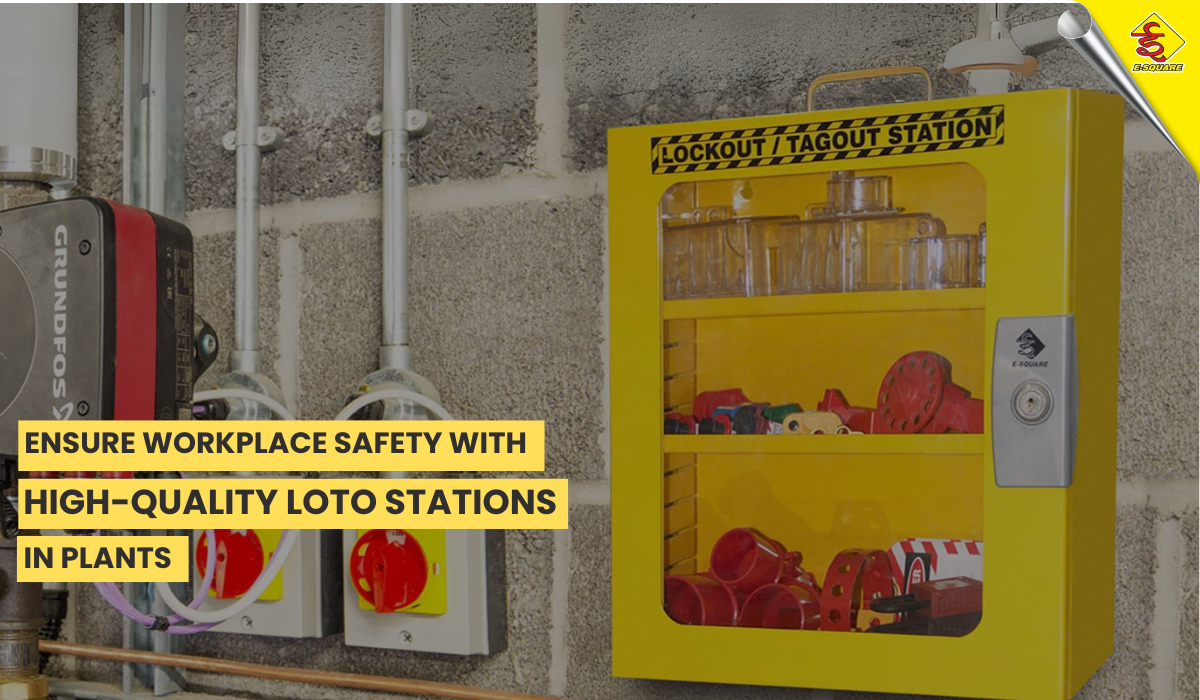
In industrial plants, workplace safety is paramount, especially when dealing with hazardous energy sources during maintenance or repair activities. Lockout Tagout stations are critical tools for controlling these energy sources, preventing accidental equipment startups that could lead to severe injuries or fatalities.
By implementing high-quality LOTO stations, plants can ensure compliance with the Occupational Safety and Health Administration (OSHA) standards, specifically OSHA 1910.147, while fostering a culture of safety. This article explores the importance of LOTO stations, their key features, and best practices for their effective use in industrial settings.
The Importance of LOTO Stations in Industrial Safety:
LOTO stations serve as centralized hubs for storing and organizing lockout tagout devices, such as padlocks, hasps, tags, and circuit breaker lockouts. These stations ensure that all necessary tools are readily accessible, reducing downtime during lockout procedures and promoting consistent safety practices.
OSHA mandates that employers implement LOTO procedures to isolate hazardous energy sources, including electrical, mechanical, hydraulic, and pneumatic systems. Failure to comply can result in penalties, but more importantly, it risks worker safety. High-quality LOTO stations streamline compliance by providing a designated space for standardized, durable devices, ensuring that workers can quickly and effectively secure machinery.
Moreover, LOTO stations enhance accountability. By centralizing equipment, they allow supervisors to monitor usage and ensure that only authorized personnel access the tools. This reduces the likelihood of errors, such as incomplete lockouts or missing tags, which could lead to hazardous situations. A well-organized LOTO station also supports training efforts, as new employees can easily locate and learn to use the tools correctly, reinforcing a plant-wide safety culture.
Key Features of High-Quality LOTO Stations:
When selecting LOTO stations for industrial plants, certain features are essential to ensure reliability and compliance:
Durability and Weather Resistance: Stations should be made from robust materials like heavy-duty steel or impact-resistant plastic to withstand harsh industrial environments, including exposure to chemicals, dust, or moisture.
Clear Organization: High-quality stations include labeled compartments or hooks for padlocks, hasps, tags, and other devices, making it easy to identify and access tools quickly.
Portability or Wall-Mount Options: Depending on the plant’s needs, stations should either be portable for flexibility or wall-mounted for permanent, accessible placement near hazardous equipment.
Capacity for Multiple Users: Stations should accommodate enough devices to support multiple workers, especially in large plants where simultaneous lockouts may occur.
Visibility and Signage: Brightly colored stations with clear OSHA-compliant signage, such as “Lockout Station” or “Authorized Personnel Only,” enhance visibility and deter unauthorized access.
Non-Conductive Materials: For electrical safety, components like padlocks and lockout devices should be made from non-conductive materials like nylon or thermoplastic to prevent accidental shocks.
These features ensure that LOTO stations are practical, safe, and aligned with OSHA requirements, contributing to a safer workplace.
Best Practices for Implementing LOTO Stations:
To maximize the effectiveness of LOTO stations, plants should adopt the following best practices:
Conduct Regular Training: Employees must be trained on LOTO procedures, including how to use devices stored in the station. Annual refresher courses and hands-on demonstrations can reinforce proper techniques.
Standardize Equipment: Use uniform padlocks, tags, and lockout devices to avoid confusion. For example, red padlocks might indicate electrical lockouts, while yellow tags could signal maintenance in progress.
Perform Routine Inspections: Regularly check LOTO stations to ensure all devices are in good condition and fully stocked. Replace damaged or missing items immediately to maintain readiness.
Develop Clear Procedures: Establish written LOTO procedures specific to each piece of equipment in the plant. Include these in the station or nearby for quick reference.
Audit Compliance: Conduct periodic audits to verify that workers are following LOTO protocols correctly. Use station logs to track device usage and identify potential gaps in training or compliance.
Encourage a Safety Culture: Promote open communication about safety concerns and reward adherence to LOTO protocols. A visible, well-maintained LOTO station can serve as a constant reminder of the plant’s commitment to safety.
Overcoming Common Challenges:
Despite their benefits, implementing LOTO stations can present challenges. For instance, workers may bypass procedures due to time constraints or lack of awareness. To address this, plants should integrate LOTO training into onboarding and emphasize the consequences of non-compliance, such as OSHA fines or workplace accidents.
Another challenge is ensuring stations remain fully stocked. Assigning a designated safety officer to monitor and restock stations can mitigate this issue. Additionally, in large plants, multiple stations may be needed to ensure accessibility across different areas, which requires careful planning to balance cost and coverage.
Conclusion:
High-quality LOTO stations are indispensable for ensuring workplace safety in industrial plants. By providing a centralized, organized, and durable solution for lockout tagout devices, these stations help plants comply with OSHA regulations, protect workers from hazardous energy, and foster a culture of safety.
By prioritizing durable materials, clear organization, and employee training, plants can maximize the effectiveness of their LOTO programs. Regular inspections, standardized equipment, and proactive audits further enhance safety outcomes. Investing in well-designed LOTO stations is not just a regulatory requirement but a critical step toward safeguarding lives and maintaining operational efficiency in industrial environments.
Note: IndiBlogHub features both user-submitted and editorial content. We do not verify third-party contributions. Read our Disclaimer and Privacy Policyfor details.